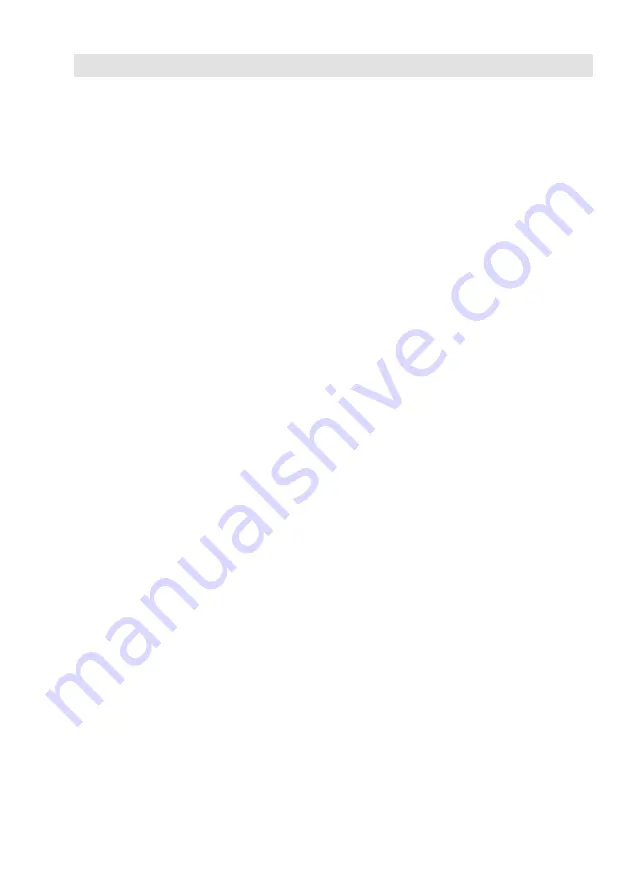
49
Manufacturer's declaration
For more information on the Conformity
Assessment according to European rules refer to
our Declaration of Conformity or our Declaration by
Manufacturer.
To download the current Declaration of Conformity
or Declaration by Manufacturer go to
www.gestra.com/documents or contact:
GESTRA AG
Münchener Straße 77
28215 Bremen
Germany
Telefon
+49 421 3503-0
Telefax
+49 421 3503-393
Web
www.gestra.de
This declaration is no longer valid if modifications
are made to the equipment without consultation
with us.
Summary of Contents for BB 1
Page 1: ...Double Swing Check Valve BB 1 BB 2 BB 3 Original Installation Instructions 819649 00 ...
Page 50: ...50 ...
Page 51: ...51 ...