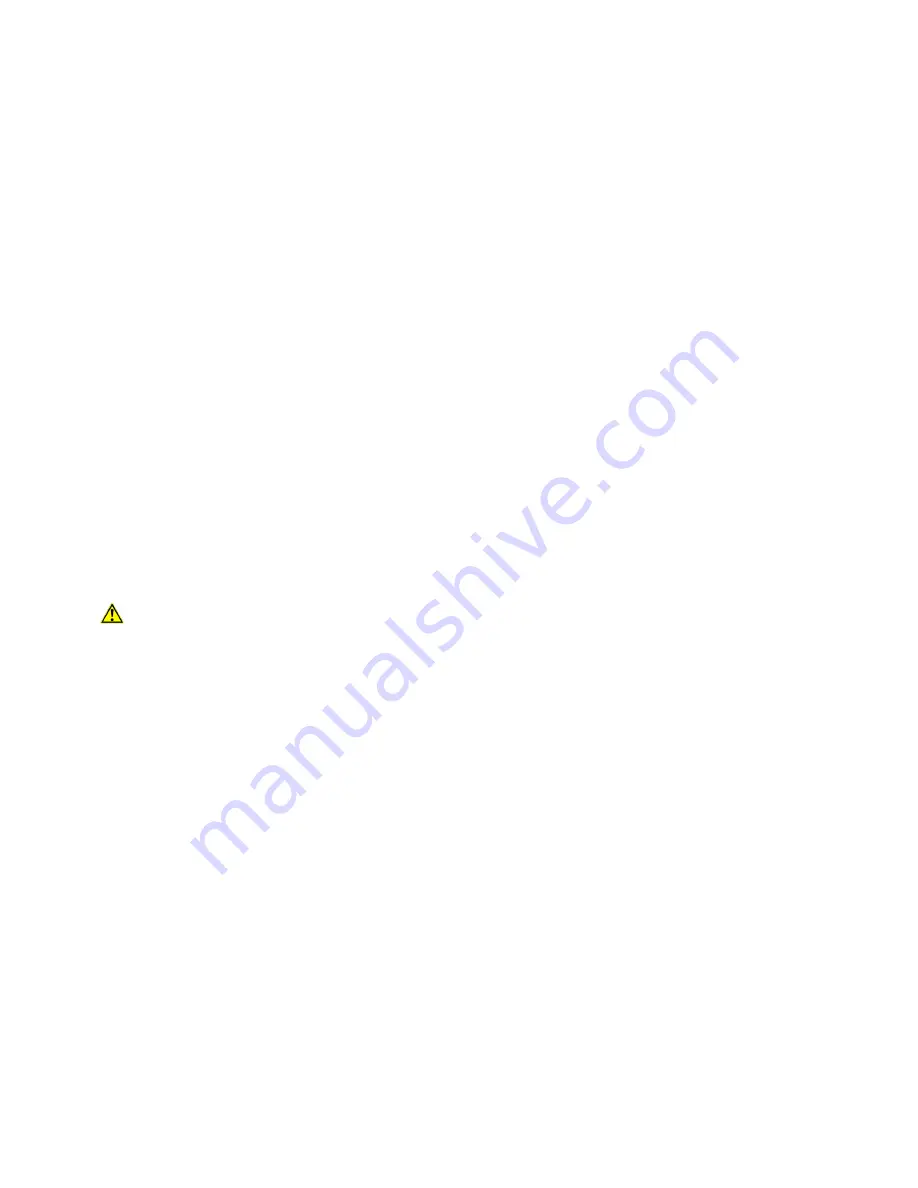
2
INSTALLATION INSTRUCTIONS
Figures for speed (rpm) and pressure apply to
interval operation with cold water.
For continual operation, the speed of all pump
models must be limited to 700 rpm and the
max. operating pressure reduced by 10%.
Required NPSH refers to water: Specific weight
1kg/dm
3
, viscosity 1°E at max. permissible revo-
lutions.
Operation and Maintenance
Check oil level prior to starting and ensure trou-
ble-free water supply. Oil: Use only 1.2 gallons
(4.6 liters) of Industrial Gear Lube Oil (Giant p/n
01154) or ISO VG 220 (e.g. Aral Degol BG220)
or SAE 90 gear oil.
Initial change after 50 operating hours and then
every 500 operating hours.
Caution when operating in damp places or
with high temperature fluctuations. Oil must
be changed immediately, should condensate
(frothy oil) occur in the gear box.
Keep NPSH under control.
Max. input pressure 145 PSI (10 bar), max. suc-
tion head -4.35 PSI (-0.3 bar).
Safety Rules
Pump operation without safety valve as well
as any excess in temperature or speed limits
automatically voids the warranty. The safety
valve must be regulated in accordance with
the guidelines for liquid spraying units so that
the admissible operating pressure can not be
exceeded by more than 10%.
When the pump is in operation, the open shaft
end must be covered up by a shaft protector
(21), the driven shaft side and coupling by a
contact-protector.
Pressure in discharge line and in pump must
be at zero before any maintenance to the pump
takes place. Close up suction line. Disconnect
fuses to ensure that the driving motor does not
get switched on accidently.
Make sure that all parts on the pressure side of
the unit are vented and refilled, with pressure at
zero, before starting the pump.
In order to prevent air, or an air/water-mixture
being absorbed and to prevent cavitation occur-
ing, te pump-npshr, positive suction head and
water temperature must be kept under control.
Cavitation and/or compression of gases lead
to uncontrollable pressure-kicks which can
ruin pump and unit parts and also be dan-
gerous to the operator or anyone standing
nearby.
Giant plunger pumps are suitable for pump-
ing clean water and other non-agressive or
abrasive media with a specific weight similar to
water.
Before pumping other liquids - especially
inflammable, explosive and toxic media - the
pump manufacturer must under all circum-
stances be consulted with regard to the
resistance of the pump material. It is the re-
sponsibility of the equipment manufacturer
and/or operator to ensure that all pertinent
safety regulations are adhered to.
Summary of Contents for GP5128
Page 4: ...4 GP5128 Exploded View...