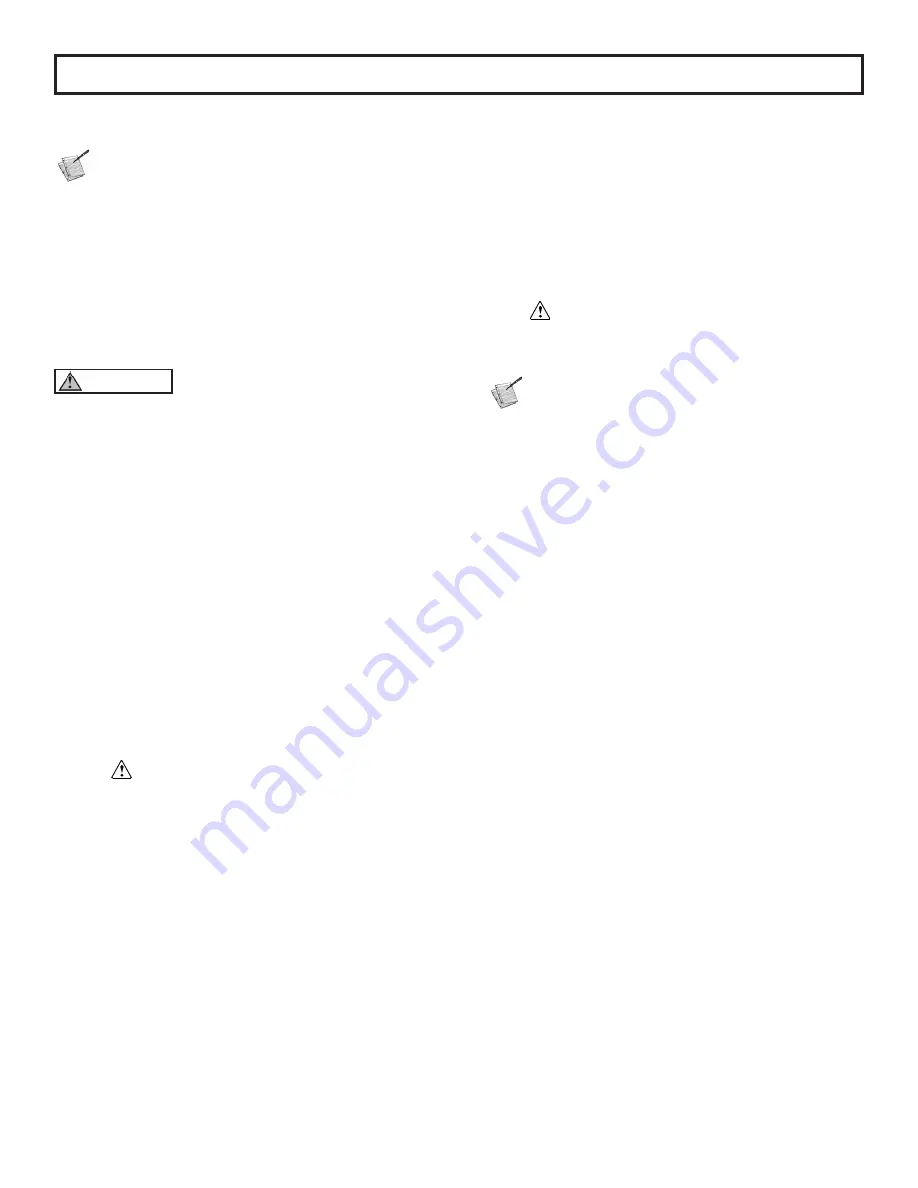
Section 1 - Installation: Equipment Assembly
Guardian Line Installation Guide
GlasCraft Systems are factory assembled. If any
questions arise concerning air or electrical
connections, please refer to illustrations located in
the forward portion of this User Manual or contact
your GlasCraft distributor.
1.
Locate Guardian.
a.
Locate Guardian on a level surface.
b.
Do not expose Guardian to rain.
CAUTION
Bolt Guardian to original shipping palet before lifting.
c.
Use the wheels to move Guardian to a fixed
location, or bolt to shipping pallet and move
with forklift.
d.
To mount on a truck bed or trailer, bolt directly to
truck or trailer bed.
2.
Advanced preparation
a.
Before beginning any installation, ensure that the
applicator has the desired power supply available,
(i.e. 220V single phase / 380V three phase),
within 10 ft. of were the machine is to be placed.
If the machine needs to be further that 10 ft. from
the power supply, additional lengths of properly
sized electrical cable will be required.
Never use a smaller gauge size than supplied
by the factory!
b.
Depending on the electrical setup, it may be
necessary to install an appropriate plug on the end
of the cable. GlasCraft will not supply this plug, as
we are unaware of which style will be needed.
c.
Consult the data sheet for the specific unit being
installed to determine the proper breaker size
needed.
d.
You will need to run an air line to the area where
the machine will be placed. consult the data
sheet the specific unit being installed to determine
much clean, dry air will be needed to supply the
machine. If the air line is
under
25 ft. use a
minimum of 1/2 in. I.D. pipe or hose. If the air line
is
longer
than 25 ft., use a minimum of 3/4 in.
pipe or hose. Anything smaller than these
diameters will severly affect the machine’s
performance!
Do not use any quick disconnect fittings on
the main air line going to the machine!
Check your air-compressor to make sure it is
capable of supplying the maximum amount of air
that the machine requires. All GlasCraft equipment
is rated at 25 CFM (cubic foot per minute) 708
liters at 90- 100 psi (.62-0.7 MPa, 6.3-7.7 bar)
do not exceed 125 psi (0.86 MPa, 8.6 bar).
3.
Move material drums to the area that the equipment will
be placed, ensuring that they are not sitting directly on
the floor. Simply place the drums on top of a palate or
similar device, so the drum bottoms will not be in
contact with any cold surfaces.
4.
Open all boxes that came with the machine and verify
that all items are accounted for.
8
Summary of Contents for GC1741
Page 26: ...24 Section 3 General Information Assembly Drawings GC1751 Generic System Schematic ...
Page 27: ...GC1751 System Schematic 220V Single Phase 25 Section 3 General Information Assembly Drawings ...
Page 37: ...Section 4 Safety Information Notes 35 ...