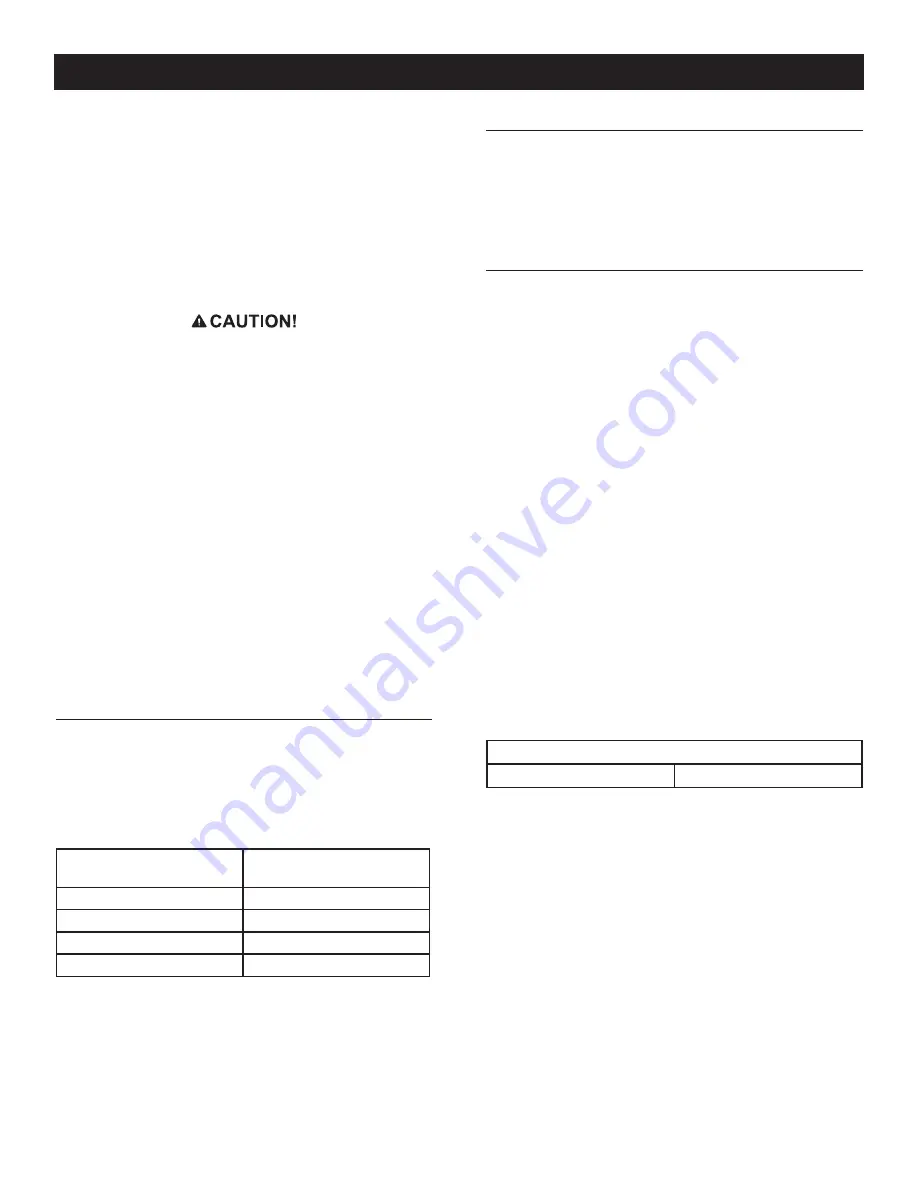
4
Before connecting wiring cables to terminals, remove any surface
oxides from the cable ends with a wire brush. All power cables
should enter the switch next to transfer mechanism terminals.
If ALUMINUM conductors are used, apply corrosion inhibitor to
conductors. Tighten terminal lugs to the torque values as noted on
the decal located on the inside of the door. After tightening terminal
lugs, carefully wipe away any excess corrosion inhibitor.
All power cables should enter the switch next to the transfer
mechanism terminals.
Use a torque wrench to tighten the conductors,
being sure not to overtighten, or damage to the
switch base could occur. If undertightened, a
loose connection would result, causing excess
heat which could damage the switch base.
Connect power source load conductors to clearly marked transfer
mechanism terminal lugs as follows:
1. Connect UTILITY (NORMAL) power source cables to switch
terminals N1, N2.
