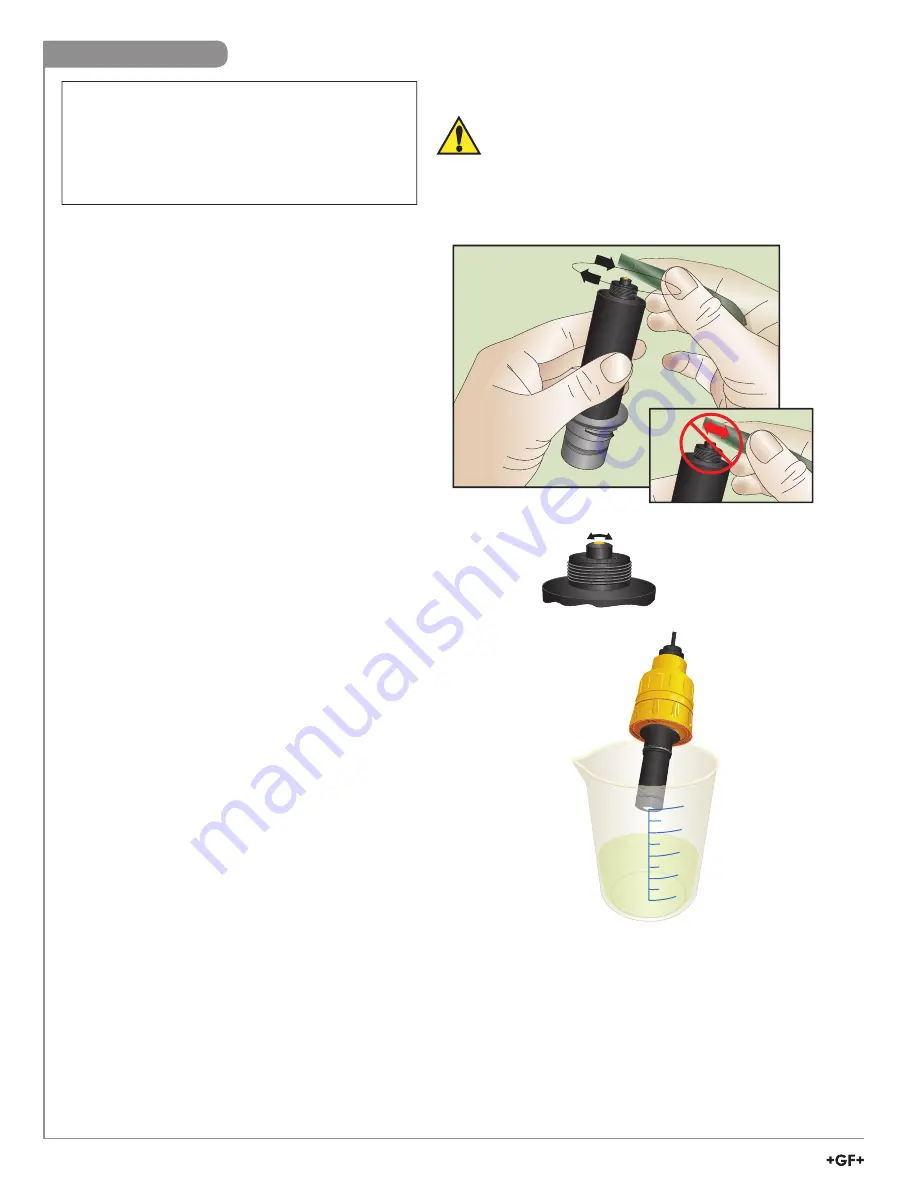
8
GF 263X Series Chlorine Electrodes
Reconditioning
Required to recondition a sensor:
• DI Water
• Beaker (any size available)
• Polishing Sheets (Included in sensor maintenance kit)
• Free Chlorine: Chlorine Bleach (13% concentration)
• Chlorine Dioxide: Aqueous Chlorine Dioxide solution
Reconditioning Procedure (Steps 1-10):
1. Remove the sensor from the 2650 electronics.
2. Remove the membrane cap.
3. Place the sensor on a
fi
rm,
fl
at surface with gold
cathode pointing upward.
4. Apply a small amount of water to the blue (coarse)
polishing paper (dull side).
5. Polish the gold electrode by moving the paper in a
circular pattern for 30 seconds. DO NOT go back and
forth in a single direction. See Figure 1.
6. Rinse the sensor tip with DI water.
7. Apply a small amount of DI water to the white (
fi
ne)
polishing paper (dull side) and polish the gold
electrode by moving the paper in a circular pattern for
30 seconds. DO NOT go back and forth in a single
direction. See Figure 1.
8. Rinse the sensor tip with DI water.
9. Top off the sensor with electrolyte and inspect
membrane for dirt or damage. Replace if necessary.
10. Insert the sensor into the 2650-7 electronics and
apply power.
Reconditioning Procedure (Steps 11-17):
11. Fill beaker with a 12 mm (½ inch) of the appropriate
solution.
12. Position or suspend the sensor 6 mm to 12 mm
(¼ in. to ½ in.) above the appropriate solution. DO
NOT SUBMERGE THE SENSOR. See Figure 2.
13. Apply power to the system.
14. Monitor the nA of the sensor (press the down arrow
three times on the 9950-3 Chlorine Controller).
The nA reading should start to rise. Response time
and nA reading will depend upon the temperature of
the bleach.
15. Once the sensor's nA reading reaches approximately
300-360 nA, allow the sensor to remain in the beaker,
suspended over the appropriate solution, for an
additional 20 minutes.
• If sensor does not recover, cover the
beaker to avoid air contamination.
• Contact the factory for assistance
(www.gfsignet.com)
16. After 20 minutes, remove the sensor from the beaker
and install it into the
fl
ow cell and restore
fl
ow to the
system.
17. Calibrate the sensor after the system has become
stable.
CAUTION!
Bleach and Chlorine Dioxide solutions are very corrosive and
may release dangerous gases if they come in contact with
acids.
• Wear proper protective clothing (gloves and eye protection)
• Avoid contact with skin and eyes
• Observe all warnings on safety data sheets
• Avoid spilling bleach and possible contact with acids
Curved Surface
Figure 1
Figure 2
The electrode is not recyclable. Dispose of properly according to local, state and federal guidelines.