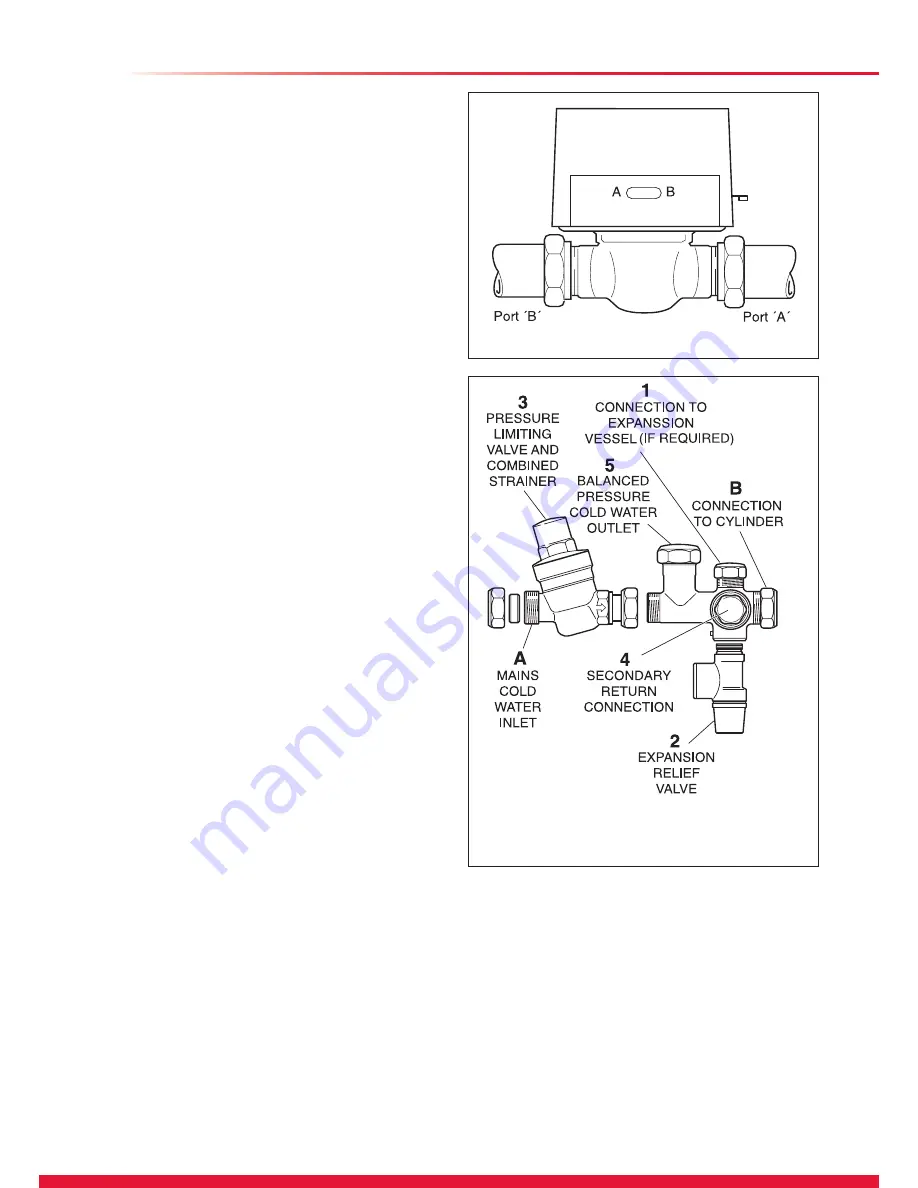
4.6 Installation procedure
IMPORTANT.
With regards to the Manual Handling
Operations, 1992 Regulations, the following lift operation
exceeds the recommended weight for a one man lift.
Unpack the Glow-worm cylinder and check the contents refer
to section 3.
NOTE:
Position the Glow-worm cylinder in accordance with
section 4.1 Siting.
4.7 Central Heating pipework
To prevent the Glow-worm cylinder from overheating the 2
port motorised valve supplied with the cylinder must be fitted
to the Central Heating flow to the indirect coil, see diagram
4.4.
