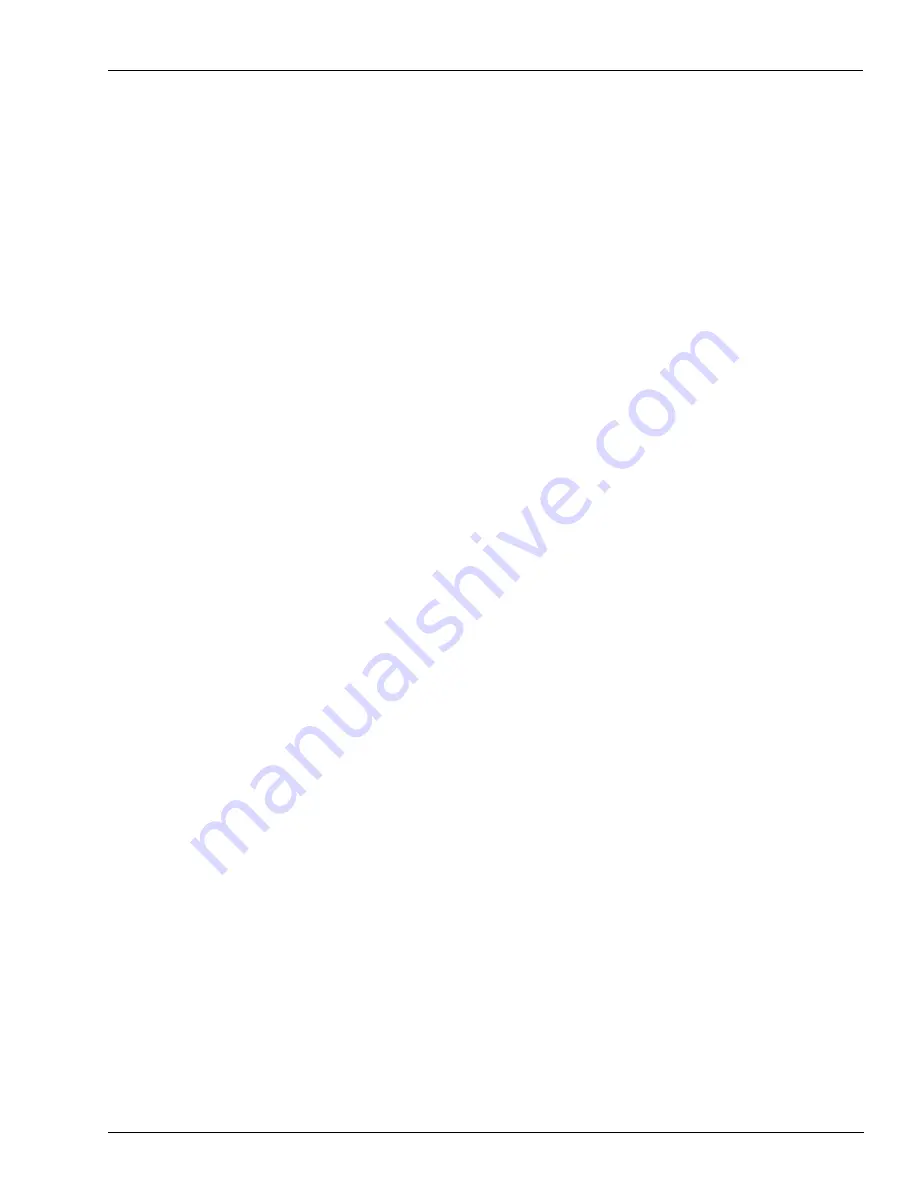
Page 6-13
System Conditions That Can Be Ignored
Troubleshooting and Analysis
MDE-5394B VaporTEK™/VaporTEK-3 Controller Board 110 V UL® Vapor Recovery Collection System for Encore® 500 S
Start-Up and Service Manual · March 2019
System Conditions That Require Attention
Long-term System Wear
Minor (and probably random) variations in pump performance will cause the A/L Ratio to
vary about its target of 100%, possibly causing it to go out of its allowable range occasionally.
These are not a cause for system shutdown and do not pose any concern to service personnel,
as they should not persist for ten consecutive transactions.
However, after a significant period of time (on the order of years), the system will eventually
go out of calibration. That is, the relationship between pump speed and flow will change, the
vapor flow will deviate from the fuel flow, and the A/L Ratio will deviate from its target.
However, as opposed to short-term variations, which will likely cause the A/L Ratio to deviate
in both directions about its average (above and below), long-term system wear will most likely
cause the A/L Ratio to trend inexorably downward. While there still will be short-term
variability superimposed on this long-term trend, once the wear becomes significant enough,
the A/L Ratio will drop out of the allowable range altogether and not return.
The remedy for this condition is simple, as it is not uncommon for this situation to occur. The
pump was designed with flow capacity well in excess of the maximum fuel flow of the
dispenser. Therefore, when the operating point of the pump changes due to wear, recalibration
will bring the pump flow back to the acceptable level. That is, the pump will need to be run at
a higher speed to deliver the same flow that it previously delivered at a slower speed. The
calibration routine described in
“External Flow Meter Calibration”
pump to run faster than it had when it was previously calibrated, and the system will operate in
compliance for a significant period of time before it will again require calibration. At some
point in time, the maximum capacity of the pump will be reached, and calibrating will no
longer bring the vapor flow up to the same level as the fuel flow. At this point, the pump will
need to be replaced.
Air Leaks
The detection of air leaks differs depending on whether the leak is on the nozzle side vs. the
dispenser (effectively, outside vs. inside the dispenser).
Nozzle-side Leaks
If there is an air leak on the nozzle side (outside) of the dispenser, the system will generate no
error but simulation on a multi-dispenser with more than one gasoline products with vapor
flow will detect a nozzle leak. Connect the reference Burkert Meter to the discharge side of
pumping unit and make a simulation with 40 LPM. If the meter starts counting, then a leakage
on the vacuum side is detected.
The vapor pump is connected to both sides of the dispenser at the same time. During
operation, the pump draws vapor through the side of the dispenser that is flowing liquid, and
no vapor flows through the opposite side, provided the nozzle on that side is not also
dispensing as well. However, if there is a leak between the nozzle and the flow meter
(i.e., anywhere in the nozzle, hose, breakaway, swivel, etc.), air will enter the system when the
pump begins to draw a vacuum.