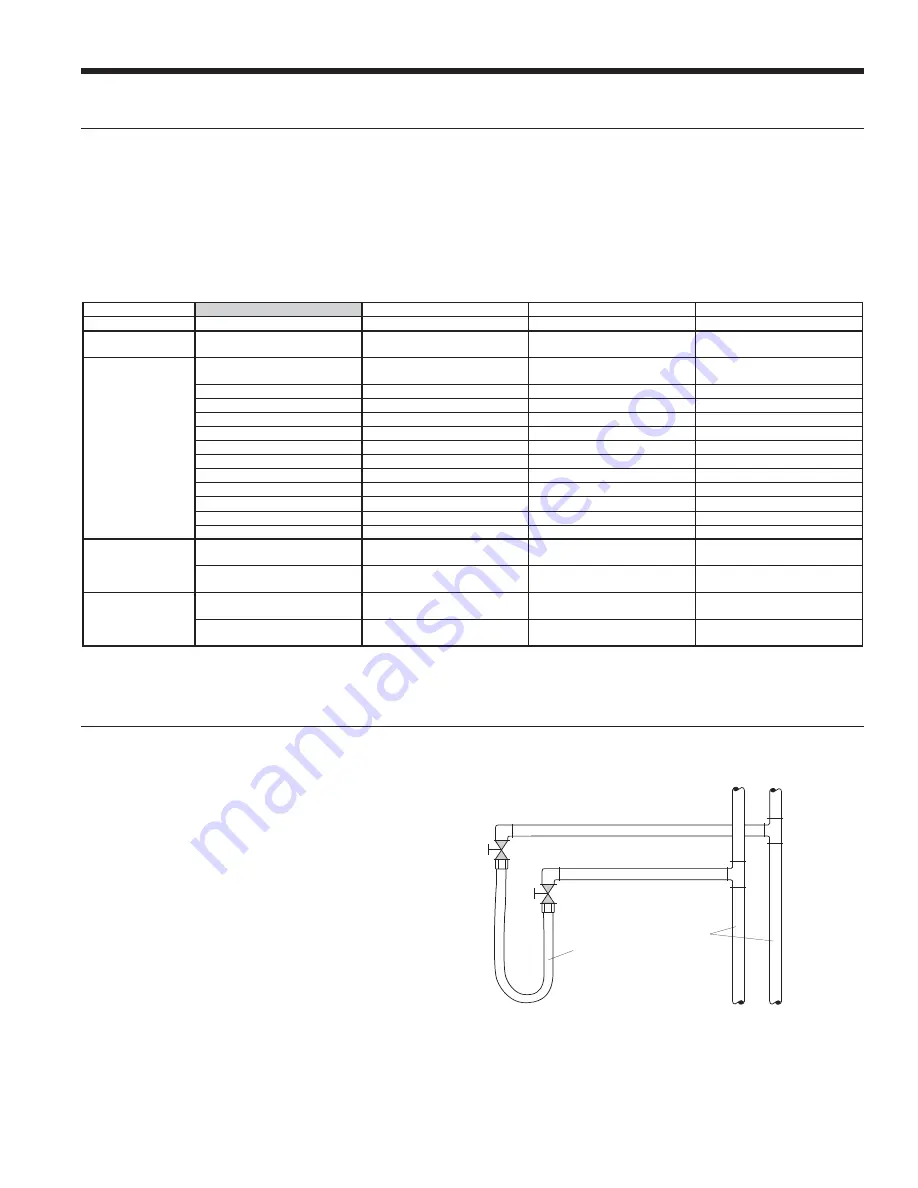
13
In ground water situations where scaling could be heavy or where
biological growth such as iron bacteria will be present, a closed
loop system is recommended. The heat exchanger coils in ground
water systems may, over a period of time, lose heat exchange
capabilities due to a buildup of mineral deposits inside. These
can be cleaned, but only by a qualified service mechanic, as
special solutions and pumping equipment are required. Hot water
generator coils can likewise become scaled and possibly plugged.
