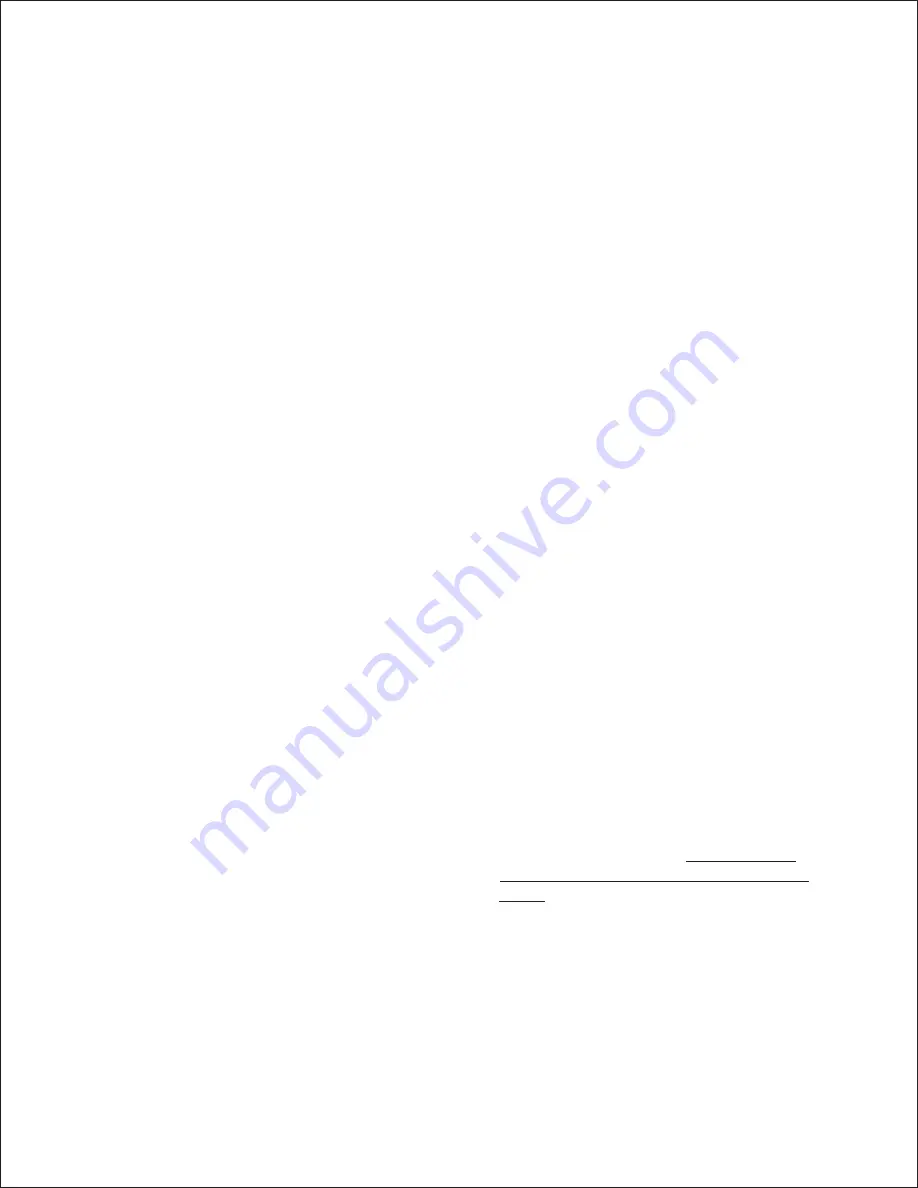
2
NOTE: Contact Giant Industries for Service School Information. Phone: (419)-531-4600
INSTALLATION INSTRUCTIONS
Installation of the Giant Industries, Inc.,
pump is not a complicated procedure, but
there are some basic steps common to all
pumps. The following information is to be
considered as a general outline for installa-
tion. If you have unique requirements, please
contact Giant Industries, Inc. or your local
distributor for assistance.
1. The pump should be installed flat on a base to
a maximum of a 15 degree angle of inclination
to ensure optimum lubrication.
2. The inlet to the pump should be sized for the
flow rate of the pump with no unnecessary
restrictions that can cause cavitation. Teflon
tape should be used to seal all joints. If pumps
are to be operated at temperatures in excess of
160
0
F, it is important to insure a positive head
to the pump to prevent cavitation. See NPSH
curve.
3. The discharge plumbing from the pump
should be properly sized to the flow rate to
prevent line pressure loss to the work area. It is
essential to provide a safety bypass valve
between the pump and the work area to protect
the pump from pressure spikes in the event of a
blockage or the use of a shut-off gun.
Finally, remember that high pressure operation in a pump system has many advantages. But, if it is used carelessly and
without regard to its potential hazard, it can cause serious injury.
IMPORTANT OPERATING CONDITIONS
Failure to comply with any of these conditions invalidates the warranty.
1. Prior to initial operation, add oil to the
crankcase so that oil level is between the two
lines on the oil dipstick. DO NOT OVERFILL.
Use Giant Recommended Oil
Crankcase oil should be changed after the
first 50 hours of operation, then at regular
intervals of 500 hours or less depending on
operating conditions.
4. Use of a dampener is necessary to minimize
pulsation at drive elements, plumbing, connec-
tions, and other system areas. The use of a
dampener with Giant Industries, Inc. pumps is
optional, although recommended by Giant
Industries, Inc. to further reduce system pulsa-
tion. Dampeners can also reduce the severity of
pressure spikes that occur in systems using a
shut-off gun. A dampener must be positioned
downstream from the unloader.
5. Crankshaft rotation on Giant Industries, Inc.
pumps should be made in the direction desig-
nated by the arrows on the pump crankcase.
Reverse rotation may be safely achieved by
following a few guidelines available upon
request from Giant Industries, Inc. Required
horsepower for system operation can be ob-
tained from the charts on pages 3.
6. Before beginning operation of your pumping
system, remember: Check that the crankcase
and seal areas have been properly lubricated per
recommended schedules. Do not run the pump
dry for extended periods of time. Cavitation will
result in severe damage. Always remember to
check that all plumbing valves are open and that
pumped media can flow freely to the inlet of the
pump.
2. Pump operation must not exceed rated
pressure, volume, or RPM. A pressure relief
device must be installed in the discharge of the
system.
3. Acids, alkalines, or abrasive fluids cannot be
pumped unless approval in writing is obtained
before operation from Giant Industries, Inc.
4. Run the pump dry approximately 10 seconds
to drain the water before exposure to freezing
temperatures.