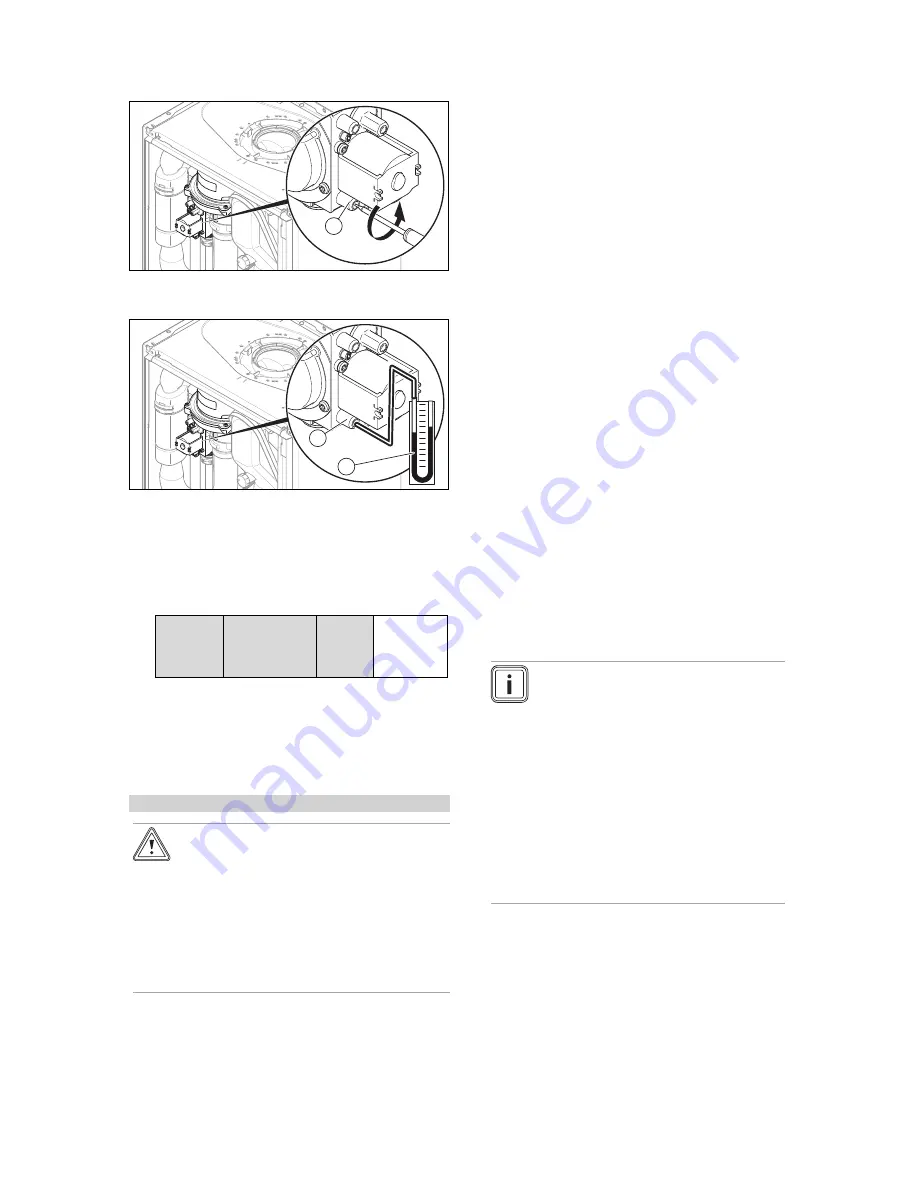
Start-up 7
0020200967_00 SUSTAIN ..s Installation and maintenance instructions
19
1
2.
Use a screwdriver to undo the sealing screw on the
measuring nipple
(1)
of the gas valve.
1
2
3.
Connect a pressure gauge
(2)
to the measuring nipple
(1)
.
4.
Open the gas isolator cock.
5.
Start up the product with check programme P.01.
6.
Measure the gas connection pressure against atmo-
spheric pressure.
Permissible connection pressure
Great Bri-
tain
Natural gas
G20
1.7
… 2.5 kPa
(17.0
… 25.0 mbar)
7.
Switch off the product.
8.
Close the gas isolator cock.
9.
Remove the pressure gauge.
10. Tighten the screw on the measuring nipple
(1)
.
11. Open the gas isolator cock.
12. Check the measuring nipple for gas tightness.
Conditions
: Gas connection pressure
not
in the permissible range
Caution.
Risk of material damage and operating
faults caused by incorrect gas connec-
tion pressure.
If the gas connection pressure lies outside
the permissible range, this can cause oper-
ating faults in and damage to the product.
▶
Do not make any adjustments to the
product.
▶
Do not start up the product.
▶
If you are unable to remedy the fault, contact the gas
supply company.
▶
Close the gas isolator cock.
7.9.2
Checking the leak-tightness of the flue gas
system and for flue gas recirculation
1.
Check that the flue gas system is intact, in accordance
with British Gas TB 200.
2.
If the flue gas installation is longer than 2 m, a flue gas
recirculation test is strongly recommended. This test
must be carried out in accordance with the instructions
below.
3.
Use the air analysis point
(1)
to check for flue gas recir-
culation.
4.
Use the flue gas measuring instrument.
5.
If you discover CO or CO2 in the fresh air, search for a
leak in the flue gas system or for the flue gas recircula-
tion.
6.
Eliminate the damage.
7.
Repeat the above-mentioned test to determine if the
fresh air contains CO or CO2.
8.
If you cannot eliminate the damage, you must not start
up the boiler.
7.9.3
Thoroughly flushing the heating installation
("hot")
1.
Operate the appliance until the boiler and the heating
system are up to temperature.
2.
Check the heating system for leaks.
3.
Connect a hose to the drain valve located at the lowest
position of the heating system.
4.
Shut off the boiler, open the drain valve and all purge
valves on the radiators and allow the water to flow out
of the heating system and the boiler quickly and fully.
5.
Close the drain valve.
6.
Fill and purge the heating installation. (
→
Page 18)
7.
Re-fill the system until the system design pressure of
0,1 MPa (1,0 bar) is attained.
Note
The actual reading on the digital pressure
gauge should ideally be 0,05 MPa (0,5 bar)
plus an additional pressure corresponding
to the highest point of the system above the
base of the boiler
–
10 m head equals an ad-
ditional 1 bar reading on the pressure gauge.
The minimum pressure should not be less
than 0,1 MPa (1 bar) in any installation. If
the system is to be treated with an inhibitor it
should be applied at this stage in accordance
with the manufacturer’s instructions. Further
information can be obtained from Sentinel,
Betz Dearborn Ltd., Tel: 0151 420 9595, or
Fernox, Alpha
–
Fry technologies. Tel: 0870
8700362.
8.
Fit the front panel. (
→
Page 10)
7.9.4
Checking the CO
₂
content
1.
Start up the product with the check programme
P.01
.
2.
Wait at least five minutes until the product reaches its
operating temperature.
3.
Measure the CO
₂
content at the flue gas analysis point.
4.
Compare the measured value with the corresponding
value in the table.
Summary of Contents for ENERGY 12s-A
Page 47: ......