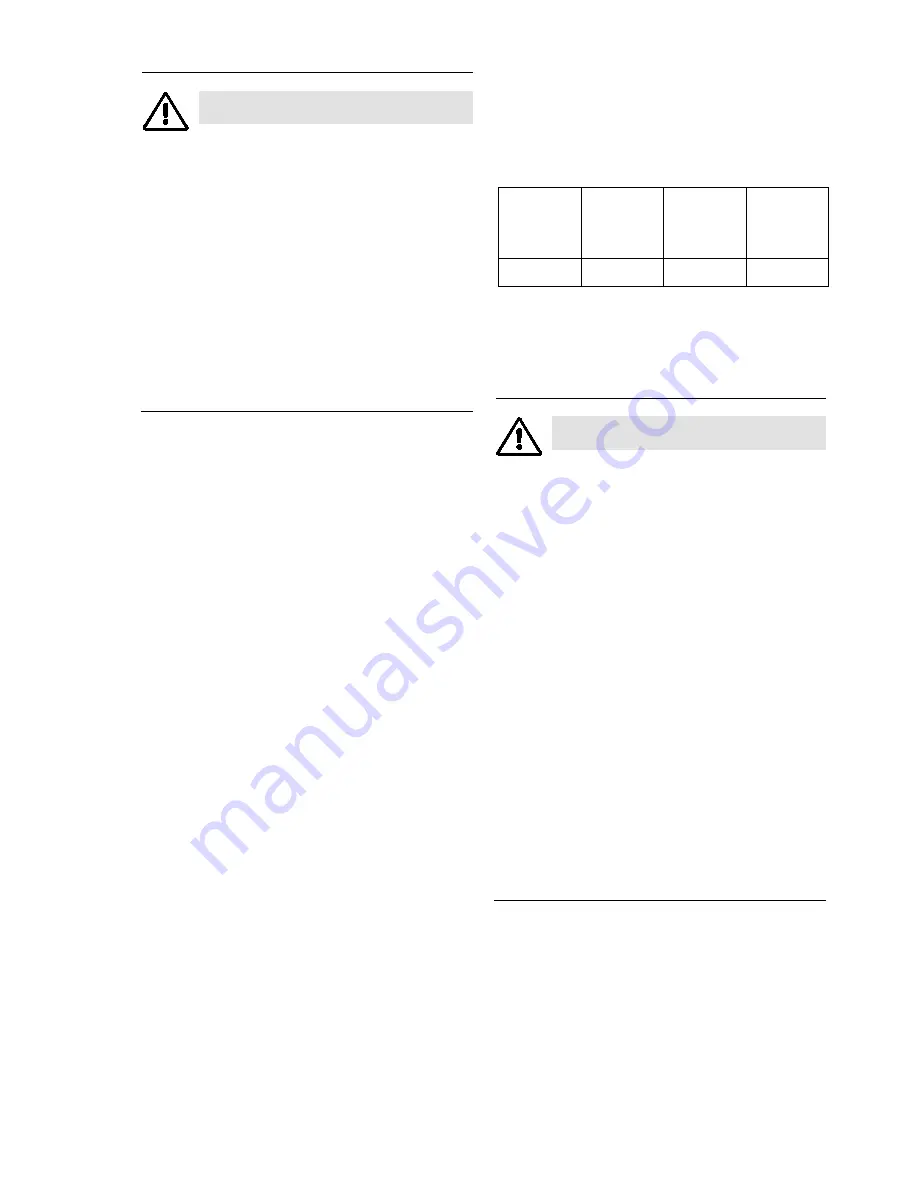
21
DANGER
Burns or intoxication from escaping
medium may cause extremely severe or
even fatal injuries.
Only insert new sight glasses in
perfect condition.
Clean all VAPOSCOPE components
before installation.
Remove foreign objects.
Tighten the hex nuts in the sight glass
lid evenly to the specified torque.
Check all removed parts for signs of damage.
Replace all worn or damaged parts.
Clean all dirty parts.
Coat the thread and contact surfaces with
temperature-resistant lubricant.
The lubricant must have the same properties as
OKS 217.
Insert the new inner sight glass seal.
Insert the new mica disc.
Insert the new sight glass.
Insert the new outer sight glass seal.
In type GK 21, insert the spherical washer in the
upper sight lass.
Insert the sight glass lid in the body.
The necessary torque for tightening the hex nuts
varies depending on type.
Please refer to the following table for the correct
torque.
GK 21
DN50
GK 11
DN65,
DN80
GK 11
DN100
GK 11
DN150
25 Nm
30 Nm
90 Nm
90 Nm
Tighten the hex nuts to the specified torque.
Secure the second sight glass in the same way.
Removing the lid
DANGER
Personnel working on pipes are exposed to
safety risks and may suffer severe injuries,
poisoning or even loss of life.
Make sure that no hot or hazardous
fluid is in the equipment or the pipes.
Make sure that the pipes upstream
and downstream of the equipment are
depressurised.
Make sure that the installation is
switched off and protected against
unauthorised or unintended activation.
Make sure that the equipment and the
pipes have cooled down to room
temperatures.
Wear protective clothing that is
suitable for the fluid and, if necessary,
wear protective gear.
For more information on suitable protective clothing
and safety gear refer to the safety data sheet of the
fluid in question.
You require the following tools to remove and fit the
lid:
Combination wrench to DIN 3113, type B (size
17, 18, 19, 24 or 30, depending on equipment
type)
Torque wrench to DIN ISO 6789