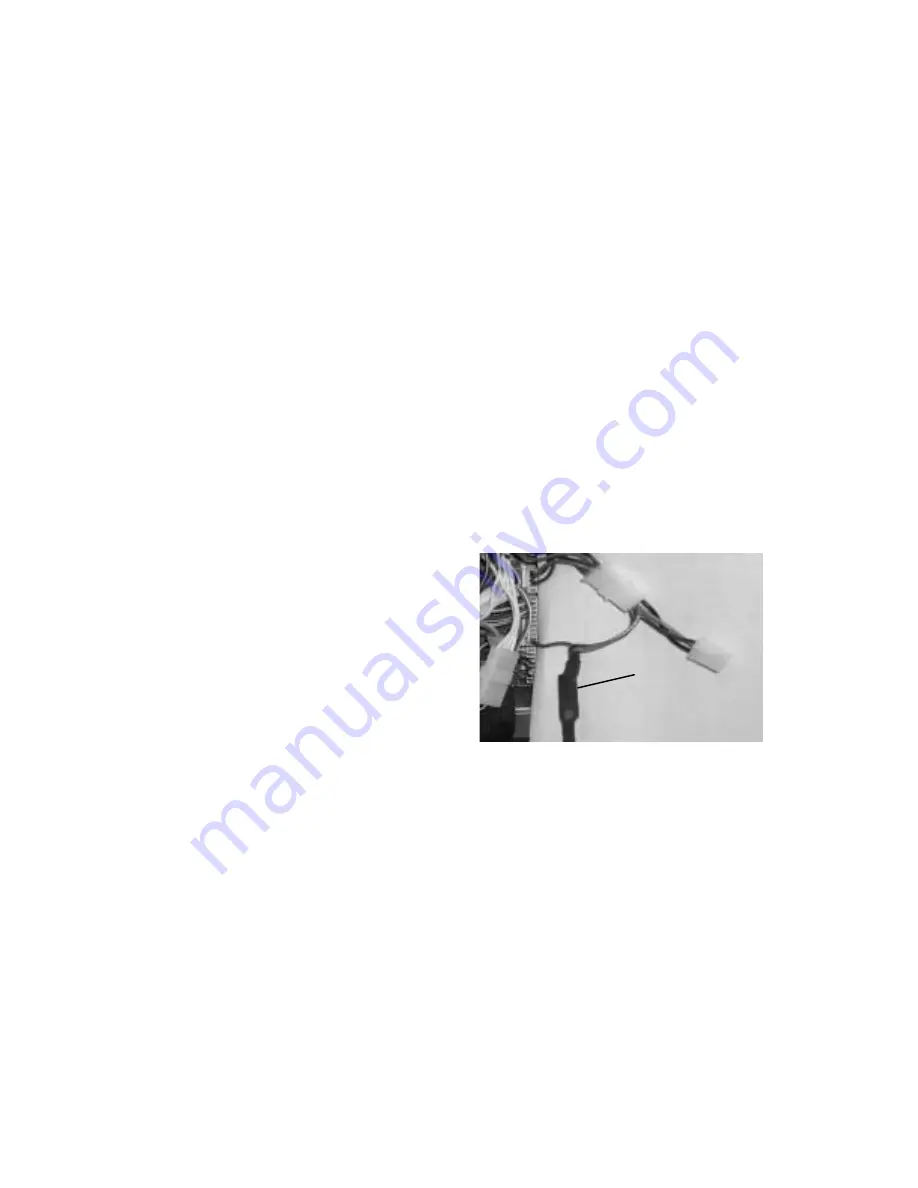
– 14 –
Inverter
Warning: Disconnecting the 6-pin connector does not disconnect power (120 VAC) from the
inverter. The refrigerator must be unplugged before servicing the inverter.
Note: Certain voltmeters will not be able to read voltage output from the inverter. If no voltage or erratic
voltage is measured, it does not necessarily indicate a faulty inverter.
The inverter receives 120 VAC line-in from the power supply. The inverter converts this single-phase,
60 Hz, 120 VAC into 3-phase, 230 VAC, with frequency variations between 57 Hz and 104 Hz. This
voltage is delivered to the compressor through 3 lead wires. Each wire will carry identical voltage and
frequency. When checking inverter voltage output, connect the test-meter leads to any 2 of the 3
compressor lead wires. The same reading should be measured between any 2 of the 3 wires.
Note: The compressor leads must be connected to measure voltage output. If the compressor wires
are not connected, or if an open occurs in one of the 3 lead wires or in the compressor, the inverter will
stop voltage output.
The inverter controls compressor speed by frequency variation and by pulse width modulation (PWM).
Changing frequency and PWM will cause an effective voltage between 80 and 230 VAC to be received at
the compressor.
•
Low speed (1710 rpm) - 57 Hz
•
Medium speed (2100 rpm) - 70 Hz
•
High Speed (3120 rpm) - 104 Hz
The inverter receives commands from the main control board. The main control board will send a
Current-Source
Circuit Board
Current-Source
Circuit Board
(PWM) run signal between 1.5 and 3.5 VDC
effective voltage to the inverter. In the circuit
between the main control board and the inverter, a
current-source circuit board is used to amplify the
pulse width modulated voltage. The signal voltage
at the inverter should be higher than the signal
voltage sent by the main control board. The
inverter will select compressor speed (voltage
output) based on this signal. A signal voltage from
the main control board (J3-10 to J2-3) lower than
1.5 VDC or greater than 3.5 VDC indicates a faulty
main control board. The main control board will only send a run signal to the inverter when the
compressor should be on.
Note: When measuring signal voltage (from the main control board) at the inverter, disconnect the wire
harness connector at the inverter and measure the voltage at the connector.
The inverter will monitor compressor operation and if the compressor fails to start or excessive current
draw (4 amps maximum) is detected, the inverter will briefly stop voltage output. The inverter will then
make 12 consecutive compressor start attempts (once every 12 seconds). If after 12 attempts the
compressor has not started, an 8-minute count will initiate. After the 8-minute count, the inverter will
attempt to start the compressor again. If the compressor starts, normal operation will resume. If the
compressor fails to start, this process will be repeated. Removing power to the unit will reset the
inverter count. When power is restored, the inverter will attempt to start the compressor within 8
seconds.
The inverter has a built-in circuit protection to guard against damage from a failed or shorted
compressor. However, if a failed compressor is diagnosed, order a new compressor and inverter. If the
compressor fails to start after replacement, replace the inverter.
Summary of Contents for PSH23SGNAFBS Series
Page 42: ... 40 Schematic 2 1 3 ...