Water Quality
Material
Copper
90/10 Cupronickel
316 Stainless Steel
pH
Acidity/Alkalinity
7 - 9
7 - 9
7 - 9
Scaling
Calcium and
Magnesium Carbonate
(Total Hardness)
less than 350 ppm
(Total Hardness)
less than 350 ppm
(Total Hardness)
less than 350 ppm
Corrosion
Hydrogen Sulfide
Less than 0.5 ppm (rotten egg
smell appears at 0.5 ppm)
10 - 50 ppm
Less than 1 ppm
Sulfates
Less than 125 ppm
Less than 125 ppm
Less than 200 ppm
Chlorine
Less than 0.5 ppm
Less than 0.5 ppm
Less than 0.5 ppm
Chlorides
Less than 20 ppm
Less than 125 ppm
Less than 300 ppm
Carbon Dioxide
Less than 50 ppm
10 - 50 ppm
10 - 50 ppm
Ammonia
Less than 2 ppm
Less than 2 ppm
Less than 20 ppm
Ammonia Chloride
Less than 0.5 ppm
Less than 0.5 ppm
Less than 0.5 ppm
Ammonia Nitrate
Less than 0.5 ppm
Less than 0.5 ppm
Less than 0.5 ppm
Ammonia Hydroxide
Less than 0.5 ppm
Less than 0.5 ppm
Less than 0.5 ppm
Ammonia Sulfate
Less than 0.5 ppm
Less than 0.5 ppm
Less than 0.5 ppm
Total Dissolved Solids (TDS)
Less than 1000 ppm
1000 - 1500 ppm
1000 - 1500 ppm
LSI Index
+0.5 to -0.5
+0.5 to -0.5
+0.5 to -0.5
Iron Fouling
(Biological Growth)
Iron, FE
2
+ (Ferrous)
Bacterial Iron Potential
< 0.2 ppm
< 0.2 ppm
< 0.2 ppm
Iron Oxide
Less than 1 ppm, above this level
deposition will occur
Less than 1 ppm, above this level
deposition will occur
Less than 1 ppm, above this level
deposition will occur
Erosion
Suspended Solids
Less than 10 ppm and filtered for
max. of 600 micron size
Less than 10 ppm and filtered for
max. of 600 micron size
Less than 10 ppm and filtered for
max. of 600 micron size
Threshold Velocity
(Fresh Water)
< 6 ft/sec
< 6 ft/sec
< 6 ft/sec
NOTES:
Grains = ppm divided by 17
mg/L is equivalent to ppm
2/22/12
In areas with extremely hard water, the owner should be informed
that the heat exchanger may require occasional flushing. Failure
to adhere to the guidelines in the water quality table could result in
loss of warranty.
Units with cupronickel heat exchangers are recommended for open
loop applications due to the increased resistance to build-up and
corrosion, along with reduced wear caused by acid cleaning.
System Cleaning and Flushing
Cleaning and Flushing
Prior to start up of any heat pump, the water circulating system
must be cleaned and flushed of all dirt and debris.
If the system is equipped with water shutoff valves, the supply and
return runouts must be connected together at each unit location
(This will prevent the introduction of dirt into the unit, see Flushing
with Water Shutoff Valve Equipped Systems illustration). The
system should be filled at the water make-up connection with all air
vents open. After filling, vents should be closed.
The contractor should start the main circulator with the pressure
reducing valve makeup open. Vents should be checked in
sequence to bleed off any trapped air and to verify circulation
through all components of the system.
As water circulates through the system, the contractor should
check and repair any leaks found in the piping system. Drain(s) at
the lowest point(s) in the system should be opened for initial flush
and blowdown, making sure water fill valves are set at the same
rate. Check the pressure gauge at the pump suction and manually
Return Runout
Supply Runout
Mains
Rubber Hose
Runouts Initially
Connected Together
Flushing with Water Shutoff Valve Equipped Systems
PREMIUM G COMPACT INSTALLATION MANUAL
Summary of Contents for Premium G
Page 2: ......
Page 46: ...46 Notes PREMIUM G COMPACT INSTALLATION MANUAL...