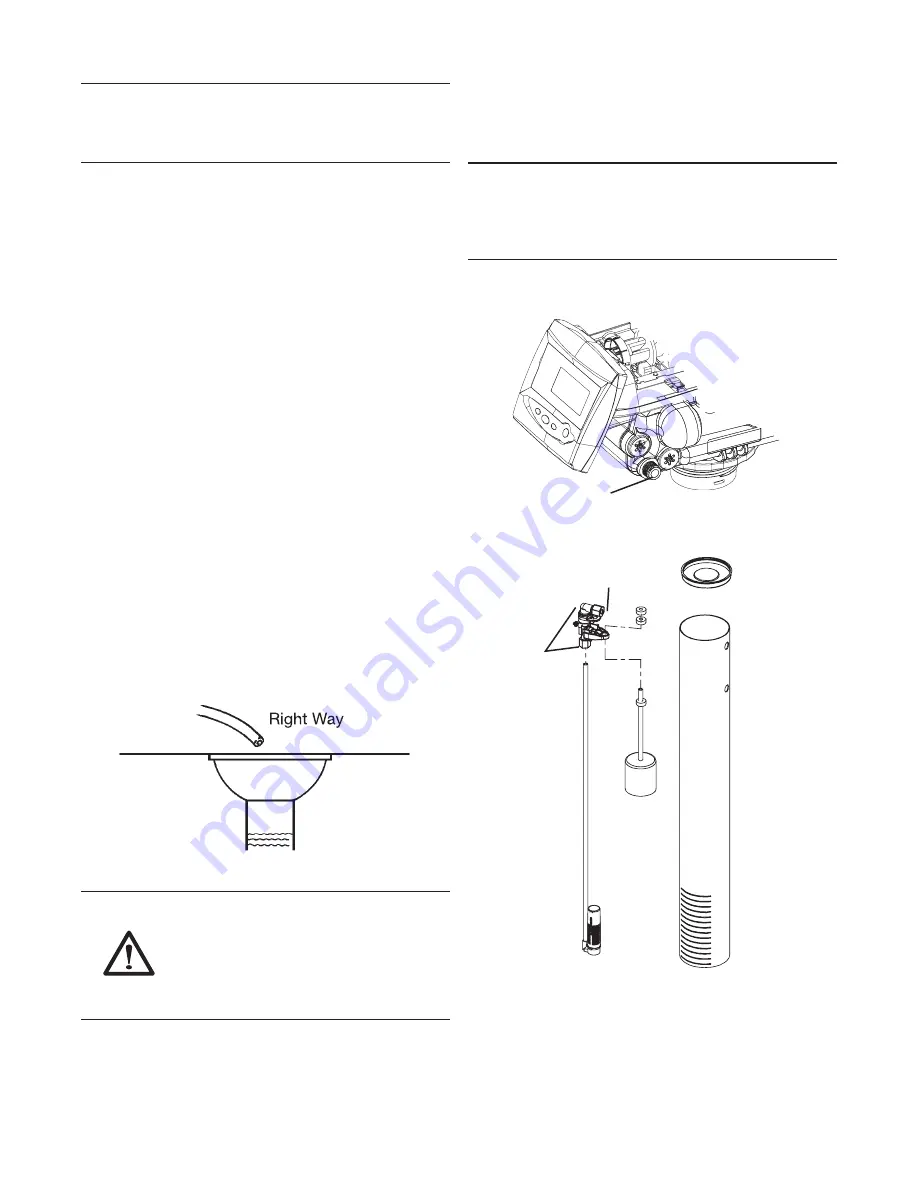
12
Drain Line Connection
Note: Standard commercial practices are expressed
here. Local codes may require changes to the following
suggestions. Check with local authorities before
installing a water conditioning system.
1. The unit should be above and not more than 20 feet
(6.1 m) from the drain. Use an appropriate adapter
fitting to connect 1/2-inch (1.3 cm) plastic tubing to
the drain line connection of the control valve.
2. If the backwash flow rate exceeds 5 gpm (22.7 Lpm)
or if the unit is located 20-40 feet (6.1 – 12.2 m) from
drain, use 3/4-inch (1.9 cm) tubing. Use appropriate
fittings to connect the 3/4-inch tubing to the 3/4-inch
NPT drain connection on valve.
3. The drain line may be elevated up to 6 feet (1.8 m)
provided the run does not exceed 15 feet (4.6 m) and
water pressure at the conditioner is not less than 40
psi (2.76 bar). Elevation can increase by 2 feet (61 cm)
for each additional 10-psi (.69 bar) of water pressure
at the drain connector.
4. When the drain line is elevated but empties into a
drain below the level of the control valve, form a
7-inch (18 cm) loop at the far end of the line so that
the bottom of the loop is level with the drain line
connection. This will provide an adequate siphon trap.
Tie or wire the hose in place at the drain point. Also
provide an air gap of at least 1-1/2 inch between the
end of the hose and the drain point.
5. When the drain empties into an overhead sewer line, a
sink-type trap must be used.
6. Secure the end of the drain line to prevent it from
moving.
Figure 9 Drain Line Connection
WARNING: Never insert drain line directly
into a drain, sewer line or trap (Figure
9). Always allow an air gap between the
drain line and the wastewater to prevent
the possibility of sewage being back-
siphoned into the conditioner.
Regenerant Line Connections
The regenerant line from the brine tank safety brine valve
(Figure 11) connects to the valve. Make sure both safety
valve tube fittings are tight. Make the connections and
hand tighten.
Note: Be sure that the regenerant line is secure and
free from air leaks. Even a small leak may cause the
regenerant line to drain out, and the conditioner will not
draw regenerant from the tank. This may also introduce
air into the valve causing problems with valve operation.
Ensure that plumber tape pipe sealant is applied to the
3/8-inch NPT regenerant line connection (Figure 10).
Regenerant Line Connection
Figure 10
Regenerant Line Connection
Figure 11 Salt Tank Safety Brine Valve and
Brine Well Assembly
Tube Fitting