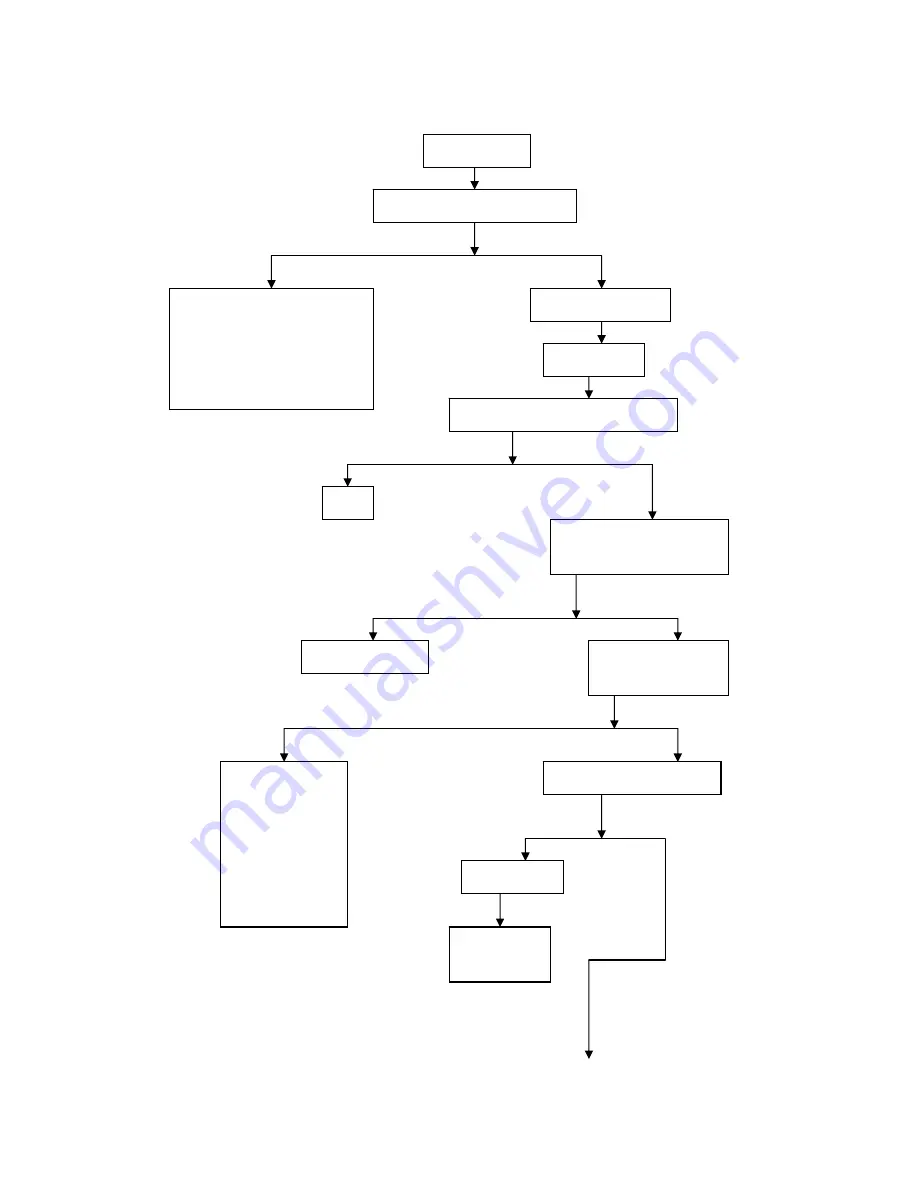
- 22 -
Y
N
Y
N
Y
N
N
Y
Y
N
Diagnosis on engine overheating
Engine overheating
Check whether operation is correct
1.
Check whether gasoline grade is
improper or stored for a long
time
2.
Check whether the engine works
at high speed for a long time or
with overload during driving
Check cooling system
Air-cooled engine
Check whether heat sink is spotted or there
is too much oil stain
Clean
Check whether cooling fan or air
director is damaged (forcedly
air-cooled engine)
Inspection & solution
Check whether ignition is
timely conducted with an
ignition timing light
1.
Check whether
CDI ignition
device is in good
condition
2.
Check whether
flywheels and
trigger coil are
loosened
Check whether clutch is slipping
Slipping clutch
Solution to
slipping clutch
Summary of Contents for Onyx 50
Page 2: ...ONYX Service Manual Generic Motor GmbH ...
Page 8: ... 6 18 5 Solution for idle discharge value exceeding defined value two stroke 169 ...
Page 21: ... 19 system I D of brake drum rear wheel φ140mm QJ50QT 22D ...
Page 54: ... 52 ...
Page 79: ... 77 Bulbs Switches Meters ...
Page 93: ... 91 Body Panel ...
Page 105: ... 103 Rear wheel rear suspension ...
Page 113: ... 111 Fuel tank ...
Page 126: ... 124 oil pump assembly 机油泵组件 machine oil pump assembly 机油泵组件 ...
Page 137: ... 135 Cylinder body and piston ...
Page 145: ... 143 Driving disc clutch driven wheel ...
Page 152: ... 150 挡圈 retaining ring 摩擦片 abrasion piece ...
Page 158: ... 156 离合器弹簧压缩器 spring compressor of clutch Decelerator device ...
Page 173: ...171 ...