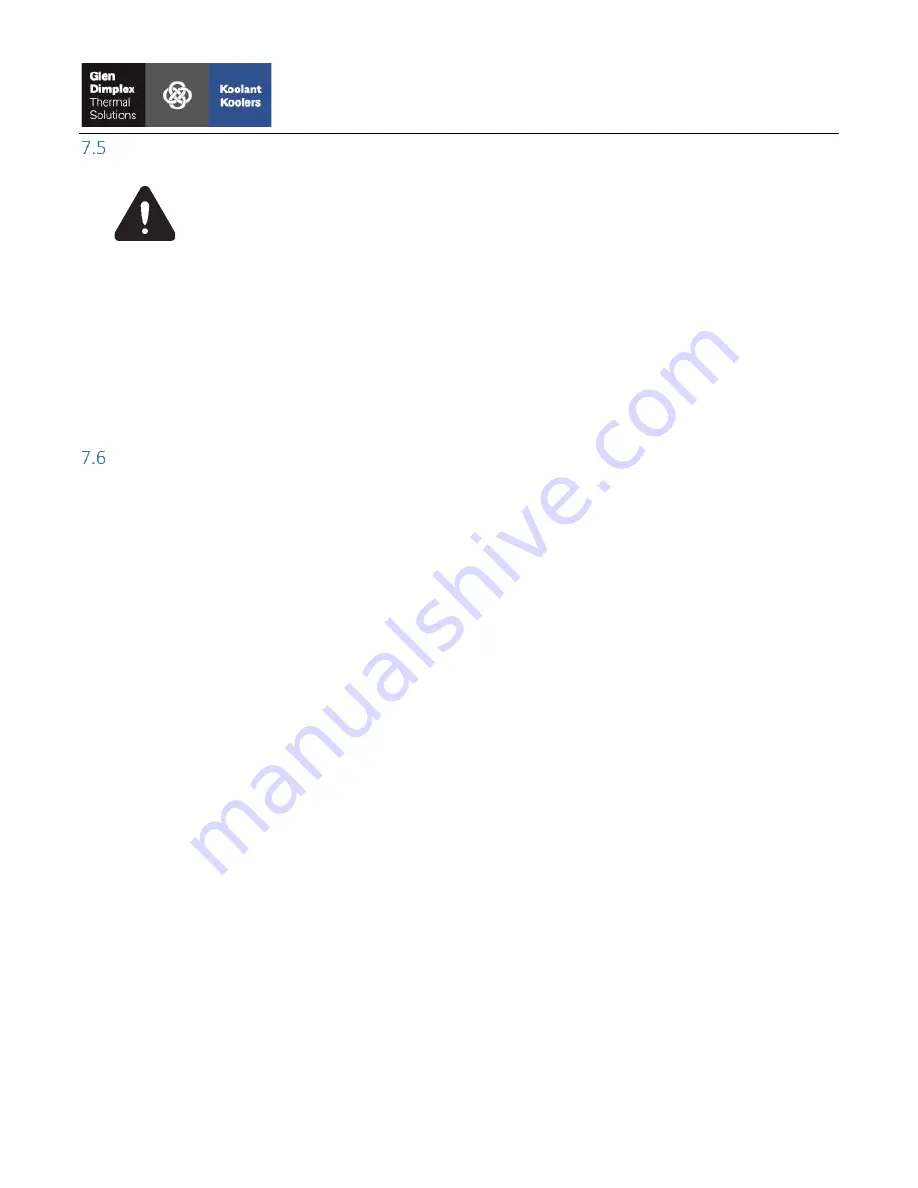
Operation
27
Refrigeration High Pressure Switch
WARNING
The refrigeration discharge lines may be extremely hot
–
avoid contact. Resetting
of the refrigeration high pressure switch should only be performed by qualified
personnel equipped with proper safety gear and tools.
The chiller’s refrigeration circuit is equipped with a mechanical, high pressure switch that disengage
s (trips) the
refrigeration circuit when dangerously high pressures occur to prevent damage to the refrigeration system. If
the switch has tripped it can be reset by performing the following steps:
1.
Access the chiller’s air intake/filter side (refer to sect
ion 6.1).
2.
Depress the red reset button until a tactile click is felt.
3.
Reinstall the air intake filter(s) before restarting Chiller.
Maintenance
Establishing a proper maintenance schedule will extend the lifetime of the chiller. A suggested checklist has
been provided in section 7.6.1.
7.6.1
Suggested maintenance checklist.
Items in this list should initially be performed on a weekly basis to determine how often they need to be
serviced. Time between servicing must be re-established when operating conditions have changed.
7.6.1.1
Inspect and clean the condenser coil and air intake filter
Excessive buildup of dirt, oil, and/or other debris on the condenser coil and air intake filters will cause
reduced air flow rates for heat dissipation leading to lower capacities. Ensure that the fins of the
condenser coil are clean and undamaged. Use compressed air at no more than 120psi (8.3bar) to blow
out the condenser coil and air intake filters in the direction opposite to normal air flow. For the
condenser coil the cleaning air should enter the discharge side and exit from the intake side. If the air
filters cannot be cleaned, then they must be replaced.
7.6.1.2
Inspect the supply pressures
Record the supply pressure after the initial startup and then periodically. If plumbing connections
between the chiller and process have remain unchanged, the supply pressures should remain
constant. An increase in pressure indicates a clogged filter/strainer or buildup of debris in the fittings.
7.6.1.3
Inspect and clean fluid strainer
Fluid strainers protect the brazed plate heat exchanger from becoming clogged. Inspect and clean
strainer after first hour of operation, after first week of operation, and annually thereafter.
Summary of Contents for Koolant Koolers WO2-2-10000
Page 1: ...Original Instructions 800 968 5665 dimplexthermal com User Manual...
Page 17: ...Installation 11 Figure 7 Removal or Doors Blockers 3 8 DOOR BOLT 3 8 BLOCKER BOLT BLOCKER DOOR...
Page 18: ...Installation 12 Figure 8 Removal of Lower Doors LATCHES...
Page 28: ...Operation 22 Figure 10 Controller Restart Warning Figure 11 Controller Home Page...
Page 30: ...Operation 24 Figure 15 Controller On Off Menu Figure 16 Controller Pump Enable Disable Menu...
Page 31: ...Operation 25 Figure 17 Controller Setpoint Menu Figure 18 Controller Alarm Menu...
Page 37: ...Internal Components 31 Figure 20 Door Side PUMP 2 PUMP 1 FLOAT SWITCH...
Page 44: ...Appendix A Plumbing 38 Appendix A Plumbing...
Page 45: ...Appendix B Pump Curve 39 Appendix B Pump Curve...
Page 46: ...Appendix C Refrigeration WO2 2 5000 40 Appendix C Refrigeration WO2 2 5000...
Page 47: ...Appendix C Refrigeration WO2 2 7500 41 WO2 2 7500...
Page 48: ...Appendix C Refrigeration WO2 2 10000 42 WO2 2 10000...