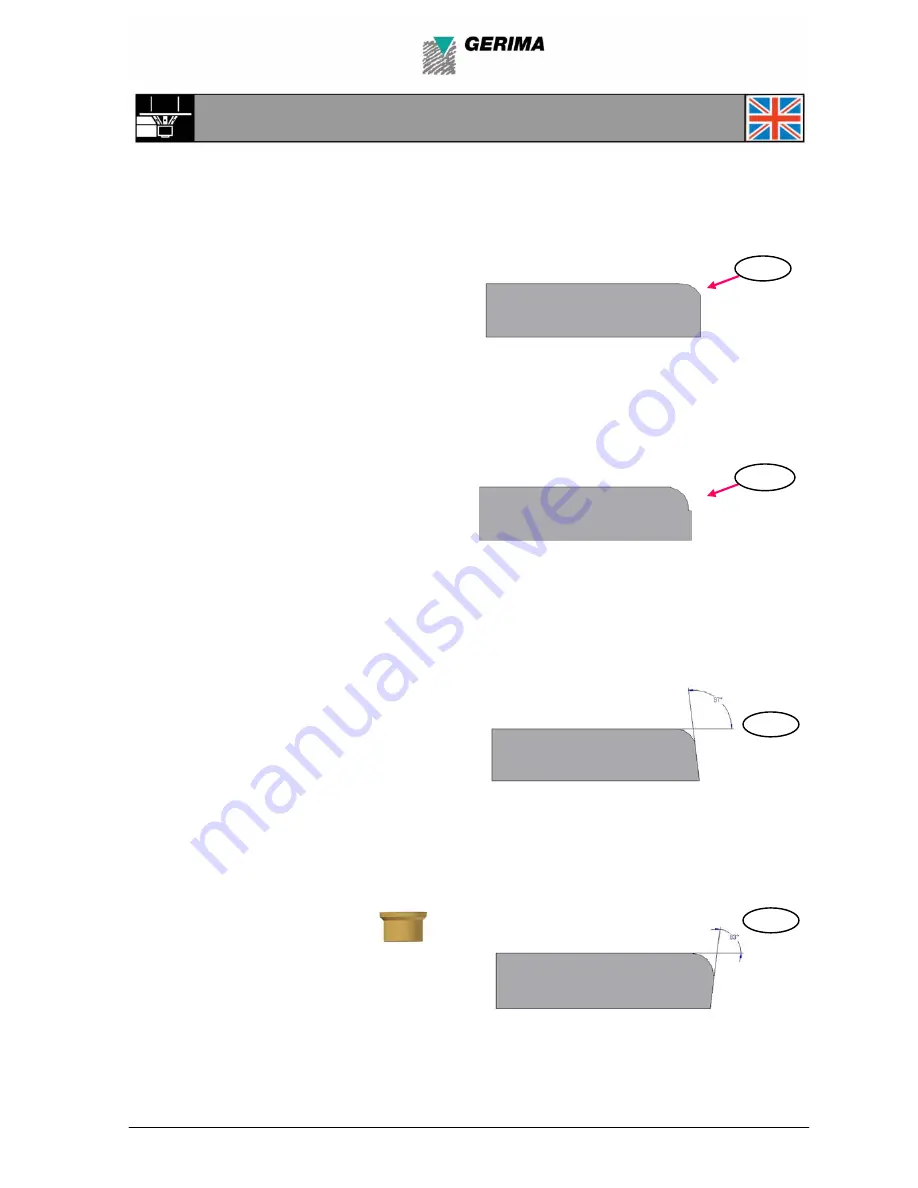
20
V62.1.2
.
27.09.10.ENG
>
90°
Notes
on
radius
milling:
Choosing
the
right
guide
bearing
to
ensure
the
correct
lateral
position
of
the
radius
is
just
as
important
as
setting
the
correct
height
of
the
guide
plate.
If
the
wrong
guide
bearing
is
used,
the
machined
radius
will
not
form
a
smooth
transition
with
the
end
face
of
the
workpiece.
If
the
guide
bearing
used
is
too
large,
the
ap
‐
pearance
of
the
resulting
radius
is
similar
(but
rotated
by
90°)
to
that
created
when
the
guide
plate
is
set
too
low.
If
the
guide
bearing
used
is
too
small,
the
ap
‐
pearance
of
the
resulting
radius
is
similar
(but
rotated
by
90°)
to
that
created
when
the
guide
plate
is
set
too
high.
The
same
phenomenon
arises
if
the
end
and
up
‐
per
faces
of
the
workpiece
are
not
aligned
at
right
angles
to
one
another.
If
the
edge
of
the
workpiece
to
be
machined
was
created
by
cutting
a
larger
plate
with
a
plasma
cutter,
the
upper
and
end
faces
of
the
workpiece
may
be
out
of
rectangular
alignment
by
as
much
as
7°.
This
type
of
misalignment
will
result
in
a
radius
that
is
either
incomplete
or
that
cuts
too
far
into
the
material
depending
on
whether
the
upper
or
lower
surface
of
the
workpiece
is
being
machined.
Although
our
conically
shaped
guide
bearings
are
designed
to
butt
up
against
the
workpiece
immediately
below
the
cutting
inserts
and
can
therefore
minimize
the
problem,
they
cannot
eradicate
it
entirely.
Machining
a
correct
radius
therefore
requires
a
90°
angle
between
the
adjacent
faces
of
the
workpiece.
Guide
bearing
too
large
(radius
incomplete)
Guide
bearing
too
small
(radius
cuts
into
material)
Angle
greater
than
90°
(radius
incomplete)
Angle
less
than
90°
(radius
cuts
into
material)
Indexable
cutting
inserts
for
radius
milling
<
90°
too
small
too
large