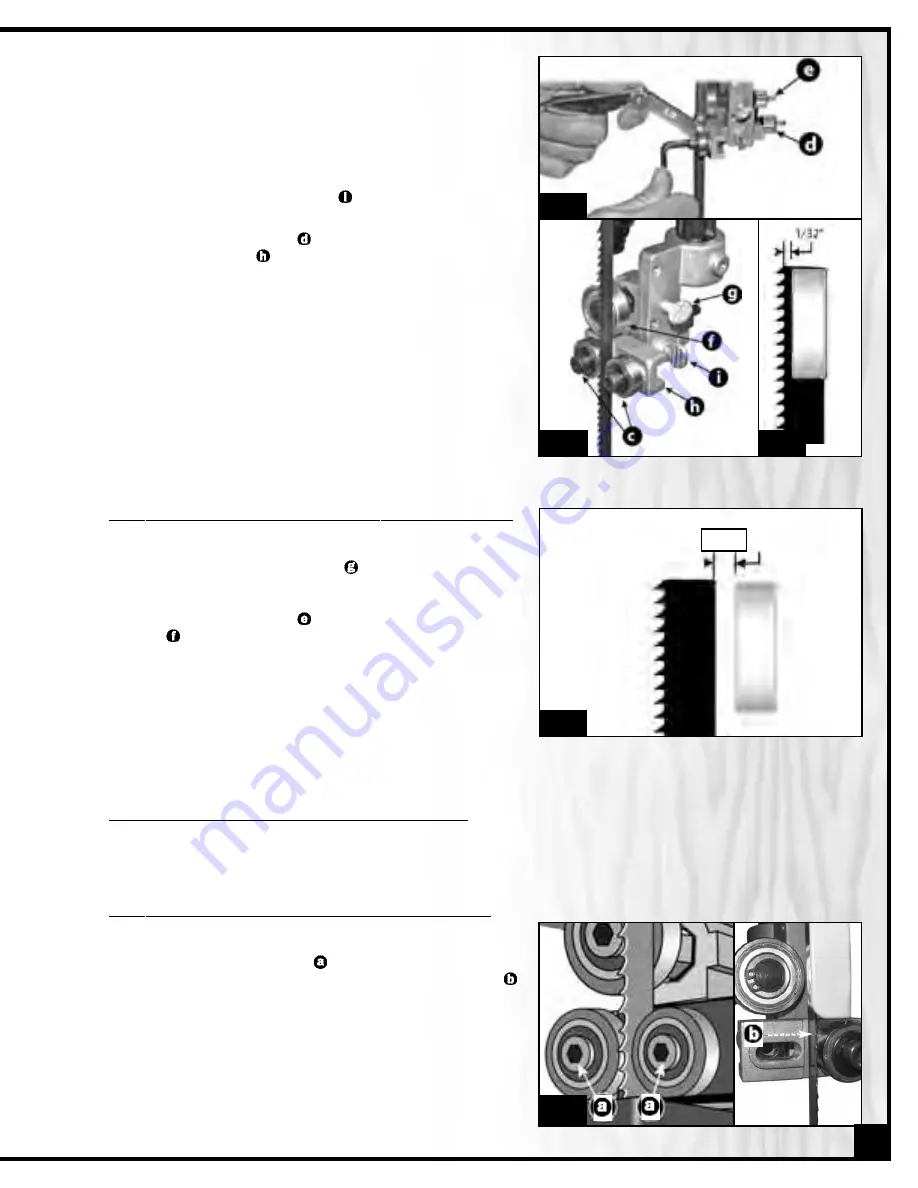
Adjust the positionning of the upper thrust bearing as follows:
1.
Loosen the upper thumb screw
. (Fig. 33)
2.
Turn the micro adjust nut
(Fig.32) to move the thrust bea-
ring
(Fig. 33) in or out until the bearing is 1/64” behind
the back edge of the blade (Fig. 35), then tighten the thumb
screw.
2.
Place a feeler gauge between one of the bearings and
the blade and tighten the Allen bolt until there is a 0.02"
gap left between the blade guide and the blade. (See Fig. 32)
3.
Repeat step 2. for the other guide on the other side of the
the blade.
4.
Loosen the lower thumb screw
. (See Fig. 33)
5.
Turn the micro adjust nut
(See Fig. 32) to move the guide
bearing assembly
(See Fig. 33) in or out until the guides
are at least 1/32” behind the blade teeth. (See Fig. 34) The
guides must remain behind the blade teeth to prevent da-
mage to the blade.
6.
Tighten the thumb screw to lock the guide bearing assem-
bly in position.
Fig. 32
1/64"
Fig. 35
POSITIONING THE LOWER BLADE GUIDES AND THRUST BEARING
The lower blade guides and thrust bearing perform the same function as the upper blade guides and thrust
bearing except they do so after the blade has contacted the stock being cut.
Adjust the positioning of the lower blade guide as follows:
1.
Loosen the two Allen bolts
and slide the two blade gui-
des along the elongated hole in the mounting bracket
toward the blade. (Fig. 36)
2.
Place a feeler gauge between one of the bearings and
the blade and tighten the Allen bolt until there is a 0.02"
gap left between the blade guide and the blade.
Fig. 33
Fig. 34
Fig. 36
23
Summary of Contents for 90-125 M1
Page 32: ...32 NOTES...