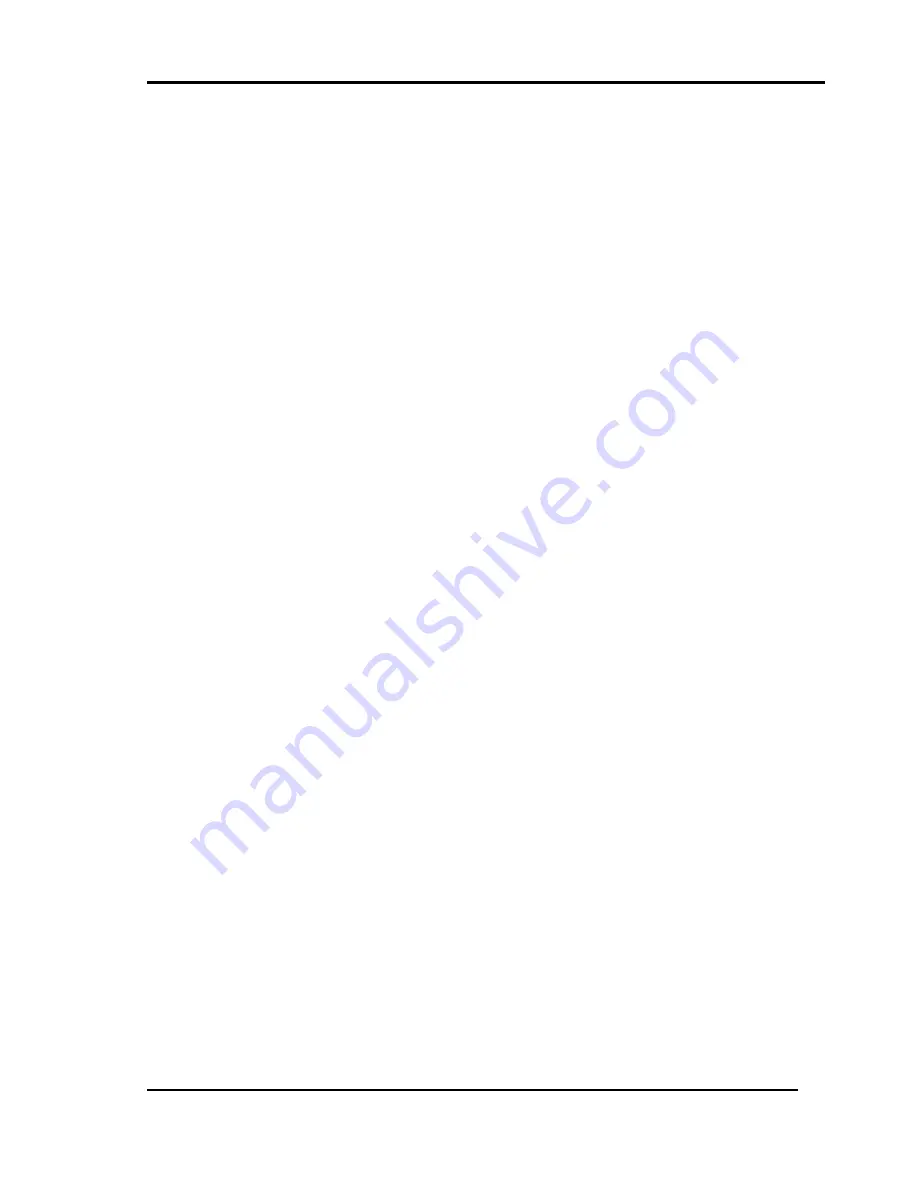
Section 5 - Appendix A - Performance Specifications
41
Frequency Response:
High Pass Corner:
3 dB corner at 8 Hz. Less than 1% error due to high
pass corner for frequency above 30 Hz.
Low Pass Corner:
Greater than 4 kHz. Less than 1% error due to low
pass corner for frequency below 4 kHz.
5.1.6 Accuracy
Percent of full scale range.
Liquid Crystal Display
±3% for 30 Hz to 4 kHz
-30%, +3% for 8 to 30 Hz.
Buffered output
±3% for 30 Hz to 4 kHz.
-30%, +3% for 8 to 30 Hz.
4 to 20 mA Interface
±3% for 30 Hz to 1 kHz.
-30%, +3% for 8 to 30 Hz.
5.1.7 LED Indicators
OK:
One constant ON green LED indicates OK condition of monitor,
transducer, and field wiring. Constant OFF indicates NOT OK
condition. OK LED flashing at 2 Hz indicates monitor has been NOT
OK, but is now OK.
Alert:
One yellow LED indicates an Alert condition. Flashing at 2 Hz
indicates an Alert condition has occurred and then gone away (only
occurs if the Alert relay is configured as nonlatching).
Danger:
One of the two red LEDs indicates a Danger condition. Flashing at 2
Hz indicates a Danger condition has occurred and then gone away
(only occurs if the Danger relay is configured as nonlatching).
Bypass:
The other red LED indicates the monitor is in BYPASS mode.