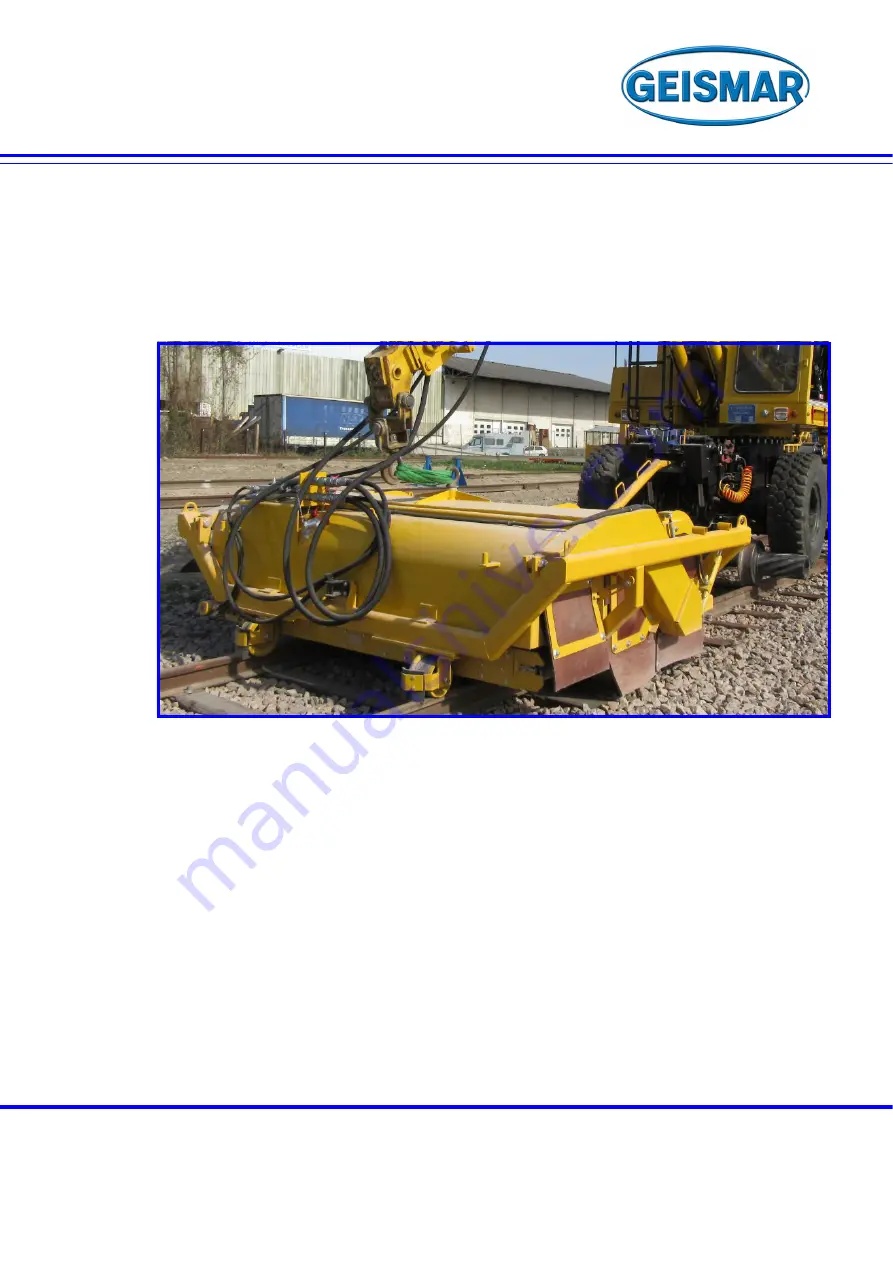
Société des Anciens Etablissements
L.GEISMAR
113 bis, avenue Charles de Gaulle
92200 NEUILLY SUR SEINE
Tél : +33 (0)1 41 43 40 40
- Fax : 33 (0) 1 46 40 71 70
E-mail : [email protected]
Société des Anciens Etablissements
L.GEISMAR
Boite Postale 50327 5 rue d’Altkirch
68006 COLMAR CEDEX FRANCE
Tél : +33 (0) 3 89 80 41 90 - Fax : 33 (0) 3 89 80 42 28
E-mail : [email protected]
OPERATION & MAINTENANCE INSTRUCTIONS
Model
TRACK BRUSHING TOOL
Type
BRV
GB
Code :
H110200_0118
Summary of Contents for BRV
Page 2: ......
Page 6: ......
Page 17: ...Page 17 Société des Anciens Établissements L GEISMAR Prohibited Reproduction 3 2 Dimensions ...
Page 22: ......
Page 36: ......
Page 42: ......
Page 44: ......
Page 46: ......
Page 48: ......
Page 49: ...Section A Mechanical Components ...
Page 51: ......
Page 53: ......
Page 55: ......
Page 57: ......
Page 59: ......
Page 61: ......
Page 63: ......
Page 65: ......
Page 67: ......
Page 69: ......
Page 70: ......
Page 71: ...Section B Hydraulic Components ...
Page 73: ......
Page 75: ......
Page 76: ......
Page 77: ......
Page 79: ......
Page 81: ......
Page 83: ......
Page 84: ......
Page 85: ...Optional Components ...
Page 87: ......
Page 89: ......
Page 91: ......
Page 93: ......
Page 94: ......