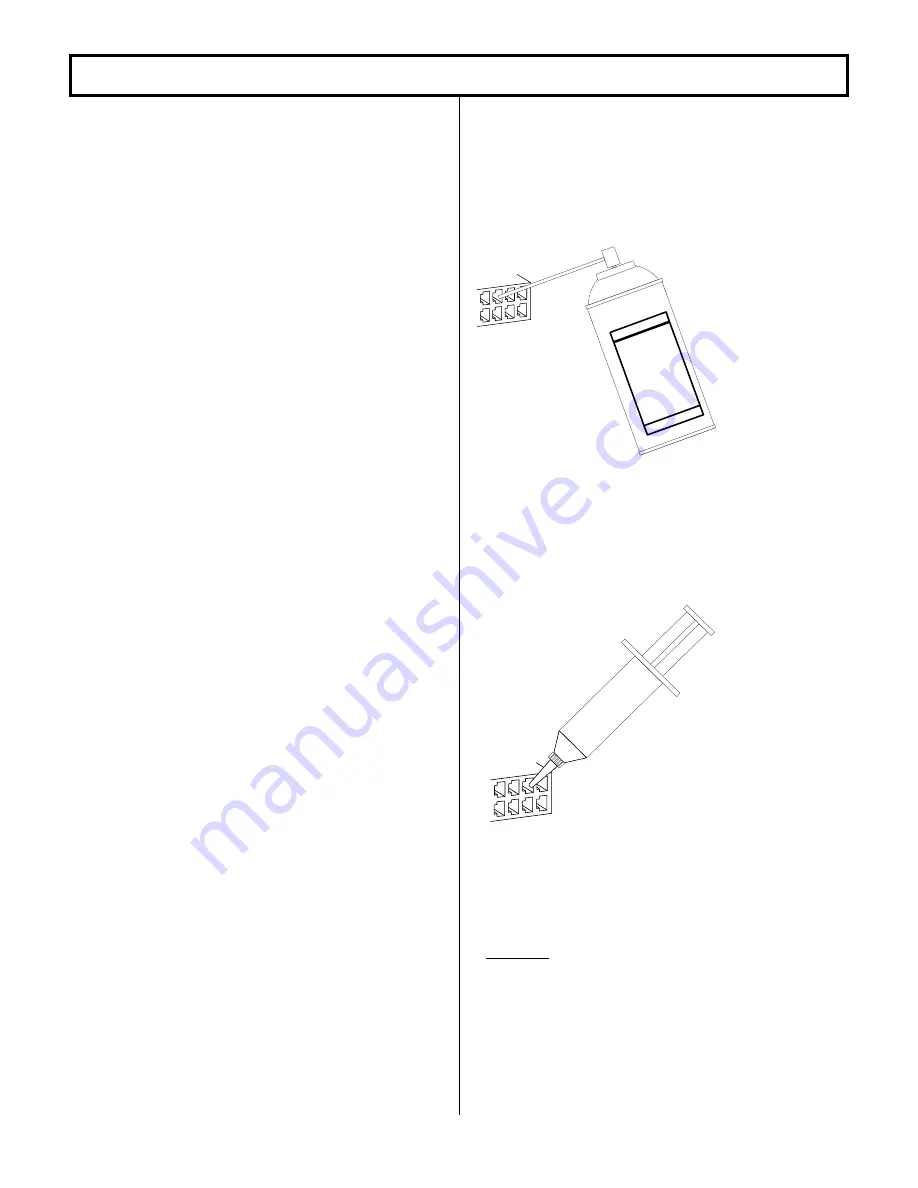
DIAGNOSTIC STATUS CODES
SX TRANSISTOR CONTROL
Page
14
July 2001
Section 4.3 Recommended Lubrication of Pins and
Sockets Prior to Installation
Beginning in January of 1999, GE implemented the addition
of a lubricant to all connections using pins and sockets on
EV100/EV200 and Gen II products. Any connection made by
GE to the A, B, X, Y, or Z plugs, includes the lubricant NYE
760G to prevent fretting of these connections during vehicle
operation.
Fretting occurs during microscopic movement at
the contact points of the connection. This movement
exposes the base metal of the connector pin which, when
oxygen is present, allows oxidation to occur. Sufficient
build up of the oxidation can cause intermittent contact
and intermittent vehicle operation. This can occur at any
similar type of connection, whether at the control or in any
associated vehicle wiring, and the resultant intermittent
contact can provide the same fault indication as actual
component failure.
The addition of the NYE 760G lubricant will prevent
the oxidation process by eliminating the access of oxygen
to the contact point. GE recommends the addition of this
lubricant to the 12 pin and 23 pin plugs of all new Gen II
controls at the time of their installation into a vehicle
When servicing existing vehicles exhibiting
symptoms of intermittent mis-operation or shutdown by the
GE control, GE recommends the addition of this lubricant to
all 12 and 23 pin plugs, after proper cleaning of the
connectors, as a preventative measure to insure fretting is
not an issue before GE control replacement. Also, for long
term reliable control operation, the plug terminals must be
maintained per these instructions with the recommended
contact cleaner and lubricant which provides a high
degree of environmental and fretting protection.
New and re-manufactured control plugs are cleaned and
lubricated prior to shipment from the factory. However, in
applications where severe vibration or high temperature
cycling and excessive humidity ( such as freezers ) are
present, it is recommended that the plug terminals be
cleaned and lubricated every year, per this instructions. In
normal applications, plug maintenance should be
performed every two years, unless intermittent problems
arise with the plugs, requiring more immediate attention.
Warning: Do not use any other cleaners or lubricants
other than the ones specified.
WARNING: Before conducting maintenance on the
vehicle, jack up the drive wheels, disconnect the battery
and discharge the capacitors. Consult the Operation and
Service Manual for your particular vehicle for details on
discharging the capacitors; this procedure differs
between SCR and Transistor controls.
1. Disconnect plug from controller or mating plug.
2. Locate the plug that contains the socket (female)
terminals. Maintenance needs only to be performed on
the plug containing the socket (female) type terminals.
Reconnecting the plugs will lubricate the pin (male)
terminals.
3. Clean each terminal using Chemtronics contact
cleaner “Pow-R-WasH CZ “ as shown in Figure 1.
Figure 1
4. Lubricate each terminal using Nye 760G lubricant as
shown in figure 2. Apply enough lubricant to each
terminal opening to completely fill each opening to a
depth of .125” minimum.
Figure 2
5. Reconnect plugs.
Reference
Cleaner
Chemtronics Pow-R-WasH CZ Contact
Cleaner
Lubricant
Nye Lubricants NYOGEL 760G
GE Plug Lub Kit Contains both above products:
328A1777G1
Chem
troni
cs
Po
w
-R
-
W
as
H
CZ
con
tact
clea
ner
ciro
zane
Ny
e
Ny
e
Ny
e
Ny
e
L
U
BR
ICA
NT
S