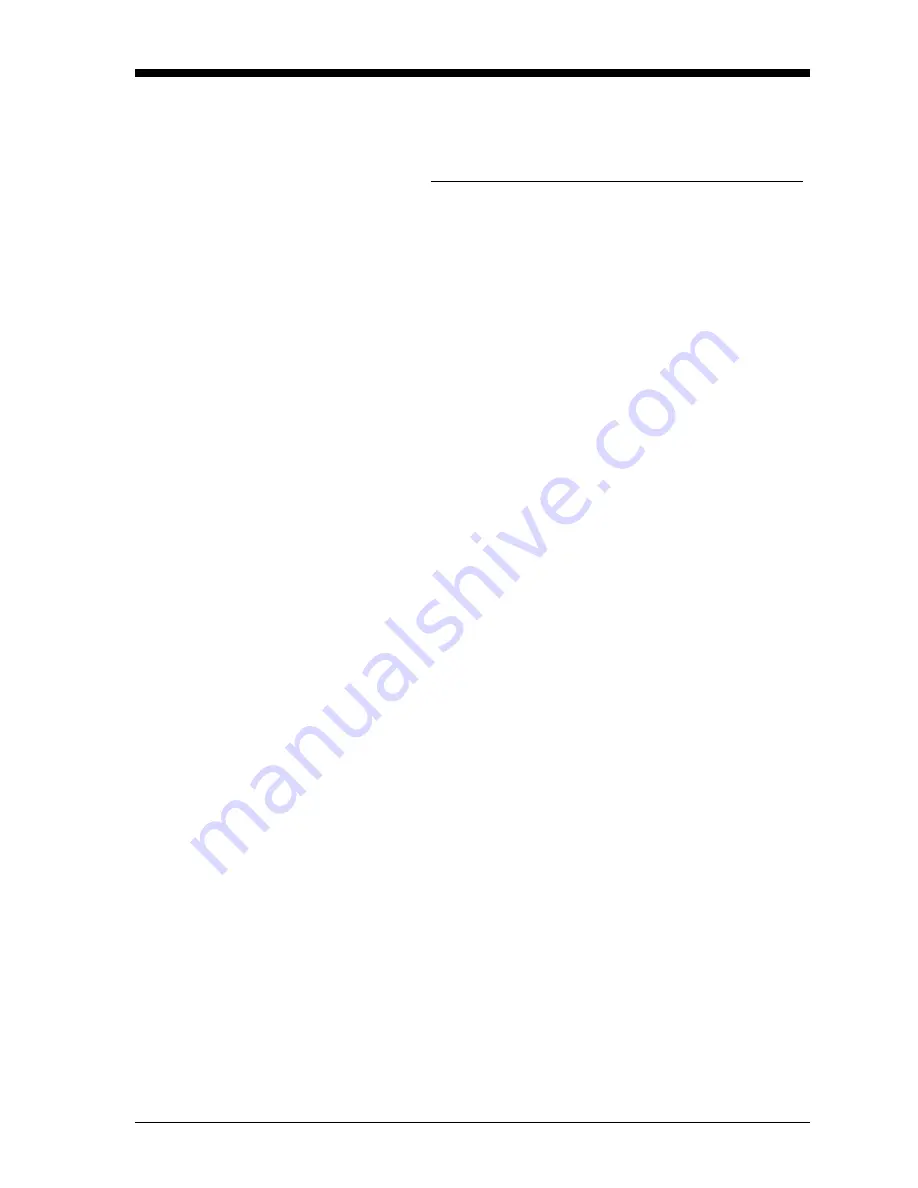
Communicating with the OPTICA Using Ethernet
G-5
January 2006
Retrieving Supported
Units
This command enables the user to retrieve different units that are
supported by the Optica and the order in which they are referenced.
Command:
http://3.112.160.36:28005/OpticaAPI.xml?GetAllLabels
Function Name:
GetAlarmTypes
Channel:
0
Response:
<?xml version="1.0" encoding="UTF-8" standalone="yes" ?>
<OpticaAPIReturn Function="
GetAllLabels
">
<channel>
0
</channel>
<sLabels>
Tdew °C
</sLabels>
<sLabels>
Tdew °F
</sLabels>
<sLabels>
%RH
</sLabels>
<sLabels>
Twet °C
</sLabels>
<sLabels>
Twet °F
</sLabels>
<sLabels>
ppmv
</sLabels>
<sLabels>
ppmw
</sLabels>
<sLabels>
Grains/lb
</sLabels>
<sLabels>
Grains/SCF
</sLabels>
<sLabels>
g/kg
</sLabels>
<sLabels>
g/m3
</sLabels>
<sLabels>
lb/Mft3
</sLabels>
<sLabels>
Kj/Kg (0)
</sLabels>
<sLabels>
Kj/Kg (32)
</sLabels>
<sLabels>
Btu/lb (0)
</sLabels>
<sLabels>
Btu/lb (32)
</sLabels>
<sLabels>
pw(mbar)
</sLabels>
<sLabels>
Tmp °C
</sLabels>
<sLabels>
Tmp °F
</sLabels>
<sLabels>
Tmp °K
</sLabels>
<sLabels>
Tmp °R
</sLabels>
<sLabels>
psia
</sLabels>
<sLabels>
mbar
</sLabels>
<sLabels>
bar
</sLabels>
<sLabels>
Pa
</sLabels>
<sLabels>
kPa
</sLabels>
<sLabels>
mmHg
</sLabels>
<sLabels>
inHg
</sLabels>
<sLabels>
KgCm2
</sLabels>
<sLabels>
DyneCm2
</sLabels>
<sLabels />
<sLabels>
UserEquation2
</sLabels>
<sLabels>
UserEquation3
</sLabels>
<retval>
GEIAPI_SUCCESS
</retval>
</OpticaAPIReturn>
Summary of Contents for Optica
Page 1: ...GE Sensing Optica General Eastern Dew Point Analyzer Operator s Manual ...
Page 11: ...Chapter 1 ...
Page 20: ...Chapter 2 ...
Page 43: ...Chapter 3 ...
Page 58: ...Chapter 4 ...
Page 80: ...Chapter 5 ...
Page 94: ...Chapter 6 ...
Page 95: ...Network Based Programming Introduction 6 1 Programming Screens 6 1 ...
Page 99: ...Chapter 7 ...
Page 109: ...Appendix A ...
Page 114: ...Appendix B ...
Page 115: ...Humidity Equations and Conversion Chart Introduction B 1 Vapor Pressure B 1 Humidity B 2 ...
Page 119: ...Appendix C ...
Page 120: ...Configuring the Serial Interface Wiring to a Personal Computer C 1 ...
Page 122: ...Appendix D ...
Page 127: ...Appendix E ...
Page 128: ...Glossary ...
Page 130: ...Appendix F ...
Page 133: ...Appendix G ...