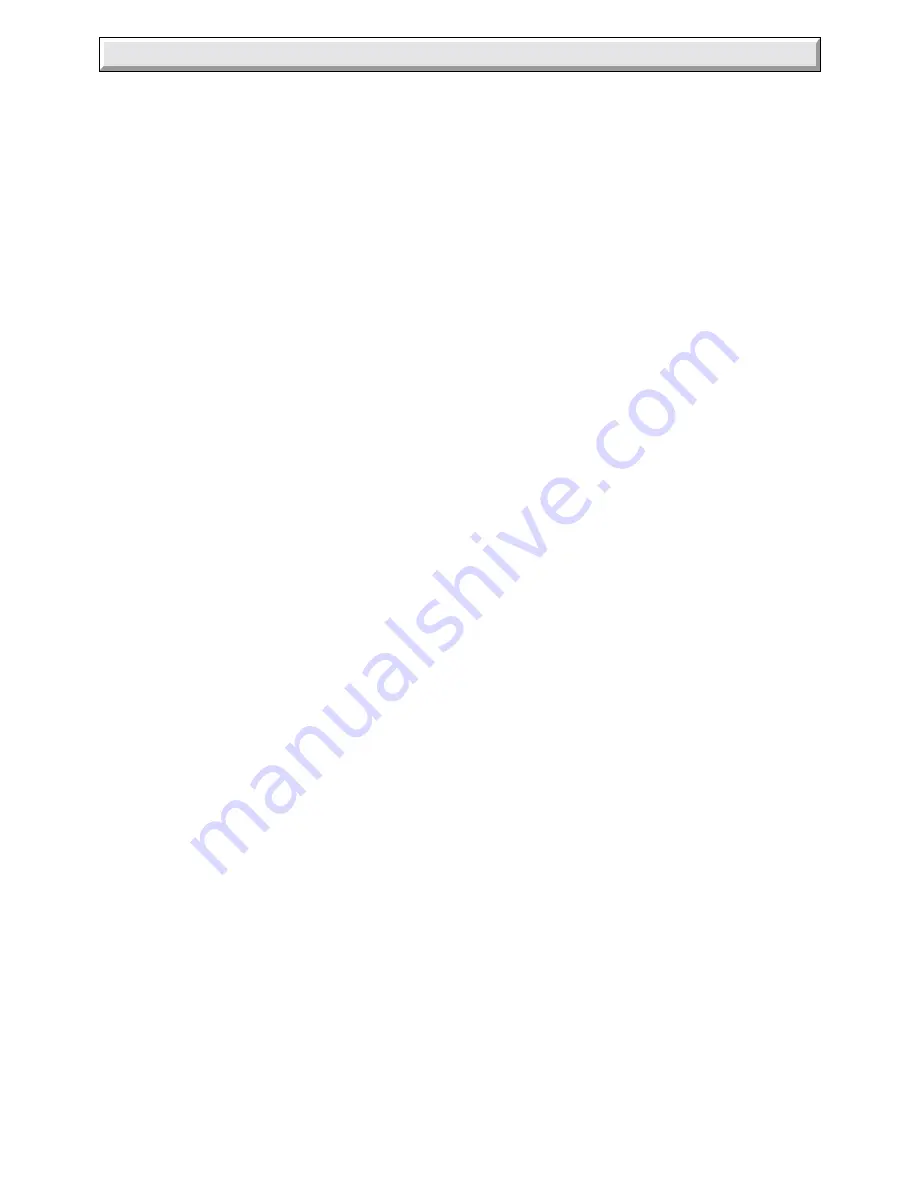
3
2000225024C
References in these instructions to British Standards, Statutory
Regulations and Requirements apply only to the United Kingdom.
For Ireland the rules in force must be used.
These instructions consist of two parts, Installation and Servicing
Instructions for the Back Boiler Unit and the Guarantee
Registration Card. User, Installation and Servicing Instructions
for the specified fire are supplied with the firefront.
The boiler is for use only with a specially designed Glow-worm
Gas firefront, see table 1.
This boiler is NOT suitable for fitting to precast flues.
The boiler is delivered in one pack which contains all the parts
necessary for the installation.
if installing the back boiler unit and the fire front at the same time
please read both sets of instructions before starting.
IMPORTANT NOTICE
This boiler is for use only on G20 gas.