2. Connect EMERGENCY (STANDBY) source power cables to
transfer switch terminals E1, E2.
3. Connect customer LOAD leads to switch terminals T1, T2.
4. Connect neutral conductors of UTILITY, EMERGENCY and
customer LOAD to the neutral block.
Conductors must be properly supported, of approved insulative
qualities, protected by approved conduit, and of the correct wire
gauge size in accordance with applicable codes.
Be sure to maintain proper electrical clearance between live metal
parts and grounded metal. Allow at least 1/2 inch for 100-400
amp circuits.
2.4
CONNECTING START CIRCUIT
WIRES
Control system interconnections consist of UTILITY 1 (N1), 2 (N2),
Load (T1) and leads 23 and 194. Recommended wire gauge sizes
for this wiring depends on the length of the wire, as recommended
below:
MAXIMUM WIRE LENGTH
RECOMMENDED WIRE
SIZE
460 feet (140m)
No. 18 AWG.
461 to 730 feet (223m)
No. 16 AWG.
731 to 1,160 feet (354m)
No. 14 AWG.
1,161 to 1,850 feet (565m)
No. 12 AWG.
2.5
CONNECTING LOAD SHED
MODULE (LSM) CONNECTIONS
The LSM can control an air conditioner (24 Vac) directly or a sepa-
rate contactor (120 Vac) which can control any load connected to
it. See Figure 2.2.
2.5.1 SEQUENCE OF OPERATION
The 4 green status LEDs will indicate when a load priority level is
enabled.
• All loads are enabled when the transfer signal is off. (ATS in
Utility position).
• If the transfer signal is pulled low (Active)
• All loads are enabled until an overload is detected
• When an overload is detected all loads are disabled
• After 5 minutes priority 1 loads are enabled.
• After another 30 seconds priority 2 loads are enabled
• After another 30 seconds priority 3 loads are enabled
• After another 30 seconds priority 4 loads are enabled
If an overload is detected within 30 seconds of a level being
enabled, all loads are disabled again and the sequence repeats.
However, the level that caused the overload and all levels higher
will not be enabled again for 30 minutes.
Control of Air Conditioner Load
1. Route the thermostat cable (from the furnace/thermostat to
the outdoor air conditioner unit) to the transfer switch.
2. Connect the wire to the terminal strip terminals (Air 1) on
the LSM as shown in Figure 2.2. These are normally closed
contacts which open upon load shed conditions. Route ther-
mostat wire away from High voltage wires.
3. If required, connect the second air conditioner to the terminal
strip terminals (Air 2).
Contact Ratings
Air 1 & 2
24 VAC, 5.0 Amps Max
NOTE:
These instructions are for a typical air conditioner installation.
Control of heat pump and 2-stage air conditioners will require
special connections.
Control of a Separate Contactor
A separate contactor relay module can be purchased from the
manufacturer. If a different relay is used it must have a 120 Vac
coil voltage. The LSM supplies fused (5A) 120 Vac to energize the
coils of the relay contactors (contactor 1, 2, 3 or 4).
1. Mount the contactor module and connect the load to the main
contacts.
2. Connect the contactor coil to the desired LSM (contactor 1, 2,
3 or 4) terminals on the terminal strip.
3. Connect additional load shedding contactors in a similar fash-
ion.
Installation
Summary of Contents for Nexus smart
Page 1: ...This manual should remain with the unit Technical Manual Nexus Smart Switch...
Page 11: ...9 Interconnection Drawing No 0H7453 C Electrical Data...
Page 12: ...10 Electrical Data Wiring Diagram Schematic Drawing No 0H7257 C...
Page 13: ...11 Wiring Diagram Schematic Drawing No 0H7257 C Electrical Data...
Page 14: ...12 Parts List on page 14 Exploded Views Parts Lists 400A Assembly Drawing No 0H7267 C...
Page 15: ...13 Parts List on page 14 400A Assembly Drawing No 0H7267 C Exploded Views Parts Lists...
Page 18: ...16 Notes...
Page 19: ...17 Notes...
Page 20: ...Part No 0H7443 Revision C 08 05 11 Printed in U S A...
Page 21: ......
Page 23: ......
Page 24: ......
Page 25: ......
Page 26: ......
Page 27: ......
Page 28: ......
Page 29: ......