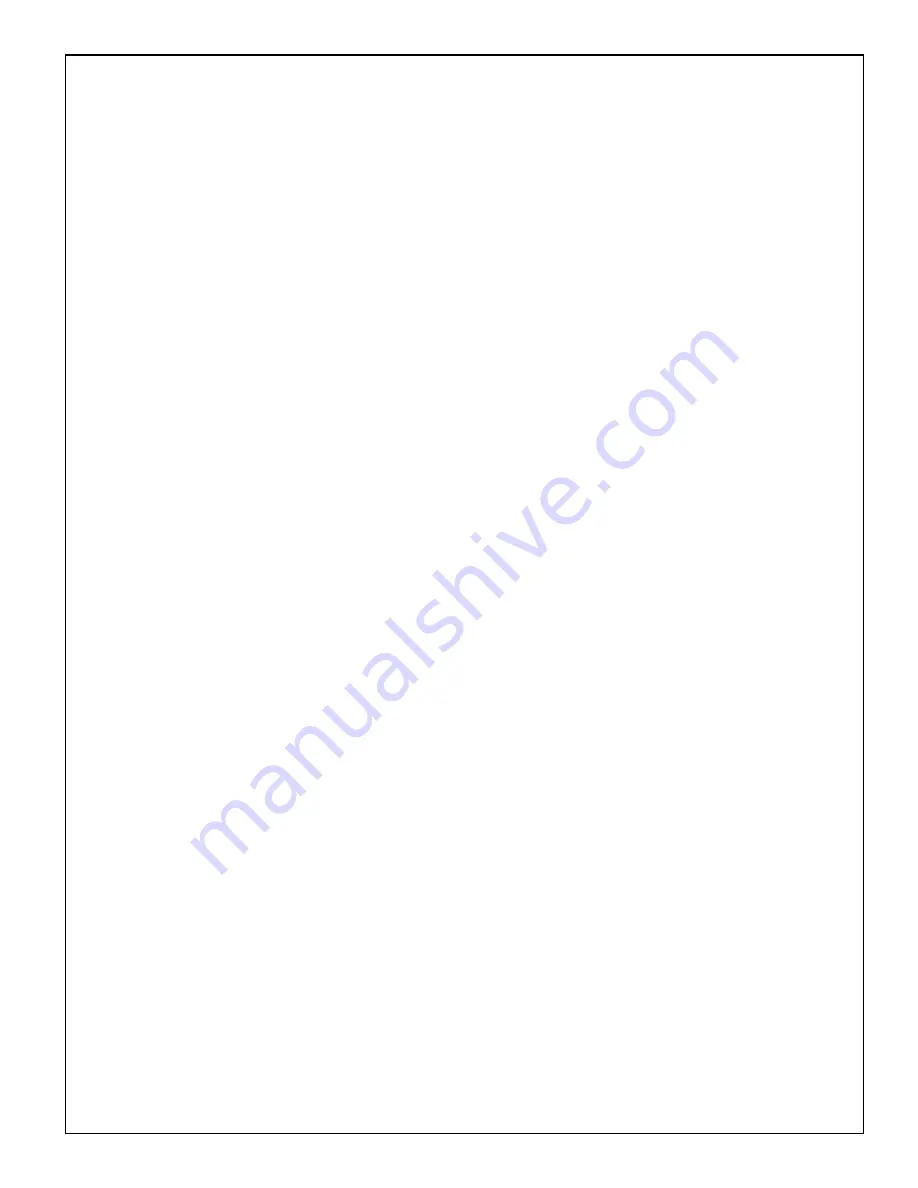
GLENTEK Inc. 208 Standard Street, El Segundo, California 90245, U.S.A. (310) 322-3026
17
If a larger current of the same polarity was commanded to the output transistors (see fig. 4.3B) the ON-time
widths of B and D would automatically increase to provide more current.
From the previous examples it is easy to understand why this output transistor switching technique is re-
ferred to as pulse-width modulation.
To change the magnitude and polarity of the current flow in the motor, the pulse widths of the opposite pairs
of transistors are modulation. The frequency at which these output transistors are switched ON and OFF is re-
ferred to as the “carrier frequency.”
After realizing how the PWM amplifier output works, it becomes apparent that some inductance must be
added to the motor circuit to prevent excessively high AC ripple current and heating in the servomotor. Consult
a Glentek applications engineer for recommended inductance.
Now that we have a good understanding of how the current is provided from an “H TYPE” pulse-width
modulated (PWM) bridge, let’s analyze the operation of the current loop.
4.5 CURRENT- LOOP OPERATION:
Please refer to figure 4.1 for a diagram of the current loop. In control electronics the symbol Sigma (with the
circle around it) is referred to as a “summing junction”. The manner in which this summing junction operates is
as follows:
The current-command signal (also referred to as the velocity-error signal when received from the output of
the velocity loop, as shown in fig. 4.1) is added to the current-feedback signal. The signal resulting from this ad-
dition, is referred to as the “current-error” signal. This current-error signal is fed into the current amplifier, which
in turn produces a current in the motor. A voltage which is proportional to the motor current is developed across
Rs (shunt resistor). This voltage is referred to as the “current-feedback” signal. The current in the motor in
creases until the current-feedback signal is exactly equal in magnitude, but opposite in polarity, to the current-
command signal. At this point the current-error signal drops to zero, and the actual current is equal to the com
manded current. If anything happens to disturb either the current-command signal, or the current-feedback sig-
nal, the same process occurs again until the current-feedback signal is equal in magnitude to the current-
command signal, but opposite in polarity.
The type of loop described above is referred to as a “servo loop” because the current servos about a com-
manded value.
We are surrounded in our everyday lives by a multitude of servo loops. For example, many of today’s luxury
cars have what is called “automatic climate control”. To operate this servo loop, you set the climate control to
the temperature that you wish to be maintained in the interior of the car (current-command signal). The selected
temperature is then summed with the actual temperature from a thermometer (current-feedback), and the out-
put (current-error signal) activates either the heater or the air-conditioner until the actual temperature as measured
by the thermometer (current-feedback signal) is equal in magnitude, but opposite in polarity, to the set tempera-
ture.
4.6 VELOCITY-LOOP OPERATION:
Please refer to figure 4.1 for a diagram of a typical velocity loop. The velocity-loop’s operational description
is analogous to the current-loop description, except for the fact that the input signal is called the Velocity Com-
mand and the feedback signal from the DC tachometer is called the Velocity Feedback.
CHAPTER FOUR: THEORY OF OPERATION