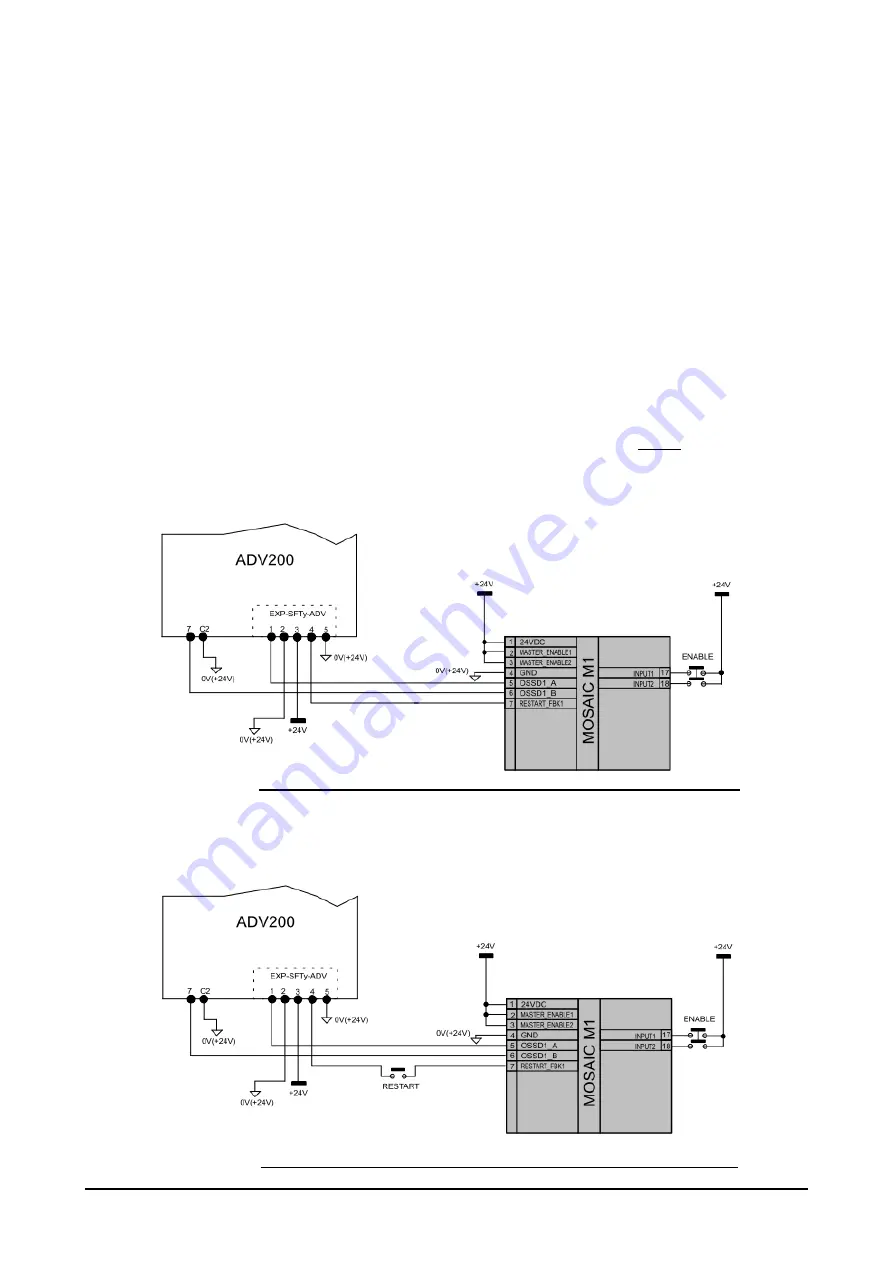
User manual ADV200-…-SI with External Safety Modules
Page 10 of 13
All safety functions that check for risks operate by running the drive-integrated STO function, which
disengages the motor from the drive system torque. In addition to implementing the STO function, safety
modules can protect the system by applying other means (motor brakes, mechanical blockage, etc.)
according to the machine-related function.
4.2 STO Wiring
All safety module functions listed above must be programmed correctly and coherently based on the specific
machine safety requirements as described in Chapter 1.
The following diagram covers several installation possibilities, as the STO wiring does not depend on the
performed function, while still fulfilling the specific functions described in paragraphs §5.1, §5.2, §5.3 and
§5.4. Indeed, all safety functions, in cases when work interruption is called for, require the activation of the
Safe Torque Off (STO) function as a means for machine shutdown or return to safe operation.
To allow the safety modules to activate the ADV200 STO function and, at the same time, to monitor the STO
state through inputs with automatic reactivation configuration, the wiring diagram in Figure 4 should be used.
In this diagram, the outputs of safety module M1 (OSSD1_A, OSSD2_B) control the ADV200 Enable and
STO Enable inputs. The Feedback output of the STO function is fed to the Restart_Fbk1 input so that the
module can automatically check the machine status and restart it (if programmed to do so).
Figure 4.
Connecting the safety module for activating the STO function with automatic restart.
Figure 5 shows a diagram that requires/allows a manual restart, using a special safety function button
(RESTART).
Figure 5.
Connecting the safety module for activating the STO function with a manual restart.