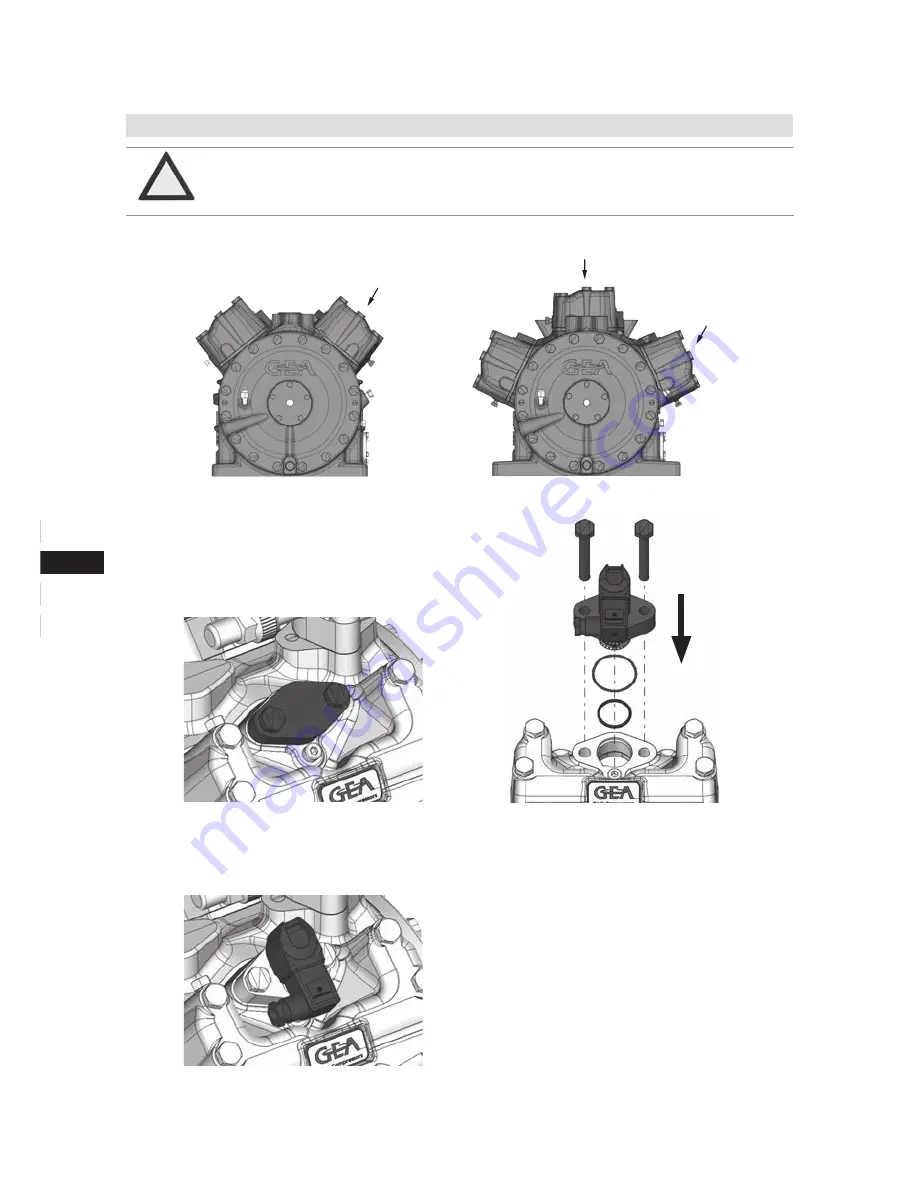
30
D
GB
F
E
96416-03.2017-DGbFEIRu
8.1 Capacity regulator
Fig. 22
CR 1
CR 2
ATTENTION
If the capacity regulator is installed at the factory, it is subsequently
installed and connected by the customer.
8
|
Accessories
CR 1
Delivery condition 1 (from the factory):
Cylinder cover prepared for capacity regulator.
Fig. 24
Before commissioning, the blind flange with
screws must be removed and replaced by the
new set capacity regulator with O-ring joints
and screws. Observe position and construction
of the capacity regulator.
Attention! Compressor is under pressure!
Depressurize the compressor first.
Delivery condition 2 (from the factory):
Connect capacity regulator in terminal box or
switch cabinet.
Fig. 23
Fig. 25
HG44e
HG56e