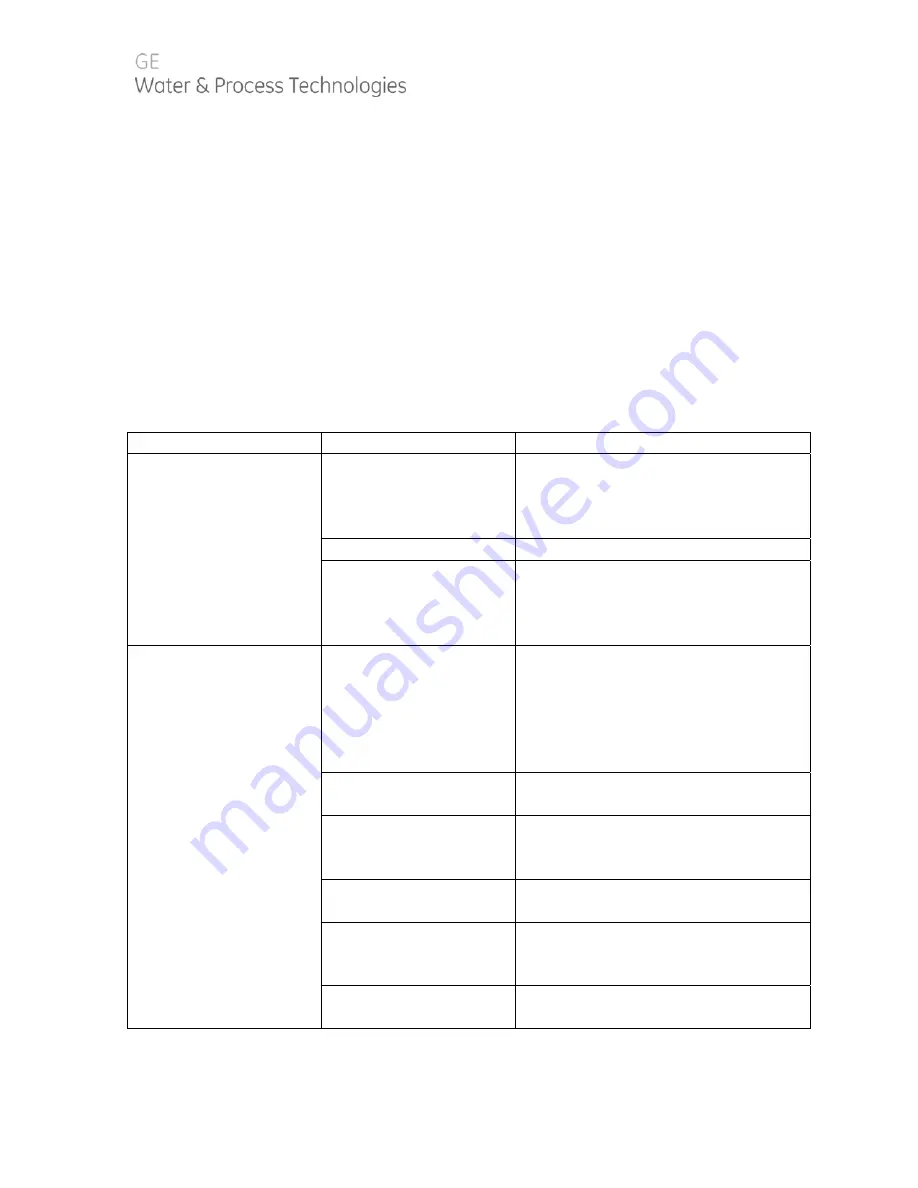
22
5.
TROUBLESHOOTING
This troubleshooting guide can assist you in identifying common operating problems
you may experience with your machine. Many of these problems can be easily
corrected by the operator, however, for those that persist or are not understood, you
should contact the GE Customer Support Center. Have the following information
available when calling the Customer Support Center:
1.
Machine installation date
2.
Model number
3.
Serial number
4.
Weekly log sheets
5.
Detailed description of problem
Table 5.
Troubleshooting Guide
Symptom (Alarm)
Possible Cause
Remedies
Low inlet pressure
Insufficient feed water
pressure
Increase the feed pressure, open the
inlet/feed valve, check for
restrictions, and consider installing a
feed water boost pump.
Clogged pre-filter
Replace the pre-filters.
Solenoid valve not
opening
Clean or replace the solenoid valve.
Clean air line for adequate pressure.
Check regulator for correct
operation and setting.
Low operating
pressure
High flow rates
Close the orifice bypass valve, check
the permeate and concentrate flow
rates and adjust if necessary.
Excessive permeate flow may
indicate improper interconnector
installation.
Pump discharge screen
(low primary pressure)
Inspect and clean.
Dirty or fouled
membranes
(low final pressure)
Clean the membranes.
Warm operating
conditions
Correct temperature.
Pump rotating
backwards
(3-phase power only)
Switch any two 3-phase leads to the
motor starter.
Pump not operating
correctly
See pump instructions.