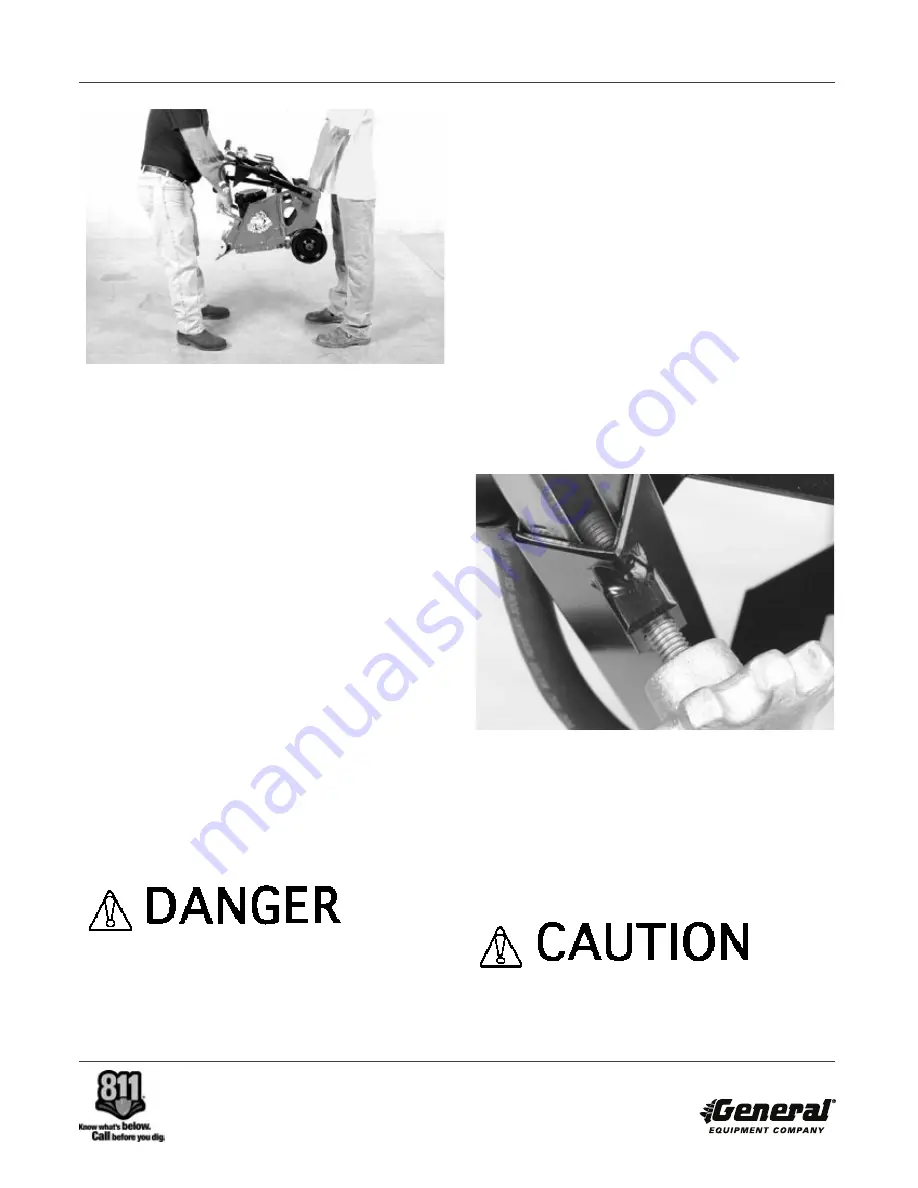
FCS16 RIP-R-STRIPPER
FORM GOM4240301, VERSION 3.1
20
FIGURE 19
2) To minimize the possibility of damage to the RIP-R-
STRIPPER, always transport in its normal, upright
position. All equipment must be secured in/on
vehicles with suitable strapping or tie-downs.
Personnel should not be transported in the same
compartment as equipment. Consult applicable OSHA
and transportation regulations (local, State and
Federal) for the proper transportation of the RIP-R-
STRIPPER.
3) Do not transport the RIP-R-STRIPPER with a blade
or the ceramic tile ripper attachment attached to the
main frame in the following configurations:
a) To and from the job site.
b) For longer distances while being repositioned on
the job site.
c) When traversing up and down stairways.
d) While performing maintenance and/or repairs.
e) Lifting up/into or/down from a transporting vehicle.
Remove the blade or ceramic tile ripper attachment
according to the procedures as outlined in this manual
for the above listed configurations.
LIFTING, LOWERING AND TRANSPORTING
THE RIP-R-STRIPPER WITH A BLADE OR
CERAMIC TILE RIPPER ATTACHMENT
INSTALLED CAN RESULT IN PROPERTY
DAMAGE AND/OR PERSONAL INJURY.
4) When transporting to and from the job site, block
the bottom of the main frame to prevent direct impact
blows against the exciter plate. This procedure will
reduce impact loads directly to the elastomeric rubber
mounts, minimize their deflection and increase service
life.
ADJUSTING THE OPERATOR HANDLE
HEIGHT.
The RIP-R-STRIPPER incorporates a handle that can
be adjusted to compensate for variances in operator
height. Handle height can be infinitely varied between
the stop limits. No external tools are required. Correct
handle height can increase overall machine
productivity and reduce operator fatigue.
1) Loosen the handle knobs located at the rear of the
handle. Extend the knobs out approximately 1/2 inch
(13 mm). FIGURE 20.
FIGURE 20
2) Position the operator handle grips at a height
convenient to the specific operator. In most
configurations, the operator handle grips will be at
approximately waist level.
3) Tighten the handle knobs finger tight. Determine
the adjustable section of the operator handle is
properly secured tight against the fixed section.
Improper knob tension and/or improperly
securing the operator handle to the main
frame can result in an unstable platform
configuration. An unstable platform
Summary of Contents for RIP-R-STRIPPER FCS16
Page 2: ...Left Blank ...
Page 36: ...FCS16 RIP R STRIPPER FORM GOM4240301 VERSION 3 1 34 Page Intentionally Left Blank ...
Page 51: ...FCS16 RIP R STRIPPER FORM GOM4240301 VERSION 3 1 49 Left Blank ...
Page 60: ...FCS16 RIP R STRIPPER FORM GOM4240301 VERSION 3 1 58 Decals FCS16 Floor Covering Scraper ...