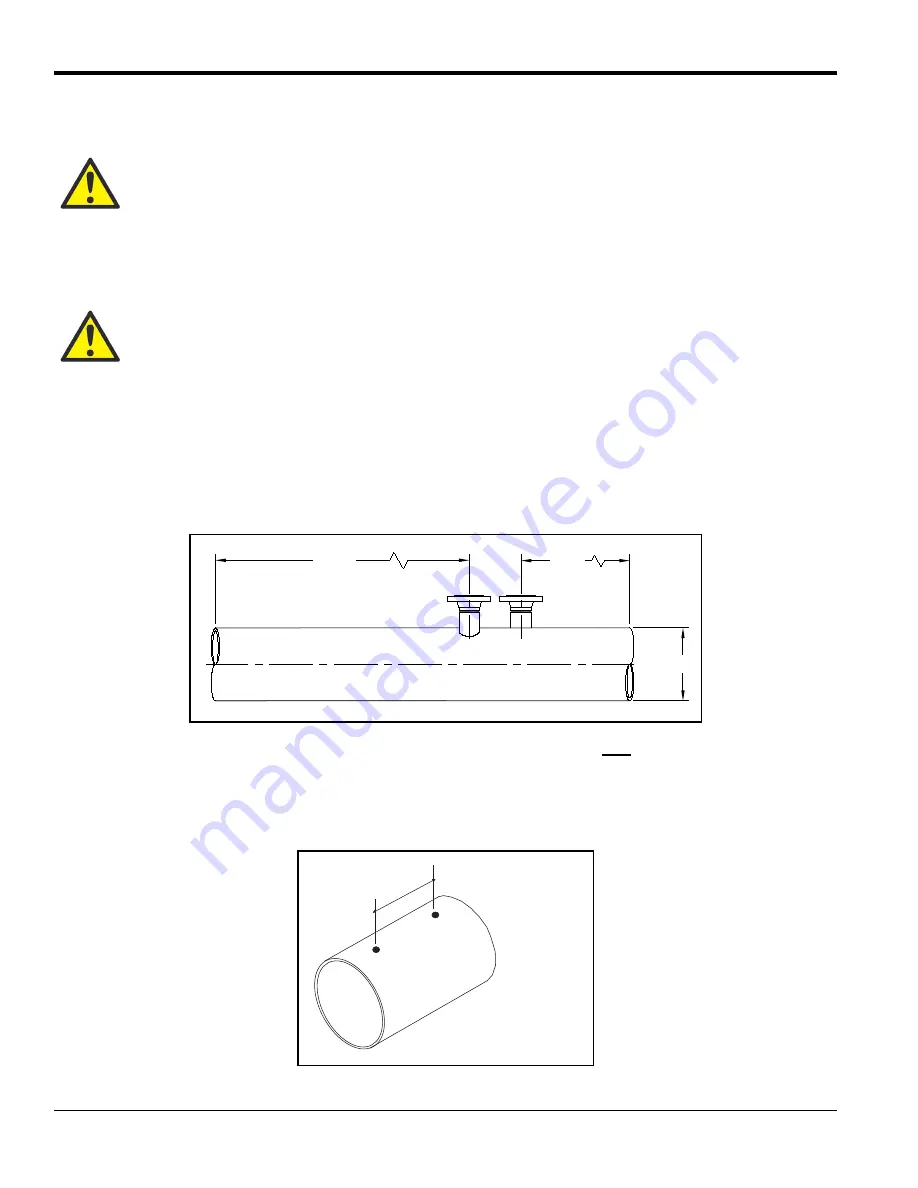
Chapter 1. Installing Pipe Nozzles
4
T5 Flare Gas Transducer Installation Guide
1.2.2 Selecting and Marking the Pipe for Nozzle Locations
1.
For optimum performance, you should select a location that has at least 20 pipe diameters of straight,
undisturbed flow upstream and 10 pipe diameters of straight, undisturbed flow downstream from the point of
measurement. Undisturbed flow means avoiding sources of turbulence such as flanges, elbows and tees;
avoiding swirl; and avoiding disturbed flow profiles. Never install the flow meter downstream of control
valves, especially butterfly valves.
Note:
If you cannot find a proper location, please consult with GE Flow Application engineering.
2.
Use a center finder device to locate the center of the pipe.
“EYEBALLING” IS NOT ADEQUATE FOR ACCURATE
FLOW MEASUREMENT!
3.
Lightly punch two marks approximately 16 in. apart on the top of the pipe, running along the center line. The
two nozzle locations will be located between these two center punch marks.
CAUTION!
Correct nozzle alignment is critical to the successful operation of the flowmeter.
Therefore, all marking, positioning and welding operations must be carried out with the utmost
attention to accuracy. Unless otherwise stated, dimensional positioning of the nozzles must be held
to a tolerance of
±
1/16 in. (±1.6 mm) relative to each other and with respect to the pipe centerline.
The angular tolerance must be held to
±
1
O
.
All hole cutting in process piping must be performed
using hot tapping equipment.
WARNING!
Be sure to adhere to all applicable safety regulations.
10D
20D
D
~ 16 in.
Top View