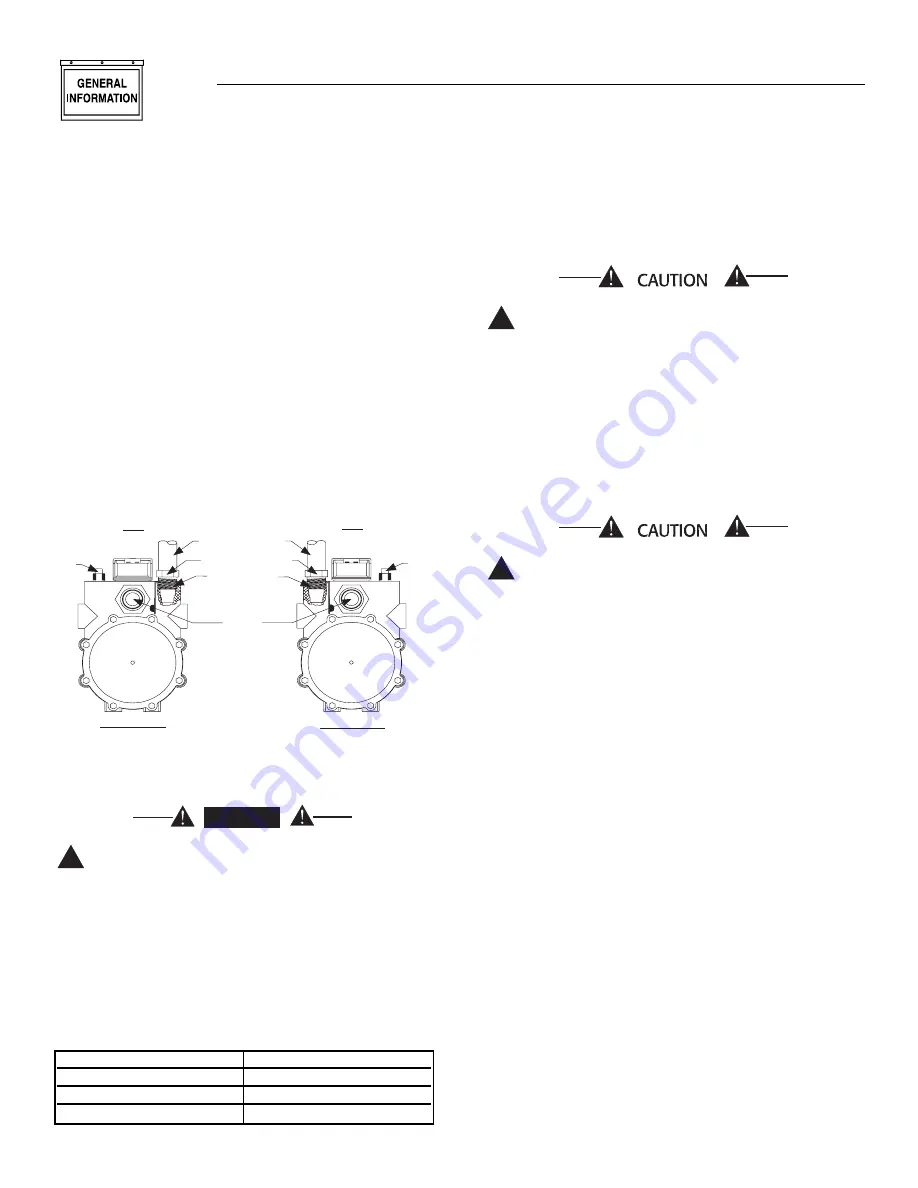
8
2. Remove the carburetor fuel hose from the outlet
port (Port 1) of the demand regulator (Figure
1.8).
3. Remove the brass hose fitting from the outlet port
(Port 1) of the demand regulator.
4. Remove pipe plug from Port 2.
5. Install brass hose fitting into Port 2.
6. Install pipe plug into Port 1.
7. Connect carburetor gas hose to brass fitting.
8. Tighten all clamps and plugs.
9. Make sure fuel supply is of the proper pressure
and type for configuration (not to exceed 14 inch-
es water column).
10. Move DIP switch position 4 on the control board
to the off position (LP vapor, see Figure 3.2 and
Section 3.7).
11. Reverse the procedure to convert back to natural
gas.
Figure 1.8 — Reconfigure the Fuel System
NOTE:
Port 1 is for NG only and Port 2 is for LP vapor
only. No provision for dual fuel has been made.
Serious injury or damage may occur if not con-
figured properly. Please consult an Authorized
Service Dealer with any questions.
1.14 ENGINE OIL RECOMMENDATIONS
The unit has been filled with 15W-40 engine oil at the
factory. Use a high-quality detergent oil classified “For
Service CC, SD, SE, SF.” Detergent oils keep the
engine cleaner and reduce carbon deposits. Use oil
having the following SAE viscosity rating, based on
the ambient temperature range anticipated before the
next oil change:
NOTE:
Synthetic oil is highly recommended when the
generator will be operating in ambient tempera-
tures which regularly exceed 90° F and/or fall
below 30° F.
Any attempt to crank or start the engine before
it has been properly serviced with the recom-
mended oil may result in an engine failure.
1.15 COOLANT RECOMMENDATIONS
Use a mixture of half low silicate ethylene glycol base
anti-freeze and half deionized water. Cooling system
capacity is about 8 U.S. quarts (7.6 liters). Use only
deionized water and only low silicate anti-freeze. If
desired, add a high quality rust inhibitor to the rec-
ommended coolant mixture. When adding coolant,
always add the recommended 50-50 mixture.
Do not use any chromate base rust inhibitor
with ethylene glycol base anti-freeze or chromi-
umhydroxide (“green slime”) forms and will
cause overheating. Engines that have been
operated with a chromate base rust inhibitor
must be chemically cleaned before adding eth-
ylene glycol base anti-freeze. Using any high
silicate anti-freeze boosters or additives will
also cause overheating. DO NOT use any solu-
ble oil inhibitor for this equipment.
1.16 BEFORE INSTALLATION
Before installing this equipment, check the ratings of
both the generator and the transfer switch. Read
“Emergency Isolation Method” and “Total Circuit
Isolation Method” in the installation manual (Part No.
079699).
The generator’s rated wattage/amperage capacity
must be adequate to handle all electrical loads that
the unit will power. It may be necessary to group the
critical (essential) loads together and wire them into
a separate “emergency” distribution panel.
This generator can be installed in conjunction with
an engineered transfer switch, if necessary (see
Section 2.10).
The standard prepackaged transfer switch (ATS
mode) does not have sensing or controlling circuit
boards. Instead, the generator control console hous-
es a “Printed Circuit Board Assembly”, which con-
trols all phases of operation, including engine start
up and load transfer.
!
!
!
DANGER
NG FUEL SYSTEM
LP FUEL SYSTEM
Port 1
Port 2
FUEL HOSE
BRASS HOSE
FITTING
OUT
PORT 2
PLUG
FUEL HOSE
BRASS HOSE
FITTING
FUEL INLET
PLUG
OUT
PORT 1
Temperature
Oil Grade (Recommended)
Above 80° F (27° C)
SAE 30W or 15W-40
32° to 80° F (-1° to 27° C)
SAE 20W-20 or 15W-40
Below 32° F (0° C)
SAE 10W or 15W-40
Section 1 — General Information
Liquid-cooled 15, 20 and 25 kW Generators