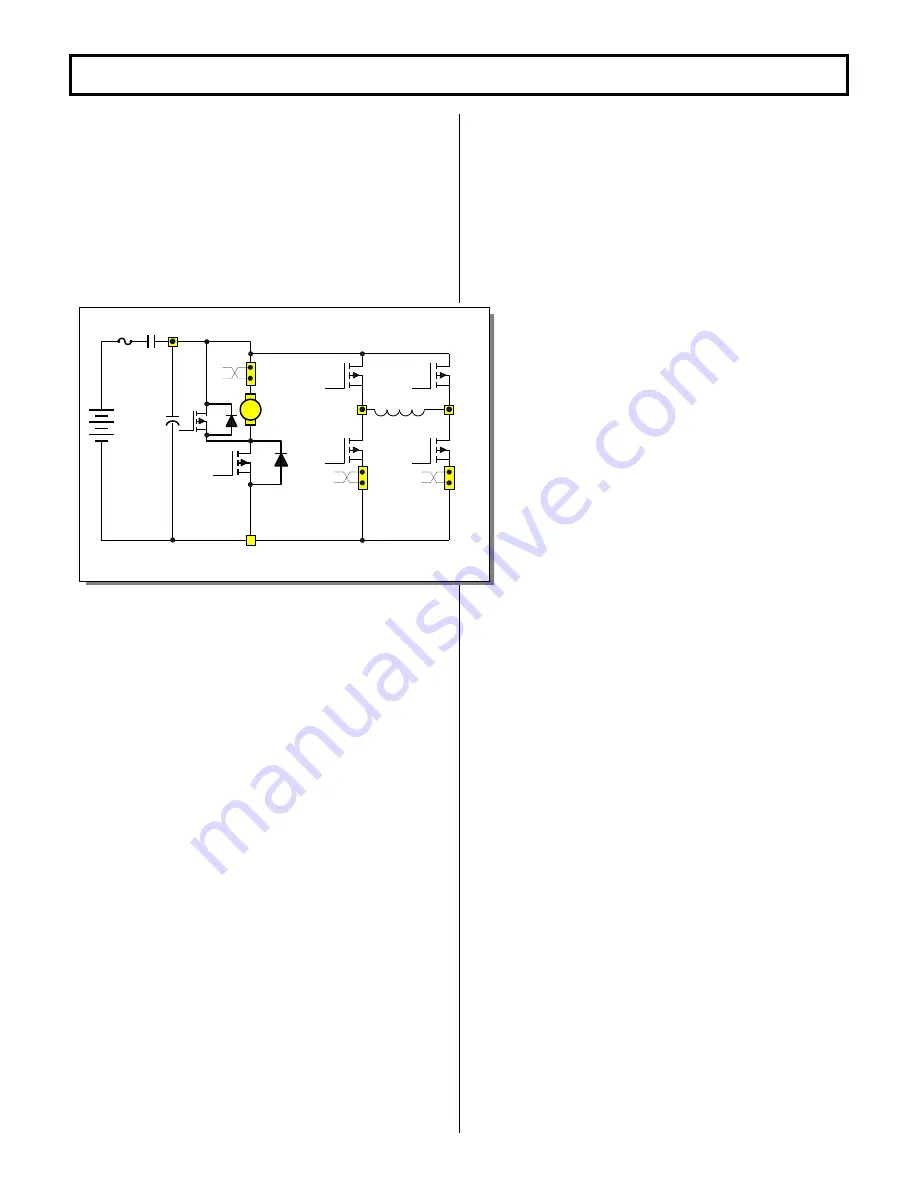
BASIC OPERATION AND FEATURES
SX TRANSISTOR CONTROL
Page
4
Section 1. 2 Solid-State Reversing
The direction of armature rotation on a shunt motor is
determined by the direction in which current flows
through the field windings. Because of the shunt
motor field, typically only requires about 10% of the
armature current at full torque, it is normally cost
effective to replace the double-pole, double-throw
reversing contactor with a low power transistor H-
Bridge circuit (Figure 4).
By energizing the transistors in pairs, current can be
made to flow in either direction in the field. The field
and armature control circuits typically operate at
12KHZ to 15KHZ, a frequency range normally above
human hearing. This high frequency, coupled with the
elimination of directional contactors, provides for very
quiet vehicle operation.
he line contactor is normally the only contactor
T
equired for the shunt motor traction circuit. This
r
ontactor is used for both pre
c
-charge of the line
apacitors and fo
c
r emergency shut down of the motor
ircuit, in case of problems that would cause a full
c
motor torque condition. The line can be energized
and de-energized by the various logic combinations of
he vehicle, i.e. activate on key, seat or start switch
t
losure, and de
c
-energize on time out of idle vehicle.
Again, these options add to the quiet operation of the
vehicle.
Section 1. 3 Flexible System Application
Because the shunt motor controller has the ability to
control both the armature and field circuits
n
i dependently, the system can normally be adjusted
or maximum system efficiencies at certain operating
f
parameters. Generally speaking, with the ability to
ndependently control the field and armature, the
i
motor performance curve can be maximized through
proper control application.
Section 1. 4 More Features with Fewer
Components
Field weakening with a series wound motor is
accomplished by placing a resistor in parallel with the
field winding of the motor. Bypassing some of the
current flowing in the field into the resistor causes the
field current to be less, or weakened. With the field
weakened, the motor speed will increase, giving the
effect of “overdrive”. To change the “overdrive
speed”, it is necessary to change the resistor
value. In a separately excited motor, independent
control of the field current provides for infinite
adjustments of “overdrive” levels, between the
motor base speed and maximum weak field. The
desirability of this feature is enhanced by the
elimination of the contactor and resistor required
for field weakening with a series motor.
With a separately excited motor, overhauling
speed limit, or downhill speed, will also be more
constant. By its nature, the shunt motor will try to
maintain a constant speed downhill. This
characteristic can be enhanced by increasing the
field strength with the control. Overhauling load
control works in just the opposite way of field
weakening, as armature rotation slows with the
increase of current in the field. An extension of this
feature is a zero-speed detect feature which prevents
the vehicle from free-wheeling down an incline,
should the operator neglect to set the brake.
Regenerative braking (braking energy returned to the
battery) may be accomplished completely with solid-
state technology. The main advantage of regenerative
braking is increased motor life. Motor current is
reduced by 50% or better during braking while
maintaining the same braking torque as electrical
braking with a diode clamp around the armature. The
lower current translates into longer brush life and
reduced motor heating. Solid state regenerative
braking also eliminates a power diode, current sensor
and contactor from the circuit.
For GE, the future is now, as we make available a
new generation of electric traction motor systems for
electric vehicles having separately excited DC shunt
motors and controls. Features that were once thought
to be only available on future AC or brushless DC
technology vehicles systems are now achievable and
affordable.
Section 2. FEATURES OF SX FAMILY OF
TRANSISTOR MOTOR CONTROLLERS
Section 2.1 Performance
Section 2.1.1 Oscillator Card Features
FUSE
LINE
CAP
ARM
F2
F1
Q3
Q4
Q5
Q6
Q1
POS
NEG
Figure 4
A1 +
A2 -
Q2
Updated Sept 2019