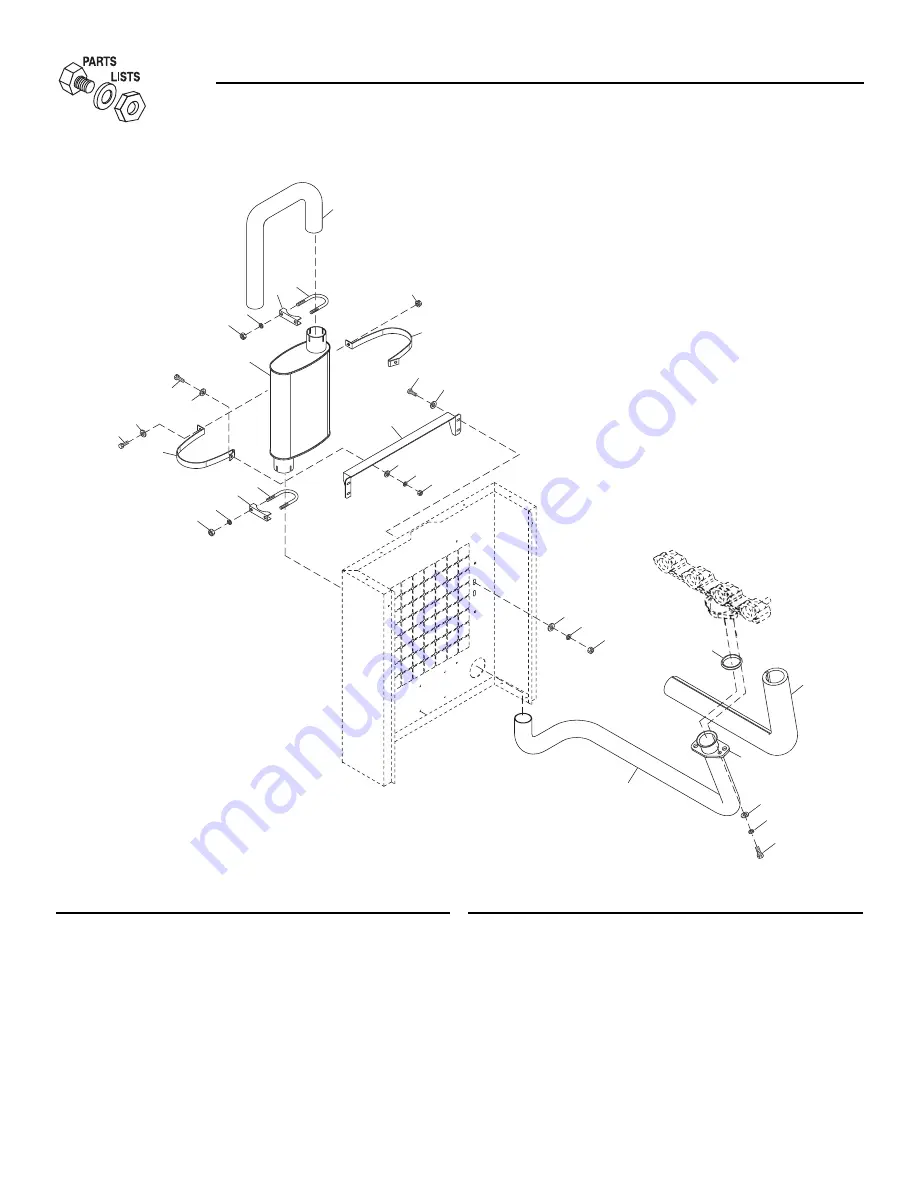
ITEM
PART NO.
QTY.
DESCRIPTION
1
0F2912
1
PIPE MUFFLER OUT
2
0F2869
1
PIPE EXHAUST 2.5L FORD
3
0F2823
1
MUFFLER 2.5L FORD
4
036434
2
BOLT U 5/16-18 X 2.09
5
036449
2
SADDLE 2 INCH
6
022129
6
WASHER LOCK M8-5/16
7
022259
4
NUT HEX 5/16-18 STEEL
8
0E0170A
1
EXHAUST BLANKET 938MM
9
044149
1
GASKET EXHAUST RING
10
0E8816
1
EXHAUST FLANGE 2" PIPE
11
0F2925
2
STRAP MUFFLER
12
0F2926
1
BRACKET, MUFFLER
ITEM
PART NO.
QTY.
DESCRIPTION
13
047411
4
SCREW HHC M6-1.0 X 16 G8.8
14
022097
4
WASHER LOCK M6-1/4
15
022473
8
WASHER FLAT 1/4-M6 ZINC
16
049813
4
NUT HEX M6 X 1.0 G8 YEL CHR
17
039253
2
SCREW HHC M8-1.25 X 20 G8.8
18
045771
2
NUT HEX M8-1.25 G8 YEL CHR
19
0A4010
1
SCREW HHC M8-1.25 X 60 G8.8 FT
20
022145
5
WASHER FLAT 5/16-M8 ZINC
21
022131
2
WASHER FLAT 3/8-M10 ZINC
22
085917
2
WASHER LOCK 3/8 SS
23
0D2611
2
SCREW HHC 3/8-16 X 1-3/4 SS
24
052858
1
NUT TOP LOCK FL M8-1.25
17
19
20
11
7
6
4
5
7
20
3
6
5
2
12
4
20
18
6
15
13
24
11
1
16
15
14
9
8
22
21
10
23
48 Generac
®
Power Systems, Inc.
Section 8 - Exploded Views and Parts
Guardian Liquid-cooled 25 kW Generator
Muffler — Drawing No. 0F2930-B