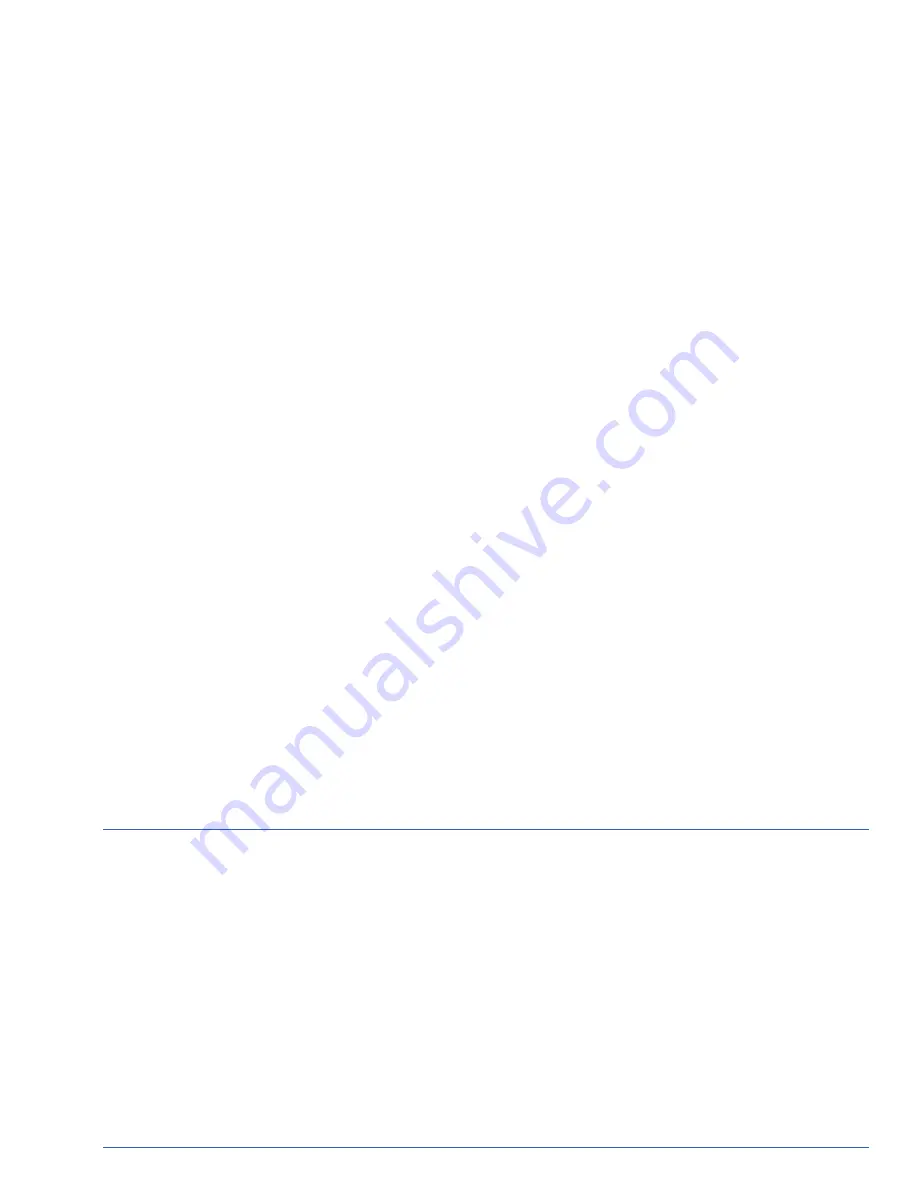
Zenith ZTS Series Automatic Transfer Switches
Universal Motor
Disconnect (UMD):
This load control discon-
nects a large motor via
its control circuit for an
adjustable period of time
prior to transfer in either
direction. For switching
multiple motors, GE’s
Accessor
y UMD
discon-
nects the motors prior
to transfer and brings
them back on line
sequentially.
Accessory R50:
This is
an in-phase monitor
that compares the phase
angle between both
sources of power and
prevents transfer until
the two are approximately
in phase (within a self-
adjusting range). GE’s high
speed transfer action,
coupled with the MX
series microprocessor
control logic, ensure
closures at or near zero
degree phase difference.
Series ZTSD:
GE
offers
delayed transition
switching on transfer
switches rated 40 amperes
and above – the GE Zenith
ZTSD
Series. This pro-
grammed center-off
position allows for the
full decay of rotating
motors or transformer
fields. It can also be
used for load shedding
of selected circuits or
other applications which
require a means to dis-
connect the load from
either source. Major UPS
system manufacturers
recommend delayed
transition switches for
proper restart sequencing
of their systems.
Series ZTSCT:
GE
’s Zenith
series of closed transition
switches combine ZTSD
operation during a source
failure with a highly
engineered control system
that allows momentary
paralleling (100 ms) of
two acceptable sources,
thereby limiting the
impact of transfer
on the load.