The back boiler unit is fitted with a flue blockage safety device
which will shut it down if there is a lack of oxygen resulting from
a build up of combustion products. The flame on the pilot light
will become unstable and lift up off the sensing device, this will
deactivate the gas valve via the p.c.b., cutting off the gas supply.
If the back boiler unit shuts down frequently for no apparent
reason the first things to check are the chimney and air inlets
into the room. Any problems found must be put right, by a
competent person, and a full operational test carried out before
the fire is used again.
The flue blockage safety device incorporates the electrode,
pilot assemblies and sampling tube assembly in conjunction
with P.C.B.
The flue blockage safety device MUST NOT be adjusted or
disconnected. It must be serviced strictly in accordance
with the instructions in this book. Any unauthorised
interference could result in the device failing to operate,
creating a potentially dangerous situation. If replacing, use
only the correct and approved parts.
Wherever possible, all materials, appliances and components
to be used shall comply with the requirements of applicable
British Standards.
Where no British Standard exists, materials and equipment
should be fit for their purpose and of suitable quality and
workmanship.
Sheet Metal Parts
WARNING. When installing or servicing this back boiler care
should be taken when handling the edges of sheet metal parts
to avoid any possibility of personal injury.
Refer to Manual Handling Operations, 1992 Regulations.
1.1 Statutory Requirements
The installation of this back boiler unit must be carried out by a
competent person in accordance with the current issue and
relevant requirements of:
Manufacturer’s instructions, supplied.
The Gas Safety (Installation and Use) Regulations, The Building
Regulations, The Building Standards (Scotland) Regulations,
applicable in Scotland, Local Gas Undertaking, Bye-laws of the
Local Water Company, The Health and Safety at Work Act,
Control of Substances Hazardous to Health, The Electricity at
Work Regulations and any applicable local regulations.
1 General
Detailed recommendations are contained in the current issue of
the following British Standard codes of practice,
BS1251, BS5440 Part 1 and 2, BS5449, BS5546, BS5871,
BS6798, BS6891, BS7593, BS7671.
Manufacturer’s notes must not be taken as overriding statutory
obligations.
1.2 Data
See diagram 1.1, Range Rating table for friefronts and Table 1.
Gas connection
Rc
1
/
2
(
1
/
2
inBSPT)
Water connection
Rc1
Electrical supply
230V~50Hz fused 3A
Weight, about
38kg (83.6lb)
Water content
2.18Litres (0.48gall)
Injector
3.35mm
Dimensions, except as noted, shown on diagrams are in
millimetres.
Data Label: On the base of the boiler next to the electrical
control box.
The Seasonal Efficiency Domestic Boilers UK (SEDBUK) for
LFE and radiant fires is 78.8%, for Inset fires it is 79.5%.
The value is used in the UK Government’s Standard Assessment
Procedure (SAP) for energy rating of dwellings. The test data
from which it has been calculated have been certified by B.S.I.
1.3 Gas Supply
The gas installation must be in accordance with the current
issue of BS6891.
The supply from the governed gas meter must be of adequate
size to provide a steady inlet working pressure of 20mbar (8in
wg) at the boiler.
Do not use pipe of a smaller diameter than Rc
1
/
2
(
1
/
2
BSP) inlet
or 15mm, see diagram 1.1 for position of gas connection.
The gas meter must be capable of passing natural gas at the
following rate: 85ft
3
/h (2.4m
3
/h).
This rate is in addition to all other natural gas appliances
supplied from the same meter.
It is recommended that the gas supply enters the builder’s
opening on the right hand side.
If the gas supply enters from the left hand side it will be
necessary to route and insulate the pipe behind the combustion
chamber before final fixing.
On completion test the gas installation for soundness using the
pressure drop method and suitable leak detection fluid, purge
in accordance with the above standard.
1.4 Electrical Supply
WARNING. This boiler must be earthed.
All system components shall be of an approved type and shall
be connected in accordance with the current issue of BS7671
and any applicable local regulations.
Connection of the boiler and system controls to the mains
supply should be through a common isolator , a double pole
isolating switch, fused 3A, should be used, having a minimum
contact separation of 3mm in both poles.
Alternatively, a fused 3A 3pin plug and unswitched shuttered
socket both to the current issue of BS1363 may be used.
Wiring to the boiler must be PVC (85
o
C) insulated type to the
current issue of BS6500 Table 9, not less than 0.75mm
2
(24/
0.20mm)..
Summary of Contents for BBU 45/4
Page 31: ...31 2000225024C ...