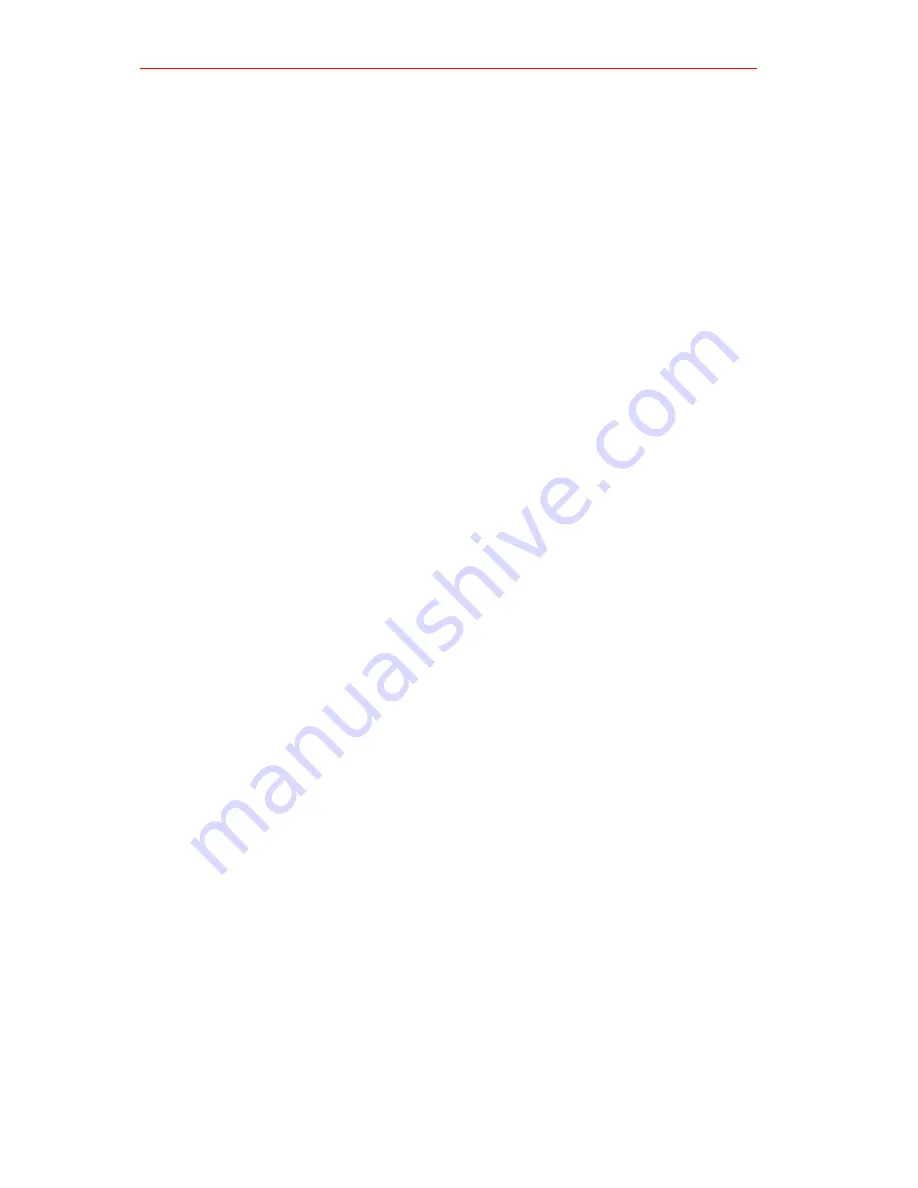
DewPro MMY245
Installation and Operation Manual
GE General Eastern
TABLE OF CONTENTS
1 General System Information __________________________________________________3
1.1 Unpacking and Inspection_________________________________________________________3
1.2 System Description_______________________________________________________________4
1.2.1 Portable
Trace
Moisture
Analyzer ______________________________________________________ 4
1.2.1.1 Versatility_____________________________________________________________________ 4
1.2.1.2 Safety ________________________________________________________________________ 4
1.2.1.3 User
Friendly
Operation__________________________________________________________ 4
1.2.2 Field
Validator _____________________________________________________________________ 5
1.3 Theory of Operation _____________________________________________________________5
1.3.1 Sensor
Theory______________________________________________________________________ 5
1.3.2 Sample System Operation_____________________________________________________________ 5
1.3.3 Software
Features ___________________________________________________________________ 6
1.3.4 Sample Conditioning Practices and Precautions____________________________________________ 6
1.3.4.1 Internal
Construction ____________________________________________________________ 6
1.3.4.2 Avoid
Liquid
Samples ___________________________________________________________ 6
1.3.4.3
Avoid High Temperatures ________________________________________________________ 6
1.3.4.4
Avoid High Pressure Samples _____________________________________________________ 6
1.3.4.5 Hazardous
Gas
Handling _________________________________________________________ 6
1.3.4.6 Avoid
Particulate
Contamination___________________________________________________ 6
1.3.4.7 Avoid
Corrosive
Chemicals _______________________________________________________ 7
1.3.4.8
Avoid Ambient Air _____________________________________________________________ 7
1.3.4.9 Piping
Recommendations_________________________________________________________ 7
Dimensions _________________________________________________________________________7
Basic Operation ________________________________________________________________8
2.1 Operating Controls ______________________________________________________________8
2.2 Display Elements ________________________________________________________________8
2.3 Basic Sampling or Spot-Checking __________________________________________________9
2.4 General Operation Practice _______________________________________________________9
2.4.1 Mapping spot check route____________________________________________________________ 10
2.4.2 Temporary
Monitoring ______________________________________________________________ 10
2.4.3 Moisture Measurement Practice _______________________________________________________ 10
2.4.3.1
Checking Dryer Performance_____________________________________________________ 10
2.4.3.2 Quality
Assurance _____________________________________________________________ 11
2.5 Instrument Setup / Programming _________________________________________________11
2.5.1 Matrix
Orientation _________________________________________________________________ 11
2.5.2 Special Functions of the Push Buttons __________________________________________________ 13
2.5.3 Function
Guide ____________________________________________________________________ 13
2.5.4 Matrix
Field
Details ________________________________________________________________ 13
2.5.5 Special Output and Input Functions ____________________________________________________ 15
2.5.6 Interconnection ____________________________________________________________________ 16
2.5.6.1 External
Power
Option__________________________________________________________ 16
2.5.6.2
External Scalable Input Option. ___________________________________________________ 16
2.5.6.3 Voltage
Inputs ________________________________________________________________ 16
2.5.6.4 Output
connections ____________________________________________________________ 17
3 Troubleshooting ___________________________________________________________17
3.1 General Troubleshooting Practice _________________________________________________17
3.2 Error Codes ___________________________________________________________________18
4 Field
Validator
Operation ___________________________________________________19