4.8 DHW system Pipework
Connect the two cold water control valves together as shown
in diagram 4.7, ensuring that the orientation of the valves,
when installed in the cold mains supply, allows the 15mm
outlet of the expansion relief valve to be connected to the
tundish.
Install the discharge pipe from the expansion relief valve so
that it has a continuous fall to outside in a safe and visible
position where it will be unaffected by frost.
Never cap or block the outlet of the expansion relief valve.
Activate the expansion relief valve regularly to prevent from
calcification.
Provide a cold water mains supply to the Glow-worm cylinder.
To ensure optimum performance from the Glow-worm
cylinder, and particularly in installations where the balanced
pressure cold water outlet (5, diagram 4.7) is to be used, the
pipework provided from the building mains stop valve to the
Glow-worm cylinder should be minimum 22 mm copper tube.
Install a drain valve in the cold mains supply between the
Glow-worm cylinder and the cold water control valves at the
lowest point.
Install the assembled cold water control valves, see diagram
4.7 in the cold mains supply at a convenient position adjacent
to the Glow-worm cylinder, ensuring adequate space exists
for service access and allow for connection of the discharge
pipe from relief valves.
The discharge pipes should be discharging either directly or
via a manifold to a tundish. The relief valves must be within
600 mm of the tundish, see diagram 4.5.
The Glow-worm cylinder is provided with an external
expansion vessel.
Connect the expansion vessel to the installed water controls
by either:
i.
Screwing the vessel directly into the control assembly at
the purpose provided connection (4, diagram 4.7) or,
ii.
Connecting the vessel to the control assembly via
copper pipe or a suitable approved flexible connection hose,
ensuring that the vessel is adequately supported (1, diagram
4.7).
NOTE:
An optional ”Remote Expansion Vessel Mounting Kit”
is available for use with Glow-worm cylinders (Accessory No.
0020000000). The kit contains a wall mounting bracket.
Connect the balanced pressure cold water supply (if required)
to the cold water control pack, see diagram 4.7.
NOTE:
In areas where the mains water pressure is high (4
bar or above) the cold water supply to a bath or shower mixer
valve can be taken from the balanced pressure cold water
outlet (5, diagram 4.7) of the cold water controls. This will
ensure that both hot and cold supplies to the mixer valve are
at approximately the same pressure. The cold water supply
for all other terminal fittings should be tee'd into the cold water
supply pipework to the Glow-worm upstream of the cold water
controls.
4 Installation
IMPORTANT:
No isolation valve shall be installed between
the assembled cold water control valves and the cylinder.
12555
12556
Connect the DHW outlet pipework to the 22 mm domestic hot
water outlet on the Glow-worm cylinder. Continue with 22 mm
size pipe to the first tee fitting after which 15 mm pipework
should be adequate. If the pipe runs are of excessive length or
there are several terminal fittings supplied, extend the length
of pipework in 22 mm.
Connect the secondary return if required, as described in
section 3.2 Secondary Return.
4.9 Safety valve discharge pipework
Connect the temperature/pressure relief and expansion
relief valves to the tundish using 15mm pipe and install the
discharge pipework from the tundish in accordance with
section 4.4 Discharge Pipework.
Diagram 4.6
Diagram 4.7
12
Summary of Contents for SS 115
Page 11: ...4 Installation FUNCTIONAL DIAGRAM 12553 FUNCTIONAL DIAGRAM 12554 Diagram 4 4 Diagram 4 5 11 ...
Page 16: ...12560 Diagram 7 1 FAULT A 7 Fault Finding 16 ...
Page 17: ...12561 Diagram 7 2 FAULT B 7 Fault Finding 17 ...
Page 18: ...7 Fault Finding 12564 FAULT C Diagram 7 3 18 ...
Page 19: ...7 Fault Finding 12562 FAULT D Diagram 7 4 19 ...
Page 20: ...20 ...
Page 21: ...21 ...
Page 22: ...COMMISSIONING CHECKLIST MAINS PRESSURE HOT WATER STORAGE SYSTEM ...