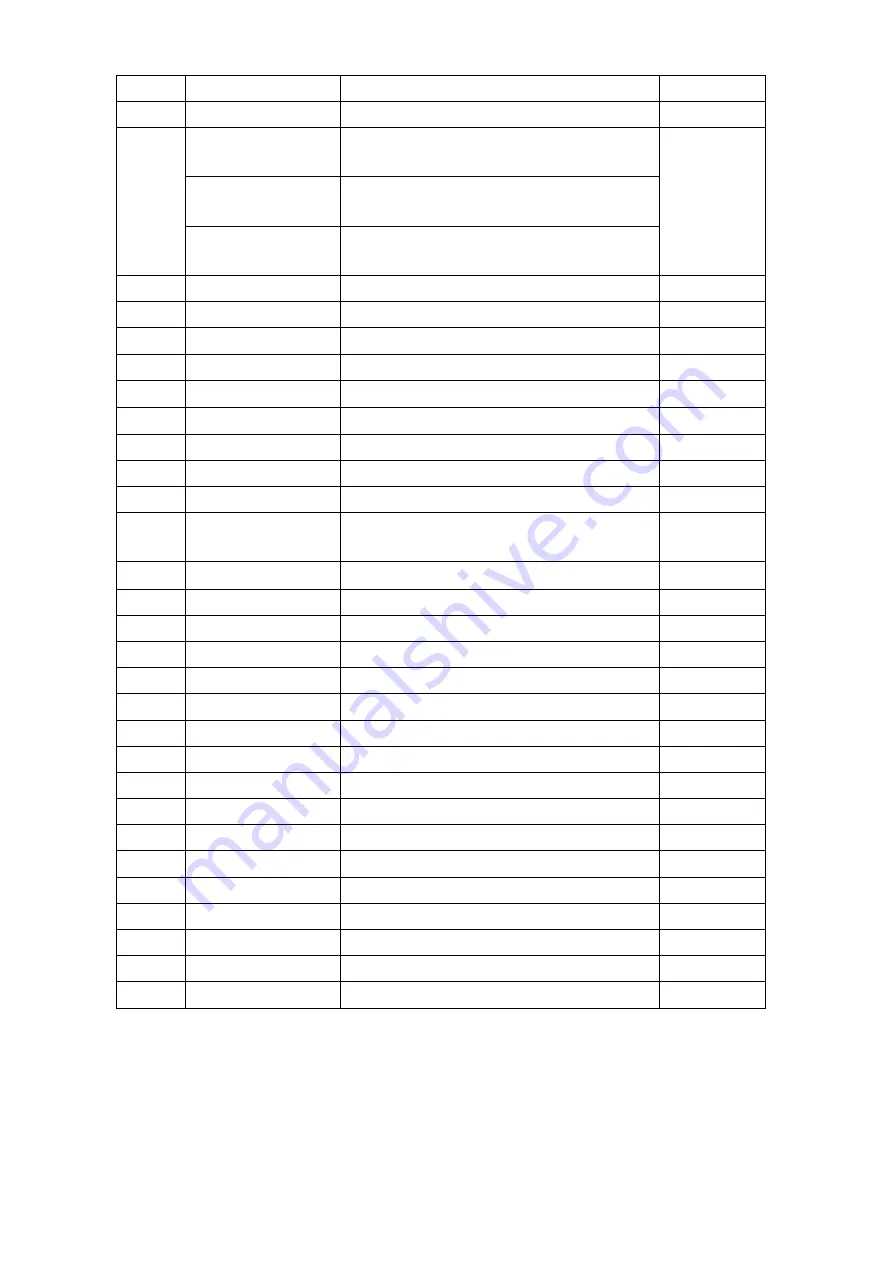
NO.
PART NO.
Name & Specifications
QTY
1
CH150.001
Hedge trimmer
1
2
CHJ150.011
Hanging Weldment(EURO
Hitch)
1
CHG150.011
Hanging Weldment(SMS
Hitch)
CHS150.011
Hanging Weldment(Skidder
Hitch)
3
CHJ150.012
Beam Weldment
1
4
CHJ150.013
Rotation Seat Weldment
1
5
GB/T889.1‐2000
Lock Nut M20
2
6
GB/T97.1‐1987
Plain Washer
2
7
GB
/
T1096‐1979
Key A 8x22
1
8
CHJ150.102
Bearing 30*34*30
2
9
GB/T5783‐2000
Bolt M14*35
4
10
GB/T889.1‐2000
Lock Nut M14
4
11
GB/T5783‐2000
Bolt M12*35
2
12
GB
/
T70
.
1‐2000
Soket head cap screw
M10x40
1
13
JB
/
T7940
.
1‐1995
Oil Cup M8
1
14
CHJ150.014
Swing Arm Weldment
1
15
CHJ150.015
Cylinder
1
16
CHJ150.016
Support Leg
2
17
GB/T97.1‐1987
Plain Washer
2
18
R Pin 3.2
2
19
1G135.00.107
Plug Pin
2
20
Safety Valve
1
21
DV26.001
Solenoid Valve
1
22
GB/T5783‐2000
Bolt M8x80
2
23
GB/T889.1‐2000
Lock Nut M8
2
24
CP5.60.104
Adapter R1/2‐M18*1.5
8
25
CHJ150.017
Oil Hoses
4
26
CHJ150.018
In‐out oil hose
2
27
LA‐H10L
One‐ way throttle valve
4
28
Washer 18
8
29
Adapter 18‐18
6
Summary of Contents for BJ 120
Page 1: ...OPERATION AND MAINTENANCE MANUAL...
Page 6: ...6...
Page 13: ......
Page 25: ...25 Fig 38 Screws and nuts Fig 42 Correct installed position...
Page 26: ......
Page 38: ...PARTS DRAWINGS AND LISTS...