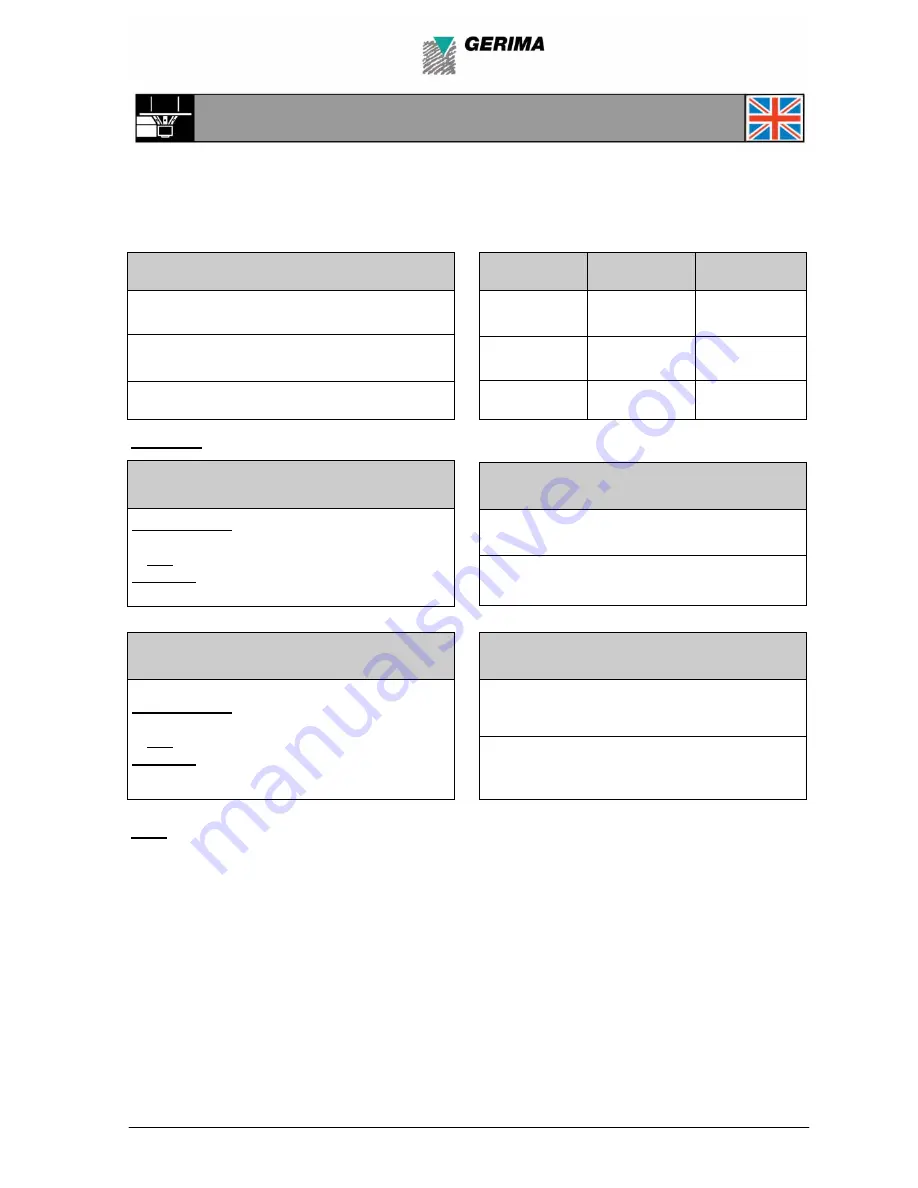
10
V62.1.2
.
27.09.10.ENG
Noise
emission
values
in
accordance
with
the
DIN
EN
60745
‐
1
standard
Vibrations:
Note:
The
measured
values
listed
above
depend
on
the
materials
and
operating
procedures
used
and
may
therefore
be
exceeded
under
other
operating
conditions.
Using
the
machine
to
create
bevels
with
a
width
greater
than
that
permitted
will
result
in
a
dispro
‐
portionally
large
reduction
in
the
machine’s
on
‐
time
and
the
service
life
of
the
indexable
cutting
inserts.
The
vibration
and
noise
emission
values
will
increase
accordingly.
Noise
emissions
Vibrations
Noise
emission
Emission
sound
pressure
level
(in
idle
mode,
speed
set
‐
Peak
emission
sound
pressure
level
at
workplace
(during
milling
operations)
Sound
power
level
Total
vibration
value
(tri
‐
axial
vector
sum)
Work
process:
‐
30°
milling
head
‐
(45°
milling
head
for
Radius)
‐
2
mm
bevel
width
(C)
in
12
mm
steel
sheet
(S
355)
Radius
R
2
Radius
in
12
mm
steel
sheet
S
355
‐
pressure
6
to
7
bar
Total
vibration
value
(tri
‐
axial
vector
sum)
Work
process:
‐
45°
milling
head
‐
‐
3
mm
bevel
width
(C)
in
12
mm
steel
sheet
(S
355)
Radius
R
3
Radius
in
12
mm
steel
sheet
S
355
‐
pressure
6
to
7
bar
Value
Uncertainty
L
pA
in
dB(A)
83
3
L
pGpeak
101
3
L
WA
in
dB(A)
94
3
Measured
vibration
emission
value
ah
=
2,50
m/s²
Uncertainty
K
=
1.5
m/s²
Determined
as
per
EN
60745:
The
power
‐
on
periods
listed
on
page
11
have
taken
the
vibration
values
into
account.
To
prevent
overloading
the
machine
and
to
avoid
operator
fatigue
it
is
very
important
to
observe
the
maximum
power
‐
on
periods
especially
when
machining
wide
bevels
or
high
‐
strength
materials.
Measured
vibration
emission
value
ah
=
3,0
m/s²
Uncertainty
K
=
1.5
m/s²
Determined
as
per
EN
60745: