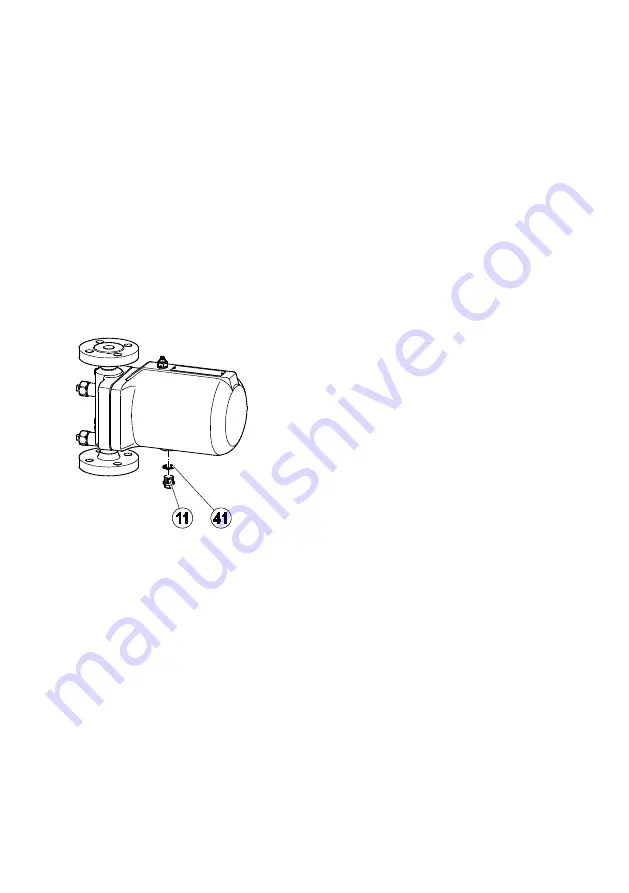
18
Make sure that medium exiting the system is
caught.
Open the screw plug (11) at the bottom of the
body.
Wait until the equipment has drained fully.
Clean the sealing surfaces of the screw plug
and cover.
Insert a new gasket (41) in the hole in the cover.
The necessary torque for tightening the screw plug
varies depending on type.
To close the screw plug of the UNA 39, tighten
it to a torque of 170 Nm.
To close the screw plug of the UNA 38, tighten
it to a torque of 70 Nm.
Removing external dirt deposits
To remove dirt deposits rinse the equipment
with fresh water and wipe it with a clean, lint-
free cloth.
To remove any persistent residues use a
cleaning agent that is suitable for the material
and carefully wipe the equipment with a clean,
lint-free cloth.
Maintaining the equipment
You require the following tools for working on the
equipment:
Type B combination spanner to DIN 3113, in
sizes
10
11
16 (UNA 39 only)
17
18 (UNA 39 only)
27
30
32
36
46)
Torque wrench to DIN ISO 6789
10–60 Nm
60–120 Nm
120–300 Nm
Allen key to DIN ISO 2936 in sizes
4
6
8
Summary of Contents for UNA 38
Page 1: ...Ball float steam trap UNA 38 UNA 39 Original Installation Instructions 818603 03 ...
Page 38: ...38 Dimensions and weights for UNA 39 ...
Page 46: ...46 ...
Page 47: ...47 ...