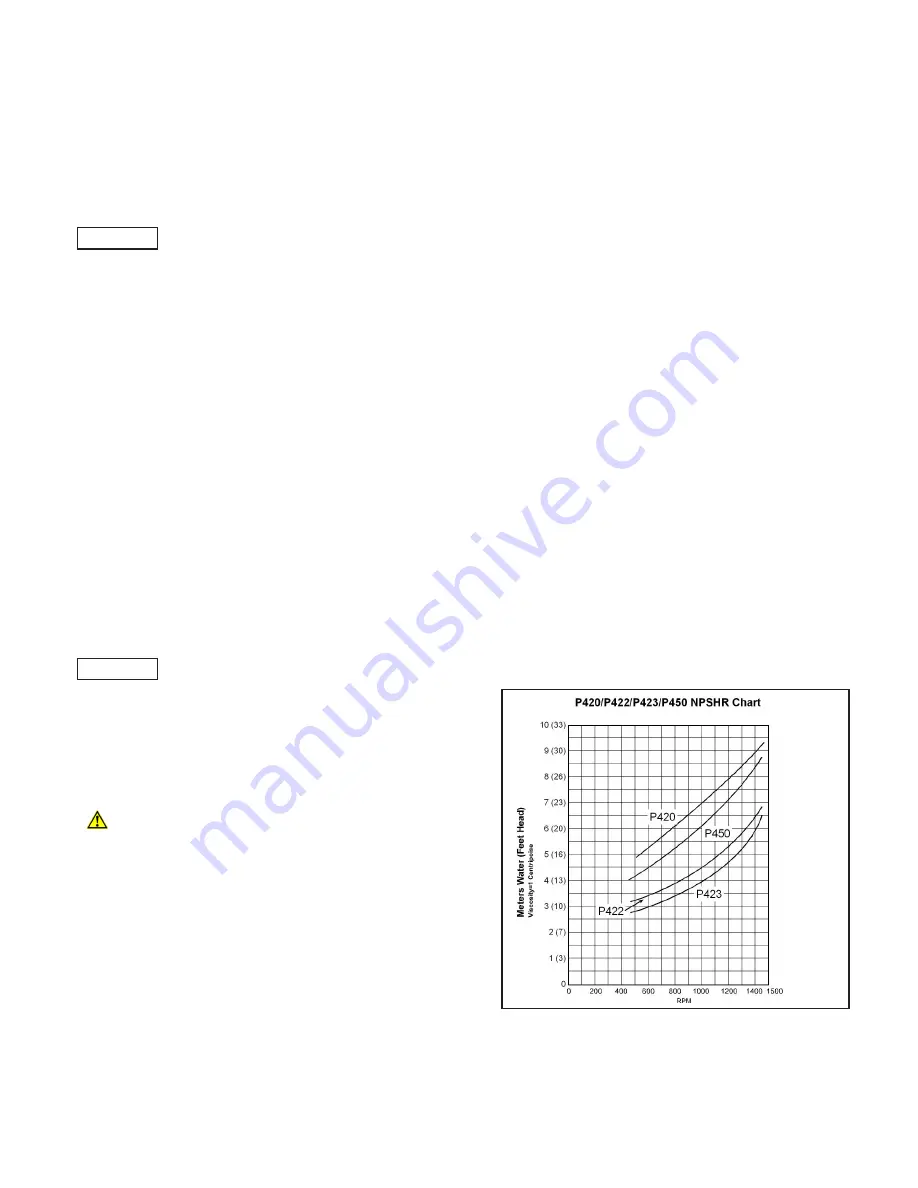
Pressure in the discharge line and pump must
be at zero before any maintenance to the pump
takes place. Shut off suction line. Disconnect
fuses to ensure that the driving motor does not
get switched on accidentally. Make sure that all
parts on the pressure side of the unit are vented
before starting the pump. In order to prevent air,
or an air-water mixture being absorbed and to
prevent cavitation occurring, the pump NPSHR
(=suction head) and water temperature must be
respected.
Cavitation and/or compression of gases lead
to uncontrollable pressure kicks which can
ruin pump and unit parts and also be dan-
gerous to the operator or anyone standing
nearby.
Giant Plunger Pumps are suitable for pumping
clean water and other non-agressive or non-
abrasive media with a specific weight similar to
water.
Before pumping other liquids - especially
inflammable, explosive and toxic media - the
pump manufacturer must be consulted with
regard to the resistance of the pump mate-
rial. It is the responsibility of the equipment
manufacturer and/or operator to ensure that
all pertinent safety regulations are ahered to.
2
INSTALLATION INSTRUCTIONS
Required NPSH refers to water (specific weight 1kg/
dm
3
) at maximum permissible pump revolutions.
Operation and Maintenance
Check oil level prior to starting to ensure trouble-free
water supply.
Important!
If there is a
danger of frost
, the water
in the pump and in the pump fittings (particularly the
unloader valve) must be emptied. The second dis-
charge port cal also be used and the pump run “dry”
for 1-2 minutes for this purpose.
Oil amount: 30.4 ounces (0.9 liters). Only use
ISO
VG 220 industrial gear oil
(e.g. Aral Degol BG220)
or
automobile gear oil SAE 90 GL4
(Giant p/n
01154).
Initial oil change after 50 operating hours and then
every 500 hours, after 1 year if used less. Caution
when operating in damp places or with high temper-
ature fluctuations. Oil must be changed immediately
should condensate (frothy oil) occur in the gear box.
NPSH values must be observed.
Maximum input pressure 145 PSI (10 bar), maxi-
mum suction head -4.35 PSI (-0.3 bar). Make sure
that suction pulsation is sufficiently dampened - wa-
ter column resonance must be avoided.
Important!
If the pump is not used for a long period
of time, it is possible the seals (23/23B) could be-
come hard or brittle thus causing the pump to leak
when put into operation.
If this is the case, we recommend these seals be
replaced every 4 years.
Safety Rules
A safety valve is to be installed in accordance with
the guidelines for liquid spraying units so that the
admissible operating pressure cannot be exceeded
by more than 10%. Pump operation without a safety
vlave as well as any excess in temperature or speed
limits automatically voids the warranty.
When the pump is in operation, the drive shaft end
and the coupling must be enclosed by a protective
cover or a coupling bell.