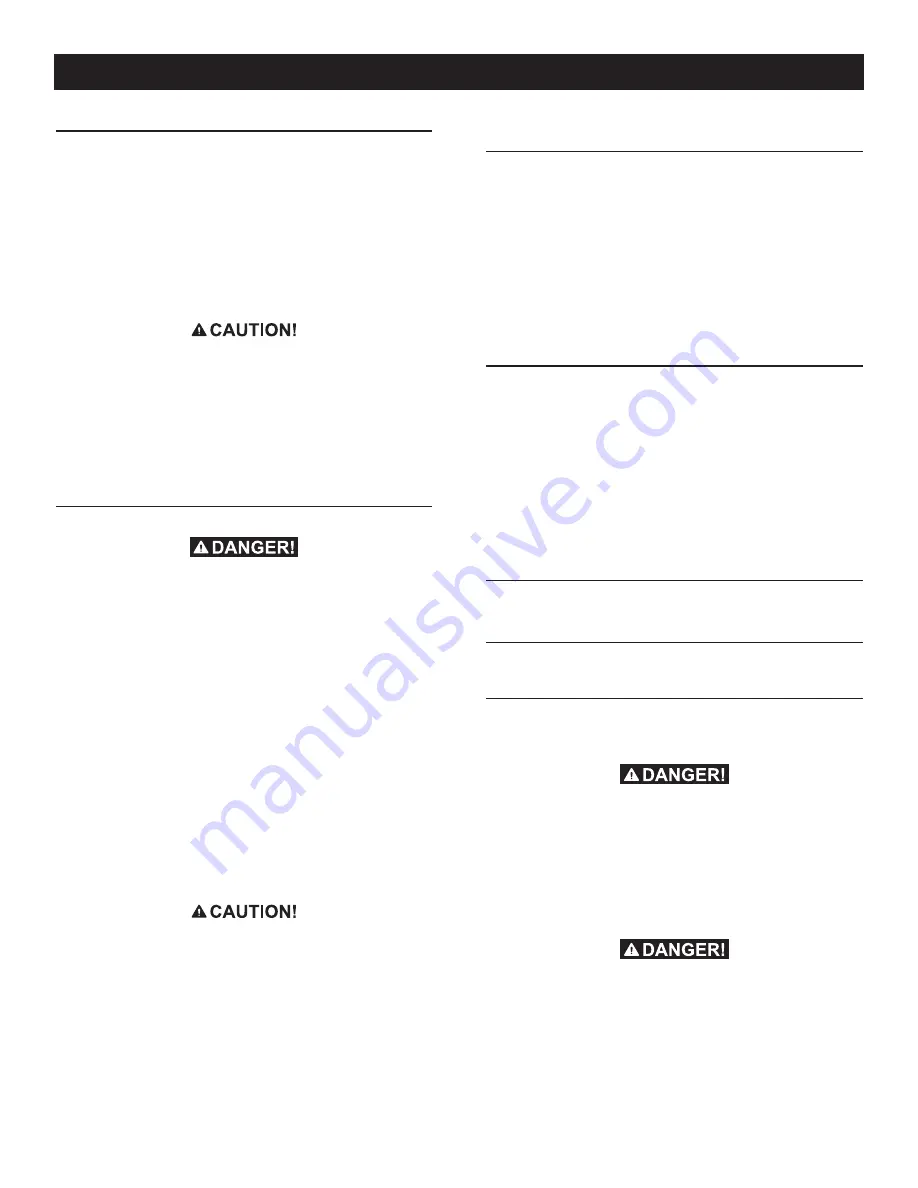
6
3.1
FUNCTIONAL TESTS AND
ADJUSTMENTS
Following transfer switch installation and intercon-
nection, inspect the entire installation carefully.
A competent, qualified electrician should inspect
it. The installation should comply strictly with all
applicable codes, standards, and regulations. When
absolutely certain the installation is proper and cor-
rect, complete a functional test of the system.
Perform functional tests in the exact order pre-
sented in this manual, or damage to the switch
could be done.
IMPORTANT: Before proceeding with functional tests, read and
make sure you understand all instructions and information in this
section. Also read the information and instructions of labels and
decals affixed to the switch. Note any options or accessories that
might be installed and review their operation.
3.2 MANUAL OPERATION
Do NOT manually transfer under load.
Disconnect transfer switch from all power
sources by approved means, such as a main
circuit breaker(s).
