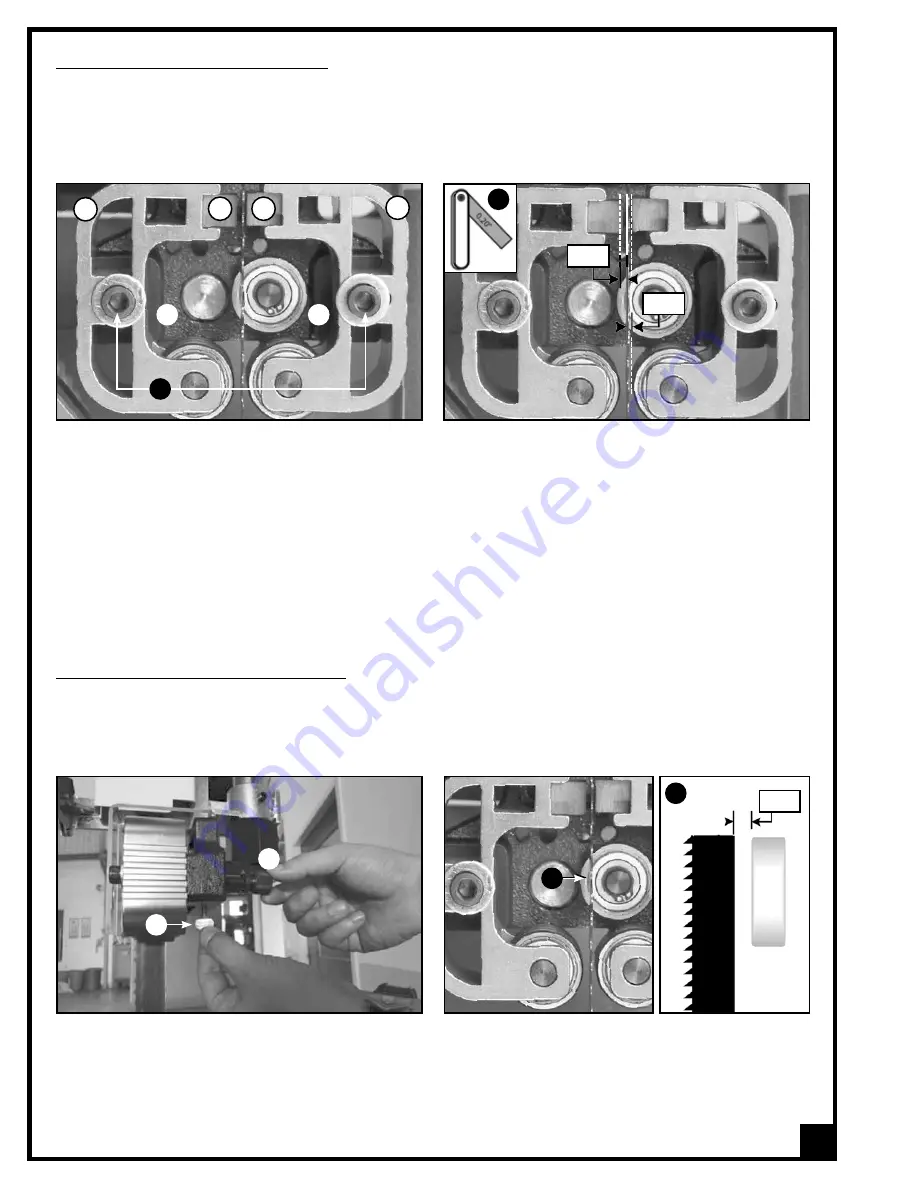
POSITIONING THE UPPER/LOWER THRUST BEARING
The thrust bearings keep the blade from moving back and out of position when the work is being fed into the blade
and must be very close to the back of the blade to prevent damage to the blade during cutting.
Adjust the positioning of the upper and lower thrust bearings as follows:
A
B
F
C
C
D
D
E
0.02”
0.02”
1.
Using a 6 mm Allen key, loosen the two cap screws,
A.
2.
Adjust the left and right mounts
B
that hold the bakelite blocks
C
and guide bearings
D
to obtain a space of
0.02” (the thickness of a sheet of paper) between the blade and blocks & bearings.
Tip: Place a feeler gauge
C
or sheet of paper between the blocks & bearings and the blade to make sure there is a 0.02”
space.
3.
Re-tighten the two cap screws
A
to lock the mounts in position.
4.
Repeat steps 1 to 3 with the lower blade guides.
1.
Loosen thumb screw
D.
2.
Turn the adjustment knob
E
to move the thrust bearing in or out, until the bearing
F
almost touches the blade
(is 1/64” behind the back of the blade
G
).
3.
Re-tighten thumb screw
D
to lock the thrust bearing in position.
4.
Repeat steps 1 to 3 with the lower thrust bearing.
POSITIONING THE UPPER/LOWER BLADE GUIDES
The space between each bearing and the blade must not exceed 0.02” (the thickness of a sheet of paper ). If less
space is left, the blade will get stuck or jammed between both bearings. Too much friction will cause blade to over-
heat and break.
Adjust the positioning of the blade guides as follows:
D
E
G
19
1/64”
B