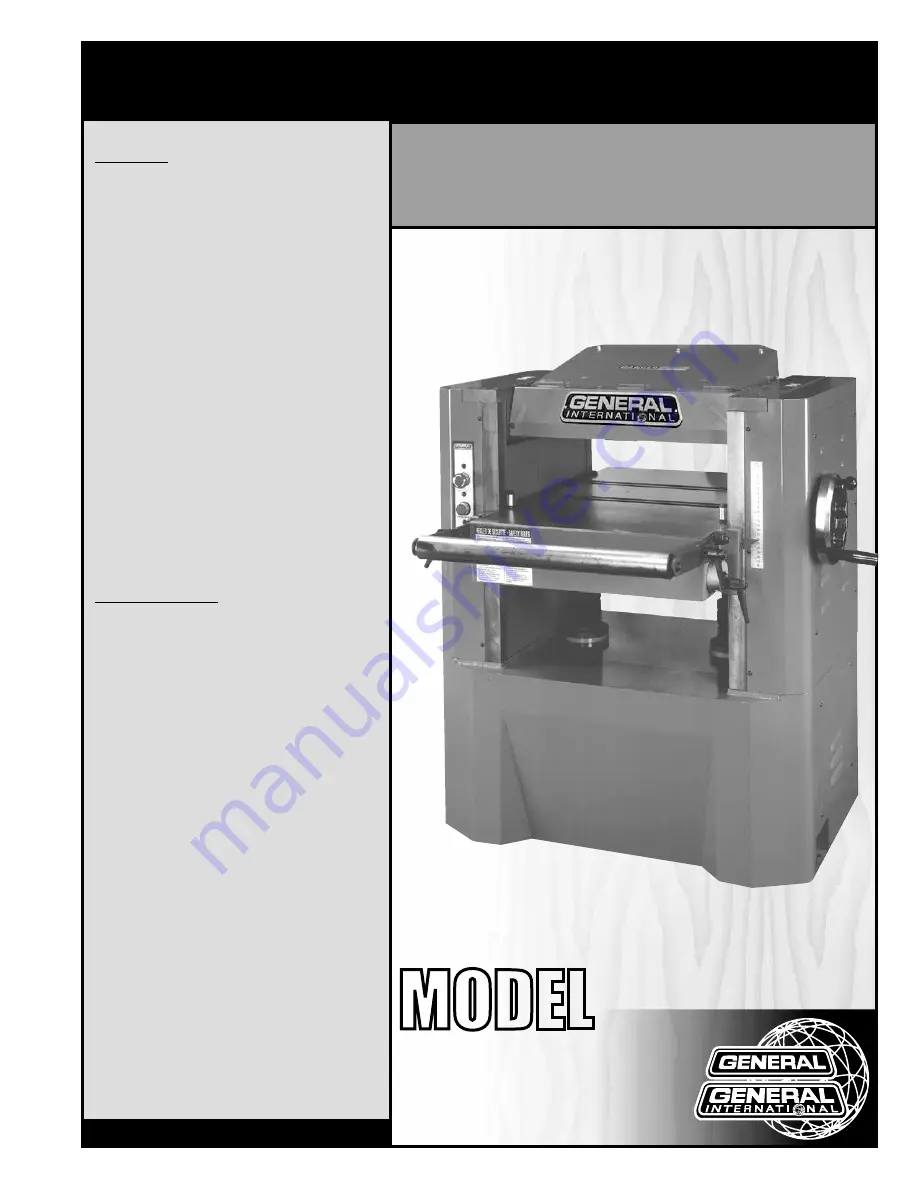
SETUP & OPERATION MANUAL
Version
#
1_Revision
#
2 - November 2015
© Copyright General International
20” SINGLE SURFACE PLANER
MODEL
#
30-360
#
30-360HC*
FEATURES
Positive gear design for quick and accurate
table adjustments.
5” dust collection hood.
Cast-iron table and head.
Four cutter knives result in easier cutting and
longer motor life, (helical cutter head model
available: #30-360HC).
Built-in table rollers reduce friction.
Large 8” handwheel quickly adjusts table
height.
Comes with magnetic safety switch.
Graduated scale in both inches and metric to
indicate workpiece thickness.
Anti-kickback fingers at the front of the infeed
roller to ensure maximum operator safety.
Vertical adjustment handle for table rollers.
Equipped with a sectioned infeed roller and a
rubber outfeed roller.
One front-mounted exterior table roller.
SPECIFICATIONS
• Table size
32” x 20” (813 x 508 mm)
• Maximum planing width
20” (508 mm)
• Min/Max thickness of stock
3/16” (5 mm) / 8” (204 mm)
• Minimum length of stock
8 1/4” (210 mm)
• Maximum cutting depth (full width)
1/8” (3 mm)
• Maximum cutting depth (width 8 1/2” or less)
1/4” (6 mm)
• Cutter head diameter
3 3/4” (97 mm)
• Cutter head speed
4500 rpm
• Feed speeds
(2) 22 & 28 fpm
• Cuts per inch (not applicable for HC model)
68.17 at 22 fpm & 53.5 at 28 fpm
• Number of knives / Inserts
4 - 30-360 / 58 - 30-460HC
• Base dimensions (l x w)
36” x 22” (914 x 559 mm)
• Motor
M1: 7 1/2 HP, 220 V, 1 Ph, 31 A
M2: 7 1/2 HP, 220 V, 3 Ph, 20 A
M3: 7 1/2 HP, 600 V, 3 Ph, 10 A
• Weight
1392 lbs (633 kg) - 30-360
1397 lbs (635 kg) - 30-360HC
*With helical cutter head