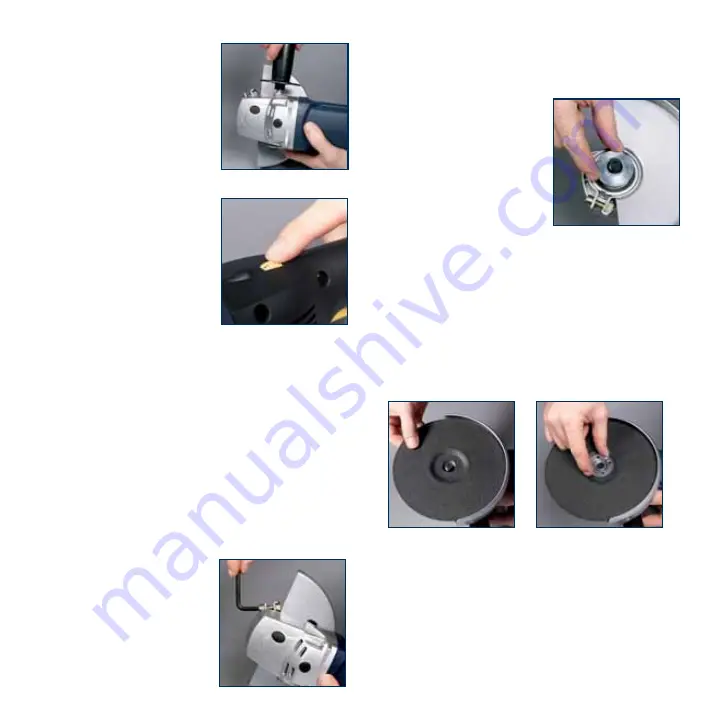
Setting up
Multi position front handle
Screw the multi position front
handle (9) into the most
suitable mounting point (6)
(left side, right side or at the
top) to suit the task on hand.
Variable Speed
The POL1450 is fitted with a
variable speed dial (3) that
allows you to adjust the speed
to suit the application and
material. The tool operates
between the speeds of
1500 RPM – 6500 RPM, the
higher the number on the
variable speed dial, the higher
the speed. For polishing and buffing applications it is
recommended that a lower speed (1500 RPM) is used. For
sanding applications it is recommended that a medium
speed (3500 RPM) is used to provide efficient material
removal, for grinding applications the maximum speed
(6500 RPM) should be selected.
Warning.
Do not operate the machine with a polishing
bonnet attached above 1500 RPM (Position 1 on the
variable speed dial).
Operation in grinder mode
Fitting the grinding disc
Switch off the tool and disconnect it from the power
supply.
Warning.
The guard must
always be attached and secured
to the tool during angle
grinding applications.
1. Fit the guard (15) onto the
spindle collar and rotate to
the required working
position. The closed side of the guard must always be
facing the operator.
2. Insert the guard securing
screw and tighten using the
matching nut. Use the
supplied Allen key to securely
tighten the screw.
3. Place the inner flange (16)
onto the spindle making sure
it fits securely.
4. Ensure that the non-threaded
inner flange is on the spindle
and located correctly. The two machined flat sections
on the inner flange must face the angle grinder and
locate in the matching positions on the spindle.
5. Place the grinding or cutting disc on top of the inner
flange ensuring the bore fits into the raised centre
section of the flange.
6. Place the outer flange (17) over the spindle. For
grinding and cutting discs which are 5mm or thicker, fit
the outer locking flange (17) with the raised centre
section inwards towards the wheel. This helps to locate
the disc on the flanges.
7. For grinding and cutting discs which are less than 5mm
in thickness, fit the outer locking flange with the raised
centre section facing outwards, away from the disc.
8. Failure to fit the outer flange correctly as detailed
above will result in the outer flange tightening on the
inner flange but not clamping the disc.
9