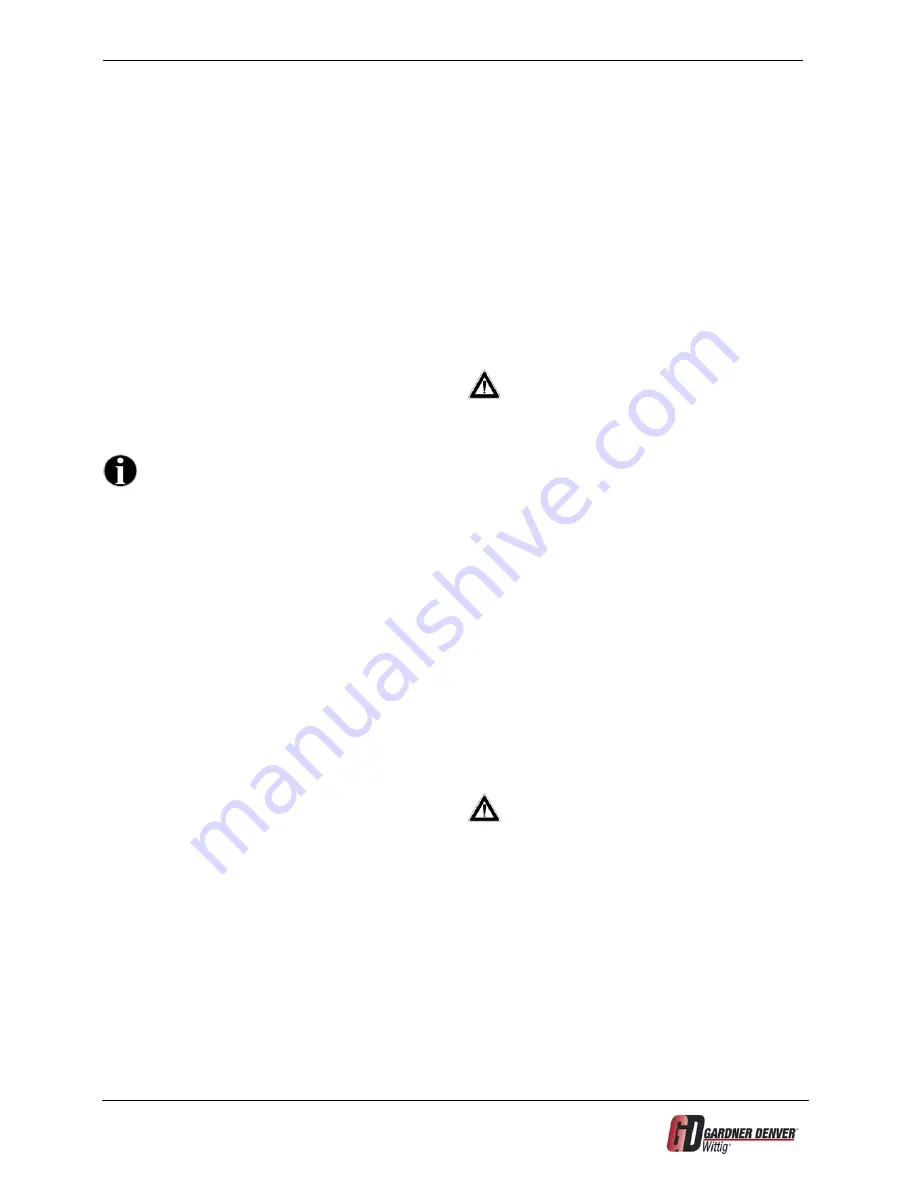
Installation
4990671000 February 2008
17
•
Thermometer
•
Pressure gauge
•
Bellows
Operating water supply line:
•
Solenoid valve for opening or closing the operating
water supply
Guard:
•
Protection against rotating parts
Protection of the machine
•
Speed monitor
•
Install drain cocks for the operating fluid to ensure
that the complete system can be drained of liquid.
Non-compliance causes forfeiture of all guar-
antee claims on Gardner Denver.
4.6.1
Vacuum gauge
To monitor the permitted operating vacuum as speci-
fied in chapter 1.1 "Machine data", a vacuum gauge is
to be installed downstream the non-return valve at the
suction side.
To measure the pressure loss in the filter, we also rec-
ommend the installation of a vacuum gauge upstream
of the filter.
4.6.2
Vacuum filter
The vacuum filter protects the machine from coarse
mechanical impurities. The vacuum filter must be in-
stalled in the suction line.
Note on installation the flow direction and required
space for replacing the filter insert.
4.6.3
Non-return valve
The non-return valve prevents the entry of water from
the pump to the intake line when the machine is not
running.
Install the non-return valve in the suction line as near
to the machine as possible. Observe the direction of
flow through the valve.
4.6.4
Thermometer
To monitor the compression end temperature, install
the thermometer in the pressure line directly down-
stream the pressure socket. For this, install a pipe cou-
pling R
1
⁄
2
". The immersion depth of the thermometers
must be equivalent to one half the diameter of the pipe.
The indicating range of the thermometers must 0 to
100 °C.
4.6.5
Safety valve
A non-shutting off safety valve shall be installed down-
stream every compressor. The valve must be dimen-
sioned and set so that the highest permitted operating
pressure cannot be exceeded by more than 10%. The
valve must be capable of blowing off the entire volume
conveyed by the liquid ring pump. This valve must also
be suitable for manual venting.
If the safety valve is handled or located improp-
erly or tampered with, there is RISK OF
EXPLOSION due to pressure and temperature
rise!
The following points must be observed when installing
the safety valve:
•
Install the valve directly downstream the liquid ring
pump, upstream of any other shutoff elements
(especially shutoff valve),
•
the component marking and seal must be visible.
•
the setting must correspond to the maximum per-
mitted operating pressure (see chapter 1.1
"Machine data"),
•
the setting must be protected against tampering,
•
the valve must not be blocked,
•
the safety valve must not be used for control of the
air volume in compression service.
Make a weekly check of the function of the
safety valve by actuating the manual vent while
the machine is running.
4.6.6
Pressure gauge
Provides pressure readings during normal machine
service. Measuring range in accordance with the oper-
ating pressure. Install directly downstream the pres-
sure connection.