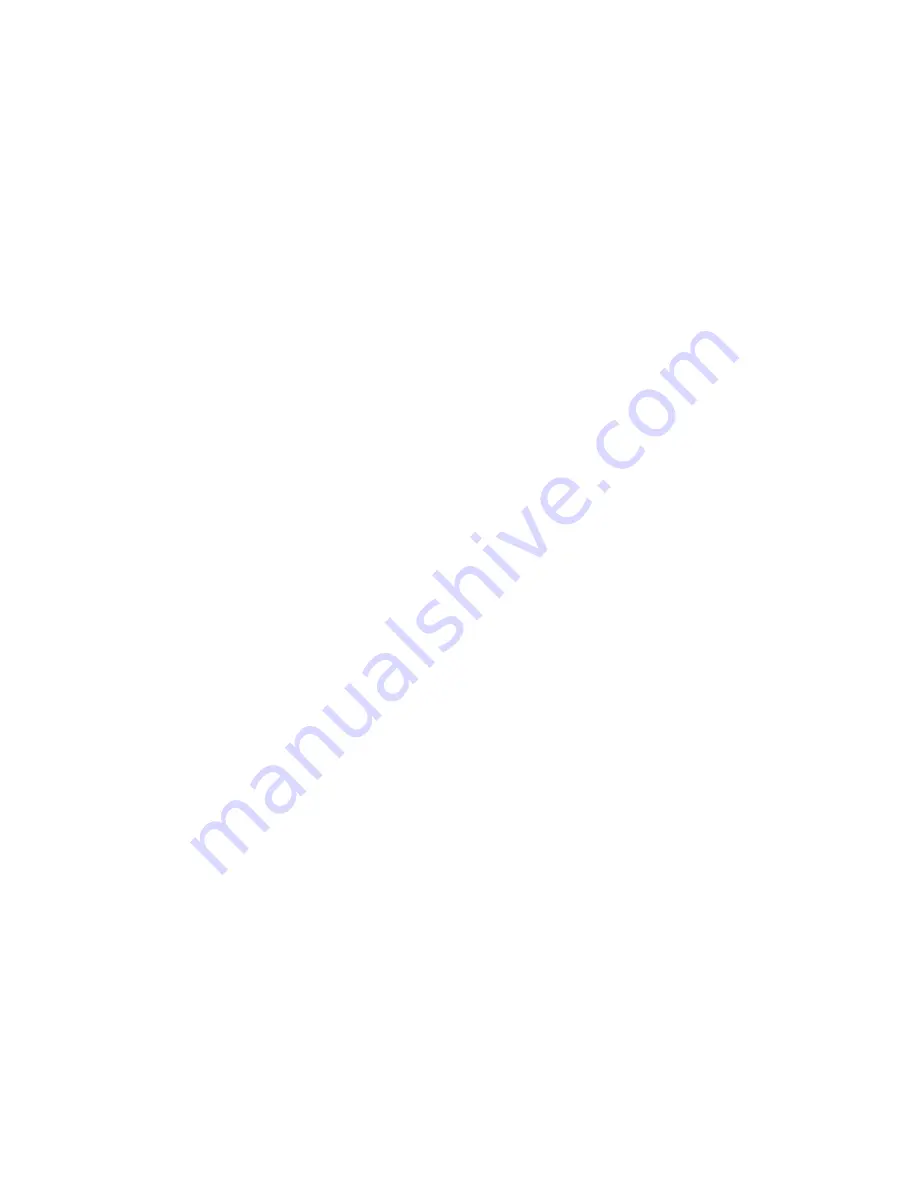
8
valve casing must be clean and free of damage. The components must lie exactly and
evenly on one another. The same exactness applies for all centering positions in the crank-
case, intermediate casing, pressure-and valve casing.
Coat the seal sleeve lightly with anticorrosive grease (e.g. molycote no. Cu-7439) in its fi t-
ted area towards the crankcase. Insert seal sleeves in to their crankcase fi ttings.
Important!
Watch the even milled surfaces on the seal sleeves. They must be positioned
vertically on each other.
Turn the pump (by hand) until the plunger (25) rests against the plunger (36). Tighten
plunger (36) to 33 Ft-lbs. (45 NM).
Insert the seal tension spring (45) in to the seal sleeve (39).
Mounting Valve Casing:
Press seal cases (38) (with the stepped OD diameter 65mm) carefully to its stop in the
centering holes of the intermediate casing. Mount fl at leakage seal (62D).
Important!
The fl at leakage seal (62D) must be positioned with its 3mm diameter bore onto
the notched pin (62C) on the intermediate casing. The leakage return bores in the interme-
diate casing and in the seal sleeves must remain clear of the cutouts in the seal (62D).
Push valve casing (50) together with intermediate casing (62) carefully on to the centering
studs (50A).
Tighten hexagon nuts evenly and crosswise to 265 Ft-lbs. (360 NM).
Important!
The torque tension on the screws (49A) must be checked after 8-10 operating
hours; the pump must be at zero pressure. Thereafter the tension is to be checked every
200 operating hours.
Repair Instructions - GP8035 Pump