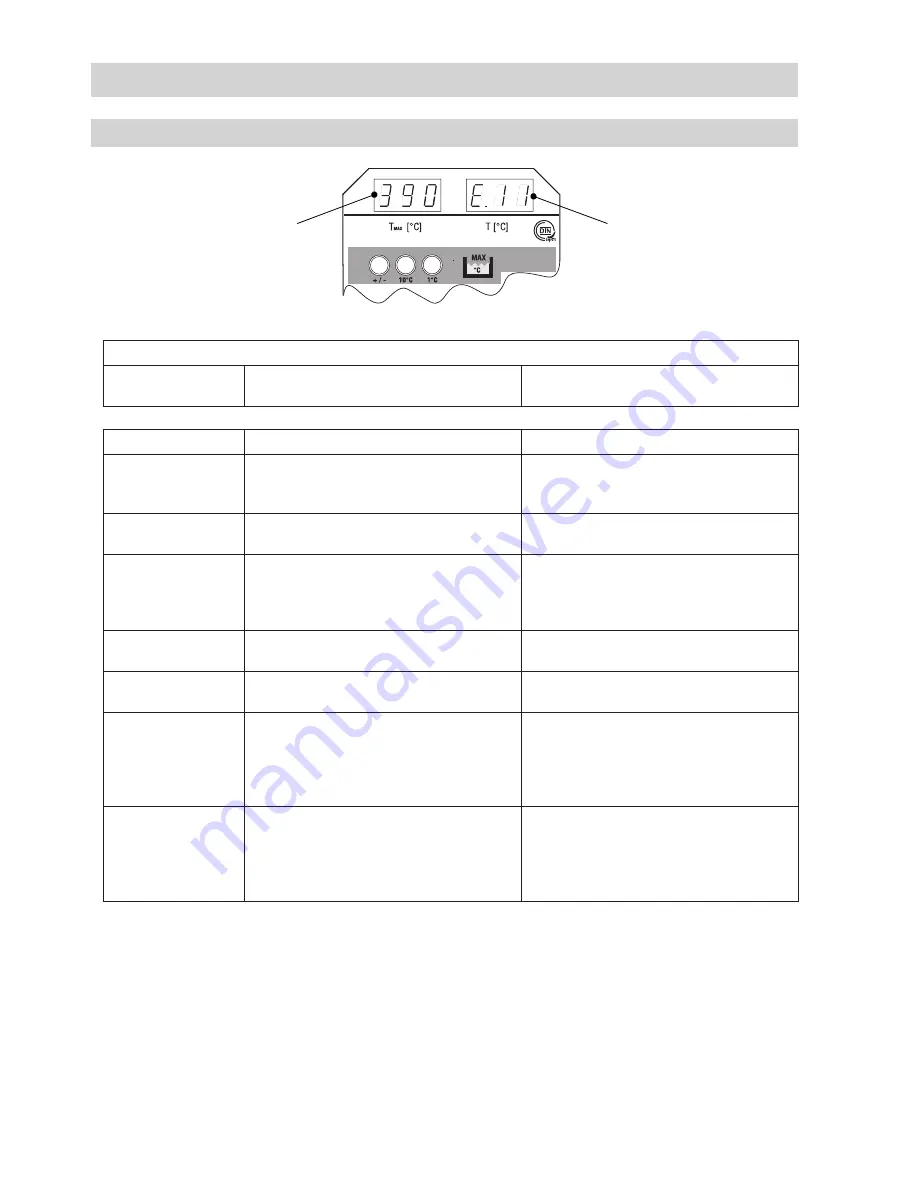
20
Indication of error code
When an error
occurs
Indication T
Display switches between indication of
error code
(E xx)
and actual value T
Error code
Possible cause
Remedy
E.01 ... E.32
Temperature transmitter defective because
a malfunction was detected during one or
more self-testing routines.
Replace temperature transmitter.
E.11
Temperature in transmitter housing too high. Check installation of the temperature
transmitter.
E.12
Resistance in temperature sensor too high.
Check readings of the temperature sensor
(see table “Basic values of measuring
resistors”). Replace measuring element if
the measured values are incorrect.
E.17
Incorrect code switch
G
Fig. 3
(Configuration) setting.
Check and correct position of code switches
S 9 and S 10 (polynom).
E.18
Incorrect code switch
G
Fig. 3
(Configuration) setting.
Check and correct position of code switches
S 1 to S 8 (limiter number).
E.30
Sensor line interrupted or interruption in
temperature sensor.
Check sensor line and readings of the
temperature sensor (see table “Basic values
of measuring resistors”). If the measured
values are incorrect replace the measuring
element.
E.0b *)
Short circuit in temperature sensor.
Check sensor line and readings of the
temperature sensor (see table “Basic values
of measuring resistor”). If the measured
values are incorrect replace the measuring
element.
*) Do not confuse indication
b
and
6
!
System Malfunctions
– continued –
Table listing error codes
Fig. 7
Indication of
limit value
Indication of
actual value / error code