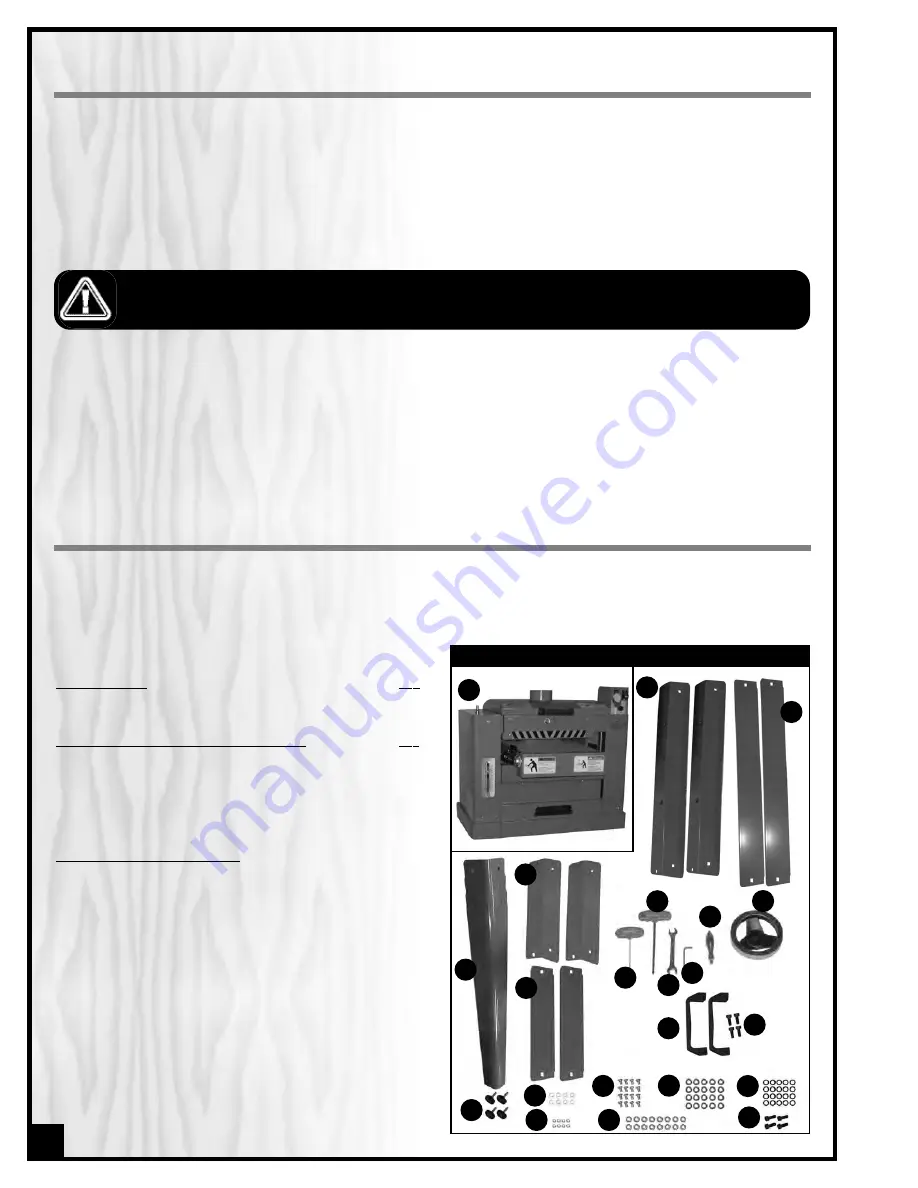
BASIC FUNCTIONS
This drum sander is designed for surface sanding of flat wooden panels, glue-ups and other natural wood products,
having a minimum length of 5” and up to a maximum width of 13”. The minimum/maximum capacity (workpiece
thickness range), is from 1/4” up to 3 3/4”. This sander is not intended (and should not be used) to sand any mate-
rial other than wood.
BASIC PRINCIPLES OF SANDING
It is always preferable to remove less material per pass and take multiple passes. This can extend sanding belt life,
place less strain on the motor and provide better workpiece finish quality.
Note: To avoid overworking the motor, creating a potential circuit overload, or damaging the sanding drum, do not
force the workpiece against or into the drum. For better finish results and to avoid potential damage to the sander
or the workpiece, let the workpiece feed into the sander at the rate of feed to which the conveyer is set.
Note: As with any other drum or belt sander, depending on the final finish quality you require, some final hand
sanding may be required.
DO NOT USE THIS SANDER AS A THICKNESS PLANER. NEVER ATTEMPT TO REMOVE MORE THAN THE DEPTH OF THE GRAIN OF THE
SANDING BELT IN ANY SINGLE PASS. TOO MUCH FRICTION WILL CAUSE BELT TO OVERHEAT AND WEAR PREMATURELY, AND, IN
EXTREME CASES, MAY CAUSE BURNS IN THE WORKPIECE.
UNPACKING
Carefully unpack and remove the sander and its components from the shipping crate and check for damaged or
missing items as per the list of contents below.
Note: Please report any damaged or missing items to your General International distributor immediately.
LIST OF CONTENTS
BOX 1 - SANDER
QTY
A
- 13” HORIZONTAL SINGLE DRUM SANDER.....................1
BOX 2 - OPEN STAND & OTHER COMPONENTS
QTY
B
- LONG TOP SHELF ...........................................................2
C
- LONG CROSS BRACE ....................................................2
D
- SUPPORT LEG .................................................................4
E
- SHORT TOP SHELF...........................................................2
F
- SHORT CROSS BRACE....................................................2
HARDWARE BAG INCLUDING:
G
-
HAND WHEEL.............................................................................1
H
-
HAND WHEEL HANDLE..............................................................1
I
-
5 MM ALLEN KEY ......................................................................1
J
-
6 MM T-HANDLE ALLEN WRENCH ............................................1
K
-
2 MM T-HANDLE ALLEN WRENCH ............................................1
L
-
12- 14 MM OPEN END WRENCH..............................................1
M
-
CARRYING HANDLE ..................................................................2
N
-
CAP SCREW...............................................................................4
O
- LEVELING FOOT .............................................................4
P
- FLAT WASHER..................................................................8
Q
- HEX NUT .........................................................................8
R
- SHOULDER BOLT...........................................................16
S
- HEX NUT .......................................................................16
T
- LOCK WASHER .............................................................20
U
- FLAT WASHER................................................................20
V
- CAP SCREW ...................................................................4
8
D
O
P
Q
R
S
T
U
V
BOX 1
A
H
G
I
K
J
L
M
N
BOX 2
B
C
E
F