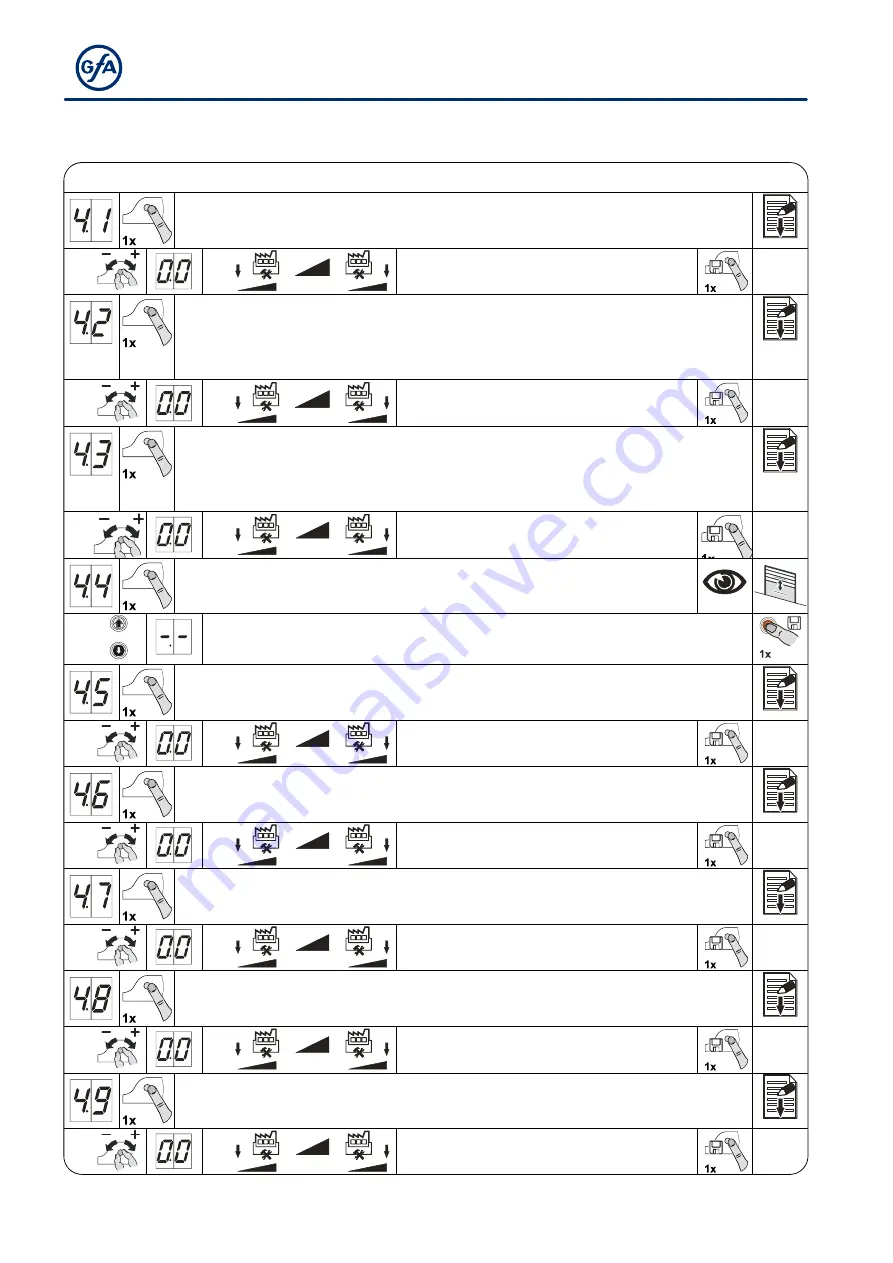
32
DI/FI settings
DI/FI settings
OPEN output speed
Output speed in rpm
CLOSE output speed
When a safety device is triggered, the door moves at reduced speed.
Output speed in rpm
Increased CLOSE output speed
Up to an opening height of 2.5 m
When a safety device is triggered, the door moves at reduced speed.
Output speed in rpm
0 = Off
Changeover position to CLOSE output speed
(with adherence to minimum opening height requirement of 2.5 m!)
Approach and store desired door position
OPEN acceleration
DI
Steps of 1.0 seconds
FI
Steps of 0.1 seconds
CLOSE acceleration
DI
Steps of 1.0 seconds
FI
Steps of 0.1 seconds
OPEN deceleration
DI
Steps of 1.0 seconds
FI
Steps of 0.1 seconds
CLOSE deceleration
DI
Steps of 1.0 seconds
FI
Steps of 0.1 seconds
OPEN/CLOSE crawling speed
Output speed in rpm