Electrical Ratings
• Ratings 40 to 4000 amperes
• 2, 3 or 4 Poles
• Open type, NEMA 1, 3R, 4, 4X and 12
• Available to 600 VAC, 50 or 60 Hz
• Suitable for emergency and standby
applications on all classes of load,
100%
tungsten rated through 400 amps
• UL 1008 listed at 480 VAC
• CSA C22.2 No. 178 certified
at 600 VAC
• IEC 947-6-1 listed at 480 VAC
Performance Features
• Contact transfer speed
less than
100
milliseconds
• High close-in and withstand capability
• Temperature rise test per UL 1008
conducted after overload and endurance
tests
- exceeds UL requirements
• Available in ZTS (utility-generator), ZTSU
(utility-
utility), ZTSG (generator-generator)
and ZTSM
(manual) configurations
Design and Construction Features
• Double throw, interlocked operation
• Electrically operated, mechanically held
by a
simple, over-center mechanism
• Segmented silver tungsten alloy
contacts
with separate arcing
contacts on 225
amp and above
• Arc quenching grids, enclosed arc
chambers, and wide contact air gap
for
superior source-to-source isolation
on all
units
• Control circuit disconnect plug and
drive
inhibit switch for safe maintenance
• Components accessible for inspection
and
maintenance without removal of
the switch
or power conductors
• Mechanical indicator and contact
chamber cover designed for inspection,
safety and position designation
Page 3
•
PB
-5066
The Zenith ZTS Series is the building block of our transfer switch
product line. This ruggedly built power contactor family of switches
has been specifically designed for transfer switch duty with
dependability, versatility and user friendliness of prime concern.
ZTS
switches are available in open type construction for switchboard
installation or nema enclosed to the customer’s specifications. The
power panel components, consisting of power switching contacts,
drive mechanism and terminal lugs, are mounted on a specially
formed panel. Logic devices including microprocessor control
auxiliary time delays and special accessory equipment are
assembled on the door for ease of maintenance and separation
from the power section. They are connected with a numbered
wiring harness equipped with a disconnect plug that allows
isolation of the control panel for maintenance.
ZTS Series Method of Operation
When Source 1 voltage fails or drops to a predetermined point
(usually 80% of nominal), if required, a circuit is closed to start
the engine generator set. When Source 2 reaches 90% of rated
voltage and 95% of rated frequency, the drive solenoid is energized
through the Source 2 coil control relay, causing the main contacts to
disconnect the load from Source 1 and connect it to Source 2.
After the drive solenoid has completed its electrical stroke and
is seated, the Source 2 coil control relay opens to disconnect it. The
transfer switch is now mechanically locked in the Source 2 position.
When Source 1 voltage is restored to a predetermined point
(usually 90% of nominal), the control voltage sensing energizes.
The Source 1 side coil relay closes, and after the drive solenoid
has completed its electrical stroke and is seated, the coil control
relay opens to disconnect it. The transfer switch is now mechanically
locked in the Source 1 position.
Drive Mechanism
All Zenith ZTS
switches employ the simple “over-center” principle to
achieve a mechanically locked position in either Source 1 or
Source 2 and GE’s high speed drive assures contact transfer in
100ms or less. High contact pressure and positive mechanical
lock allow for high withstand and closing ratings, far exceeding
UL
requirements. All
ZTS
units are listed with UL
time-based
rating,
coordinated breaker and current limiting fuse ratings.
Open and Delayed Transition ATS mechanism does not allow
both sources to be connected at the same time.
Neutral Switching
The Zenith ZTS Series is available in true four pole designs for
multi-source power systems that require neutral switching. The
neutral contact is on the same shaft as the associated main contacts.
This ensures positive operation, and avoids any possibility that
the neutral contact will fail to open or close, as is possible when
the neutral pole is an add-on accessory. The neutral contacts
are identical to the main contacts, having the same current carrying
and high withstand/closing ratings as the mains. They are designed
to break last and make first to reduce the possibility of transients
while switching the neutral.
Safe Manual Operation
The ZTS manual operator consists of a large, easy-to-use handle
that fits securely for manual operation during installation and
maintenance or in an emergency.
The ZTS may be provided with an operator inhibit switch to dis-
connect the electrical drive prior to maintenance. Fully enclosed
wrap-around arc covers shield the main contacts and mechanical
components, preventing operator exposure during manual operation.
Transferring Large Motor or Highly Inductive Loads
Some loads, especially large motors, receive severe mechanical
stress if power is transferred out of phase while the motor is still
rotating. Also, back EMF generated by a motor may result in excess
currents that can blow fuses or trip circuit breakers. GE offers
four solutions to these problems:
•
Short Time rated 1600-3000A (Non-
bypass) ATS for 0.50 sec and 1.0 sec time
duration
•
Open Transition ATS perform break
before make operation on all phases