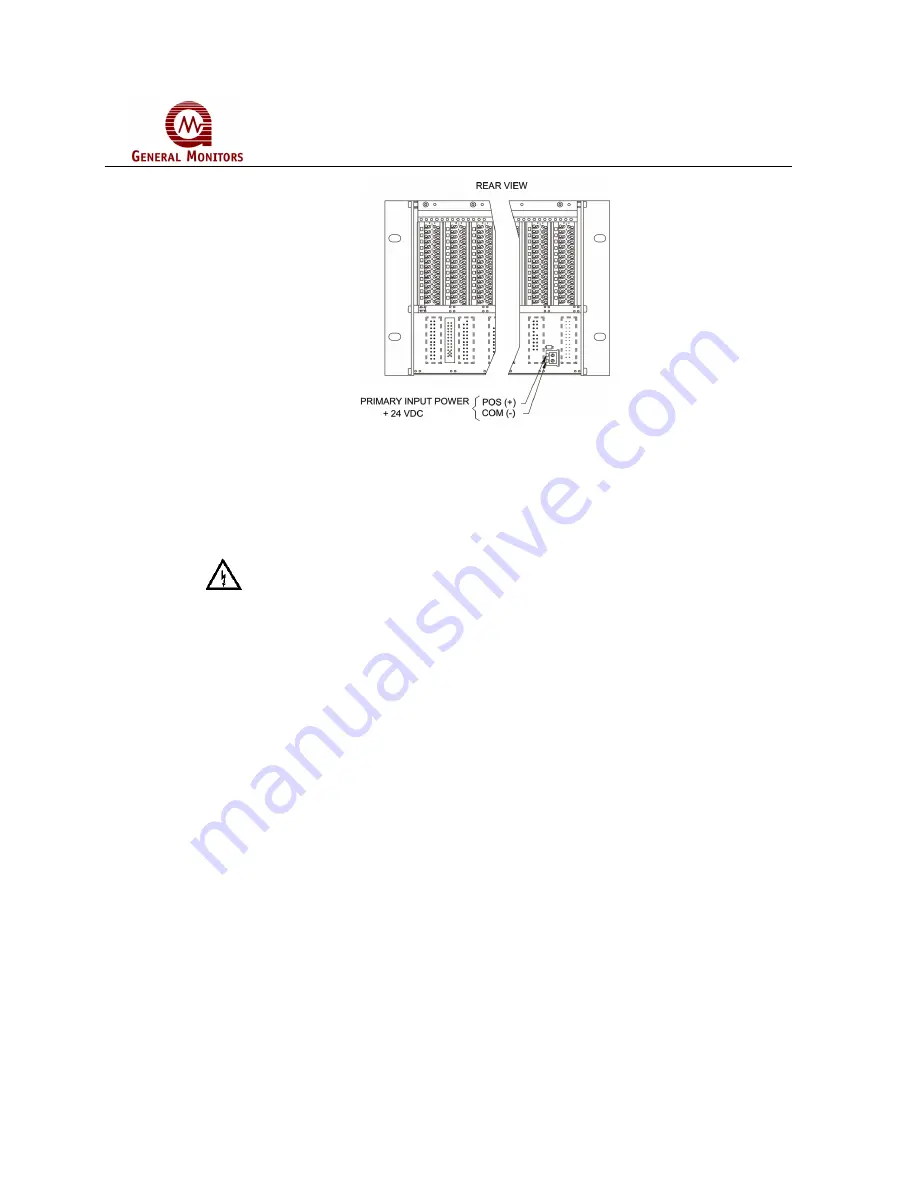
Model TA102A
16
Figure 36 – Power Connections
3.4 Sensor
Location
Considerations
There are no standard rules for sensor placement, since the optimum sensor location is
different for each application. The customer must evaluate conditions at the sensor site
in order to make this determination.
WARNING –
suitably skilled and competent personnel must carry out Installation and
Maintenance only.
3.4.1 General Sensor Location Considerations
•
The sensor should be easily accessible for calibration checks. Ensure that sufficient
clearance exists to allow the use of field calibration devices such as a Portable Purge
Calibrator for combustible gas applications.
•
The sensor head should always be pointing down to prevent water build up on the
sensing element. Remember that some combustible gases are heavier than air;
however, do not rely too heavily on this fact when selecting a sensor position.
•
The sensor should be located in areas where leaks are suspected (i.e. near valves &
pipe connections, etc.).
•
The sensor should not be placed where it may be coated by contaminating
substances may coat it.
3.5 Sensor
Poisons
Sensors may be adversely affected by prolonged exposure to certain atmospheres.
The more important poisons are:
•
Prolonged exposure to Hydrogen Sulfide (H
2
S) Gas
•
Halides (compounds containing Fluorine, Chlorine, Bromine and Iodine)
•
Heavy
Metals
(e.g. Tetraethyl lead)
Silicones contained in greases or aerosols are the most common “coating” agents.
These are not true sensor poisons, but reduce sensor response. Other damaging
materials, which attack the sensor physically, include mineral acids and caustic vapors.
The presence of such poisons and vapors does not exclude the use of General Monitors
Catalytic Bead Sensors. A careful analysis of ambient conditions should be undertaken
and the customer should be aware that sensor calibration might need to occur at more
frequent intervals.