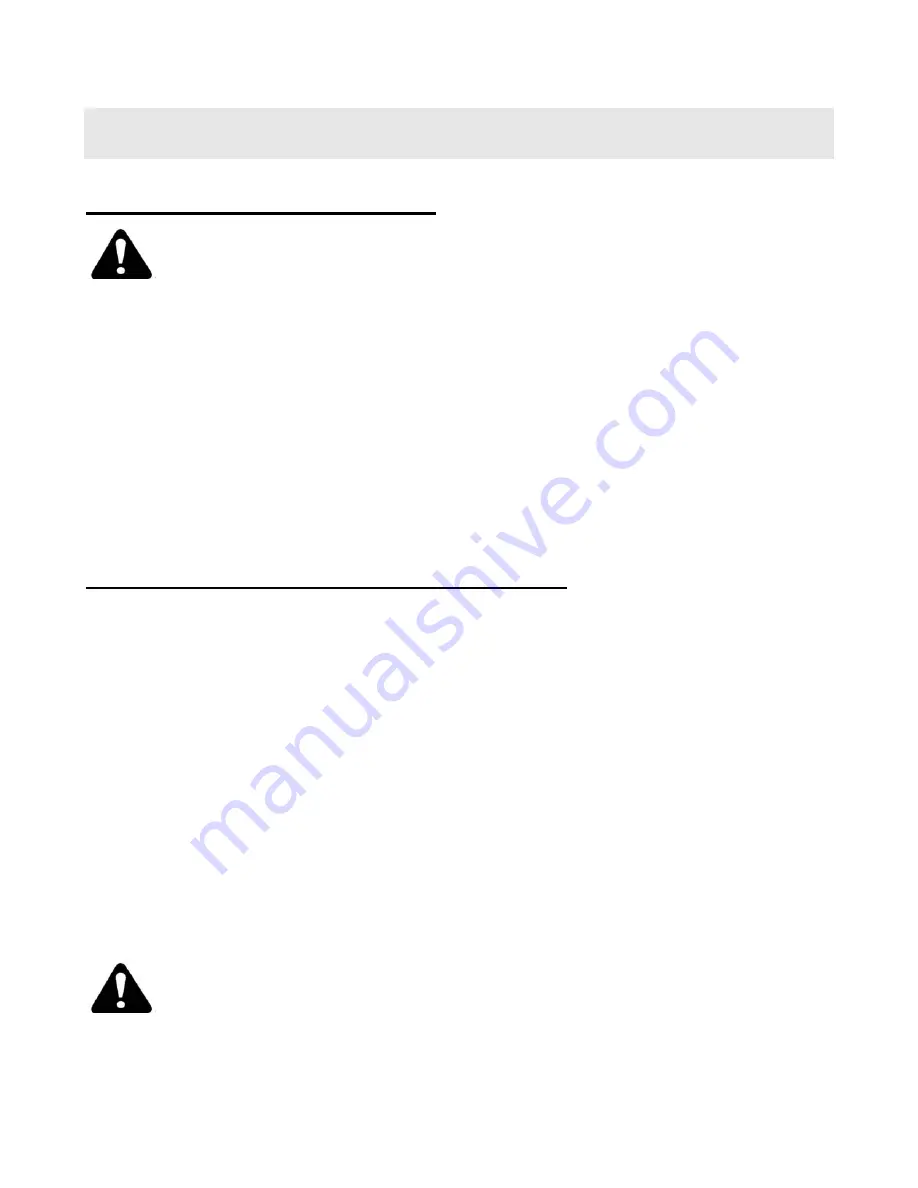
3
unit assembly & set-up (cont.)
DEBRIS BOX CONSTRUCTION
WARNING: This unit is designed to be used in conjunction with a debris collection
box. NEVER run or operate your Truck Loader without a debris box.
Below are directions for constructing a simple, sturdy debris box for use in a standard pickup
bed:
•
Cut four pieces of 3” angle iron to the inside length of the truck bed, four pieces to the inside width, then four
pieces that measure from the truck bed floor to approximately 8” higher than the top of the unit discharge
when the unit is connected to the truck. Either weld or securely bolt the box frame together.
•
Line the inside front and sides with 3/4” exterior grade plywood.
•
Cover the top of the frame with a heavy duty mesh screening to allow for adequate ventilation.
•
Cut a plywood door the width and height of the box frame. Install a heavy duty hinge at the top of the door
and fasten it to the rear of the box frame. Install latches or other locking mechanisms between the lower
sides of the door and the box sides to keep the door from opening inadvertently.
•
Mark the location on the door where the unit discharge meets the box, then cut a 16” diameter hole in the
door at that location. Install a rubber gasket around the hole to prevent debris blow-by – an old 13” or 14”
inner tube works fine.
CONNECTING UNIT TO TOWING VEHICLE
•
Install appropriate trailer plug onto end of unit wiring harness to match socket on towing vehicle. Wiring
scheme is as follows:
Red – Right signal
Yellow – Left signal
Brown – Taillights
Green – Ground
•
Back towing vehicle up to unit. Raise or lower support jack until ball hitch receiver on unit is about 3-4”
higher than ball hitch on vehicle. Flip lock lever up on ball hitch receiver.
•
With assistance behind, back up slowly, aligning both ball hitch receiver with ball hitch and discharge hose
with receiver box opening.
•
Lower front of unit down until ball hitch receiver drops completely onto ball hitch. Rock unit back and forth a
couple of times to ensure full coupling of ball hitch. Lock ball hitch receiver lever. Use a clevis pin or
padlock through locking hole in lever, to prevent accidental disconnect.
•
Connect safety chains to vehicle in a criss-cross fashion to cradle draw bar in case of accidental disconnect,
then connect wiring harness plug into trailer socket of vehicle.
•
Lift rear support leg and secure in uppermost position with clevis pin. Also be sure to fully raise support
jack.
Note: To prevent possible rollover, lock rear support leg in lowermost position
possible when unit is parked or disconnected from towing vehicle.
Your unit is now ready to be started and checked for proper operation. See your engine
manual for proper engine prep and operation.