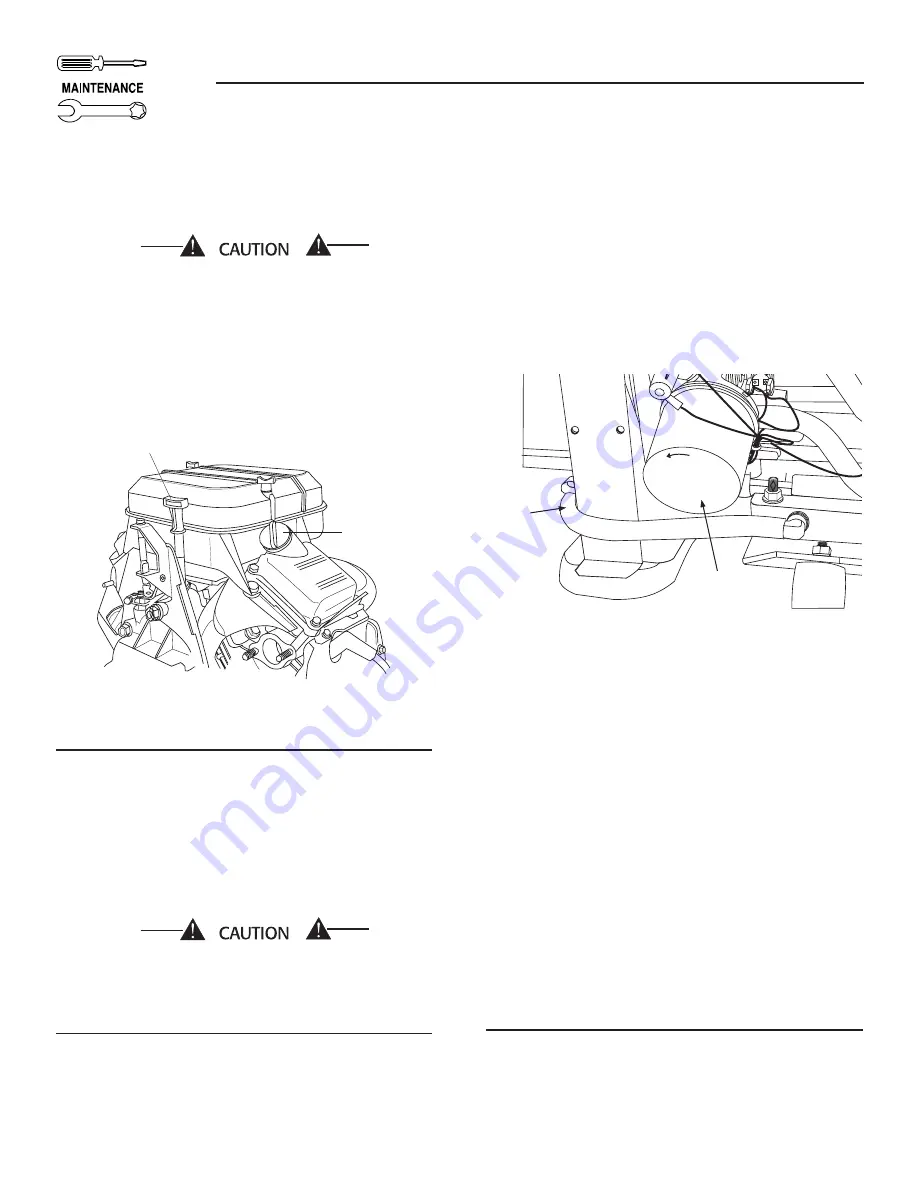
3. Install the dipstick; then, remove it again. The oil
level should be at the dipstick “Full” mark. If nec-
essary, add oil to the “Full” mark only. DO NOT
FILL ABOVE THE “FULL” MARK.
Never operate the engine with the oil level
below the “Add” mark on the dipstick. Doing
this could damage the engine.
4. Install
the
dipstick.
5. Reset the AUTO/OFF/MANUAL switch to its origi-
nal position.
Figure 4.3 — Oil Dipstick and Fill,
12 kW and 15 kW
Oil Dipstick
Oil Fill
4.3 CHANGING THE ENGINE OIL
4.3.1 ENGINE OIL RECOMMENDATIONS
Use oil of American Petroleum Institute (API) Service
Class SG, SH or SJ. Use all season SAE 5W-30
Synthetic oil. Organic break-in oil is required before
using synthetic oil.
NOTE:
The unit is supplied with “break-in” oil. See the
“Break-in Procedure,” Section 3.1, for the first
required oil change.
Any attempt to crank or start the engine before
it has been properly serviced with the recom-
mended oil may result in an engine failure.
4.3.2 OIL CHANGE PROCEDURE
To change the oil, proceed as follows:
1. Run the engine until it is thoroughly warmed up
then shut OFF the engine.
2. Immediately after the engine shuts OFF, pull the
oil drain hose (Figure 4.4) free of its retaining
clip. Remove the cap from the hose and drain the
oil into a suitable container.
3. After the oil has drained, replace the cap onto the
end of the oil drain hose. Retain the hose in the
clip.
4. Refill with the proper recommended oil (see
Section 4.3.1). See Section 1.5.2 for oil capaci-
ties.
Figure 4.4 – Oil Drain Hose and Filter
Oil Filter
Oil
Drain
Hose
Loose
n
4.4 CHANGING THE OIL FILTER
Change the engine oil filter as follows:
1. With the oil drained, remove the old oil filter by
turning it counterclockwise.
2. Apply a light coating of clean engine oil to the
gasket of the new filter. See Section 1.5.1 for rec-
ommended filter.
3. Screw the new filter on by hand until its gasket
lightly contacts the oil filter adapter. Then, tighten
the filter an additional 3/4 to one turn (Figure
4.4).
4. Refill with the proper recommended oil (see
Section 4.3.1). See Section 1.5.2 for oil capaci-
ties.
5. Start the engine and check for leaks.
4.5
CHANGING THE ENGINE
AIR CLEANER
4.5.1
7 KW, 12 KW AND 15 KW
GENERATORS
See Figures 1.1 and 1.2, for the location of the air
cleaner. Use the following procedure (Figure 4.6):
1. Turn the two screws counterclockwise to loosen.
2. Remove the cover and air filter.
Section 4 — Maintenance
Air-cooled 7 kW, 12 kW and 15 kW Generators
18