A manual HANDLE is shipped with the transfer switch. Manual
operation must be checked BEFORE the transfer switch is operated
electrically. To check manual operation, proceed as follows:
1. Turn the generator’s AUTO/OFF/MANUAL switch to OFF.
2. Turn OFF both UTILITY and EMERGENCY power supplies to
the transfer switch, with whatever means provided (such as
the main line circuit breakers).
3. Note position of transfer mechanism main contacts by
observing display windows in “A” and “B” in Figure 3.1 as
follows:
• Window “A” ON, Window “B” OFF - LOAD terminals (T1, T2)
are connected to utility terminals (N1, N2).
• Window “A” OFF, Window “B” ON - LOAD terminals (T1, T2)
are connected to emergency terminals (E1, E2).
Do not use excessive force when operating the
transfer switch manually or the manual handle
could be damaged.
3.2.1 CLOSE TO NORMAL SOURCE SIDE
Before proceeding, verify the position of the switch by observing
window “A” in Figure 3.1 on page 6. If window “A” reads “ON”,
the contacts are closed in the normal position, no further action is
required. If it reads “OFF”, proceed with Step 1.
• Step 1: With the handle attached to the actuating shaft, move
handle in the direction of the arrow on the switch cover
until it stops — DO NOT FORCE. Release handle slowly
to allow the spring in the switch box to relax. “ON” now
appears in Window “A” and “OFF” appears in Window
“B”.
3.2.2 CLOSE TO EMERGENCY SOURCE SIDE
Before proceeding, verify the position of the switch by observing
window “B” in Figure 3.1 on page 6. If window “B” reads “ON”, the
contacts are closed in the EMERGENCY (STANDBY) position. No
further action is required. If it reads “OFF”, proceed with Step 1.
• Step 1: With the handle attached to the actuating shaft, move
the handle in the direction of the arrow on the switch
cover until it stops - DO NOT FORCE. Release handle
slowly to allow the spring in the switch box to relax.
“OFF” now appears in Window “A” and “ON” appears
in Window “B”.
3.2.3 RETURN TO NORMAL SOURCE SIDE
Manually actuate switch to return Window “A” to the “ON” posi-
tion.
3.3 VOLTAGE
CHECKS
3.3.1 UTILITY VOLTAGE CHECKS
1. Turn ON the UTILITY power supply to the transfer switch with
whatever means provided (such as the UTILITY maim line
circuit breaker).
PROCEED WITH CAUTION. THE TRANSFER
SWITCH IS NOW ELECTRICALLY HOT.
CONTACT WITH LIVE TERMINALS RESULTS
IN EXTREMELY HAZARDOUS AND POSSIBLY
FATAL ELECTRICAL SHOCK.
2. With an accurate AC voltmeter, check for correct voltage.
Measure across ATS terminal lugs N1 and N2; N1 to NEUTRAL
and N2 to NEUTRAL.
FAILURE TO TURN OFF THE UTILITY SUPPLY
BEFORE WORKING ON THE UTILITY CON-
NECTIONS OF THE ATS WILL RESULT IN
EXTREMELY DANGEROUS AND POSSIBLY
FATAL ELECTRICAL SHOCK.
5. When certain that UTILITY supply voltage is correct and
compatible with transfer switch ratings, turn OFF the UTILITY
supply to the transfer switch.
Operation
Summary of Contents for Nexus smart
Page 1: ...This manual should remain with the unit Technical Manual Nexus Smart Switch...
Page 11: ...9 Interconnection Drawing No 0H7453 C Electrical Data...
Page 12: ...10 Electrical Data Wiring Diagram Schematic Drawing No 0H7257 C...
Page 13: ...11 Wiring Diagram Schematic Drawing No 0H7257 C Electrical Data...
Page 14: ...12 Parts List on page 14 Exploded Views Parts Lists 400A Assembly Drawing No 0H7267 C...
Page 15: ...13 Parts List on page 14 400A Assembly Drawing No 0H7267 C Exploded Views Parts Lists...
Page 18: ...16 Notes...
Page 19: ...17 Notes...
Page 20: ...Part No 0H7443 Revision C 08 05 11 Printed in U S A...
Page 21: ......
Page 23: ......
Page 24: ......
Page 25: ......
Page 26: ......
Page 27: ......
Page 28: ......
Page 29: ......