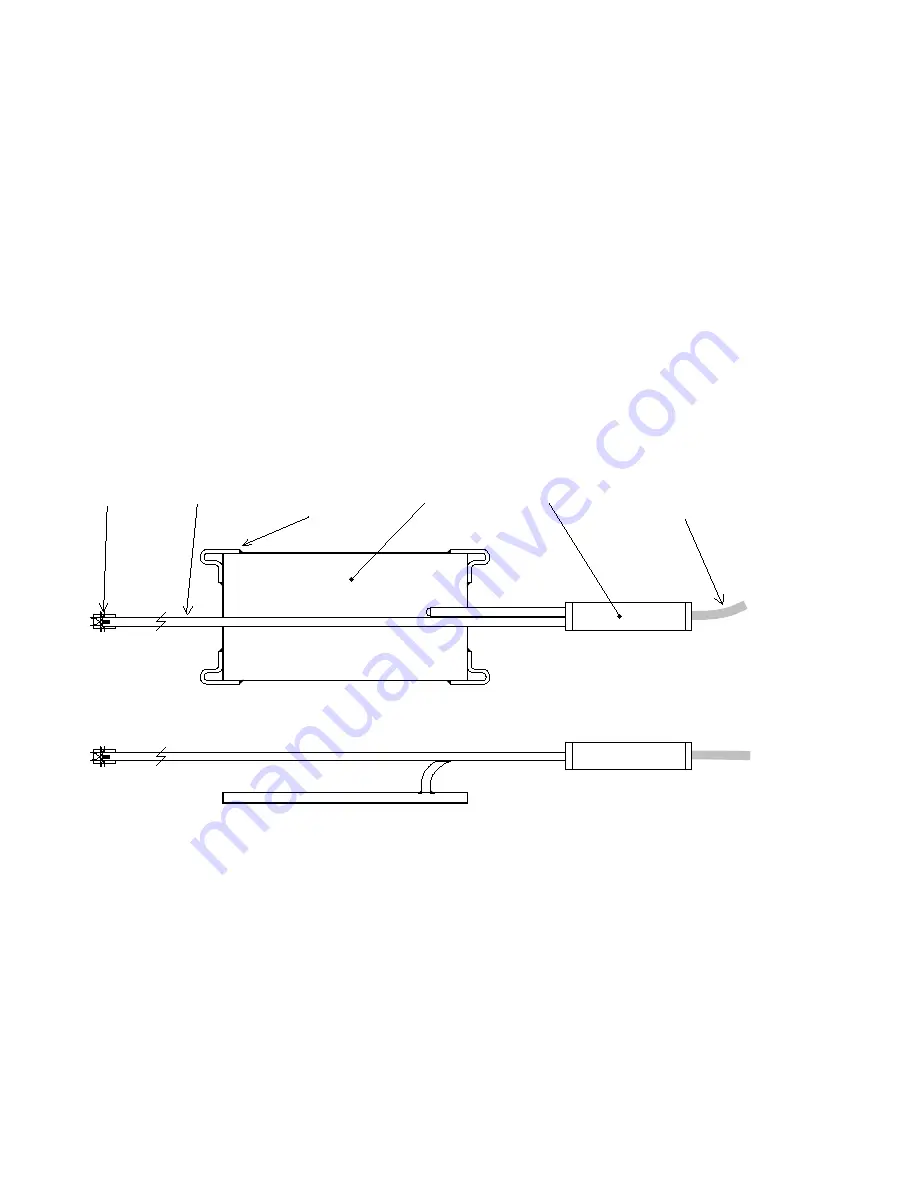
2
1.2 Stress Cell Design and Construction
The basic cell is comprised of two stainless steel rectangular plates welded together around their
periphery, leaving a thin space between the plates which is then filled with de-aired hydraulic
oil*. This fluid filled space is connected via a pressure tube to a vibrating wire pressure sensor.
Pressure applied normal to the plate is balanced by a corresponding build-up of internal fluid
pressure which is measured by the sensor.
Lugs are provided at the corners of the rectangular plates to facilitate holding the cells in place
while the shotcrete is applied.
One further refinement is required; this is the pinch tube, which is filled with mercury or de-aired
hydraulic oil and is connected at one end to the fluid filled space between the plates and the other
end is capped. The purpose of this pinch tube is to inflate the cell when the concrete around it has
fully cured and has cooled off to the ambient temperature. During concrete curing, temperatures
very often rise and will cause the cell to expand in the still green concrete. On cooling, the cell
contracts leaving a space between it and the surrounding concrete which, if allowed to remain,
would prevent the transmission of pressures from the concrete to the cell.
Pinch Tube
Stress Cell
Transducer Housing
Instrument Cable
(4 conductor, 22 AWG)
Mounting Lug
Seal Screw
(4 places)
Side View
Top View
Figure 2 - Model 4850 Concrete Stress Cell
The vibrating wire sensor is a standard Geokon Model 4500H transducer inside an all welded
housing. The sensor is hermetically sealed and is connected via waterproof connectors to an
electrical cable leading to the readout location. The sensor housing also incorporates a thermistor
which permits measurement of temperature at the cell location.
* Most other commercially available concrete stress cells are filled with mercury in order to
achieve a sufficient cell stiffness. However, the filling procedures and the construction details of
the Geokon cell are such that mercury is not required.
Summary of Contents for 4850
Page 2: ......
Page 4: ......
Page 27: ...21 APPENDIX D TYPICAL CALIBRATION REPORT Figure 11 Typical Calibration Report ...